SIMIT Siemens
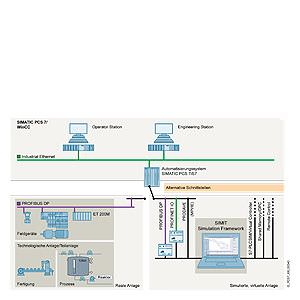
Обзор
Application and integration options of SIMIT Simulation Framework
Automation projects are subject to enormous cost pressures in both the manufacturing and process industries. The challenge is therefore to plan, install, and commission the automation of machines and systems within the shortest possible time and with a high quality.
Testing of automation with the SIMIT simulation functionality reduces the commissioning times. This is a significant contribution toward faster achievement of the planned efficiency and productivity of new plants, expansions, and modernizations.
SIMIT simulates what SIMATIC automates
The SIMIT Simulation Framework permits testing and commissioning of the project-specific user software on a partially virtual plant. To achieve this, the response of the field technology and of the technological plant/unit can be mapped and simulated in real-time or virtually. Either a real or virtual automation system is used for the control, for example, the SIMIT Virtual Controller.
SIMIT Virtual Controller instances can emulate the SIMATIC S7‑300/S7‑400 automation systems from the SIMATIC S7 and SIMATIC PCS 7 product range used in an automation project.
Many efficient tests for detection and elimination of potential faults can already be carried out before the real plant is even available, e.g.:
- Application of correct identifications
- Testing of interconnection or interlocking logic
In this manner it is possible to optimize the quality of the configuration process without a risk for the real plant.
Note:
SIMIT Simulation Framework V8.1 can be used together with SIMATIC PCS 7 V7 and V8. The SIMIT Virtual Controller V3.0 requires SIMIT Simulation Framework V8.1.
Дизайн
SIMIT Simulation Framework
SIMIT Simulation Framework runs on state-of-the-art notebooks or desktop computers with Windows 7 Professional/Ultimate (32/64-bit), and also on virtual systems (VMware ESXi Server V5.5). Flexible application is possible, and it can be integrated via open interfaces into the factory automation with SIMATIC S7 and SIMATIC WinCC or into the process automation with SIMATIC PCS 7.
Since the models can be calculated in real-time, SIMIT Simulation Framework can be linked to the real automation technology ("Hardware in the loop"). A "Software in the loop" test is also possible through virtualization of the automation system using the S7‑PLCSIM emulation software or the SIMIT Virtual Controller.
Interfacing to the real automation system is usually made via PROFIBUS DP or PROFINET IO. Interfaces (simulation units) simulate the devices on PROFIBUS DP/PROFINET IO in this case. A PRODAVE coupling can also be used for the MPI/DP or IE interface of the automation system for process data traffic with SIMIT Simulation Framework (requirement: PRODAVE driver V6.1; not included in the product package).
Further simulation models can be coupled to SIMIT Simulation Framework:
- Data exchange via standardized interfaces such as OPC DA and shared memory
- Synchronization via the remote control interface
In the case of coupling via the remote control interface, SIMIT Simulation Framework can be either the master or client (slave) for other simulations. Using virtual time management, simulations can also be implemented faster or slower than in real-time.
SIMIT Simulation Framework software packages
SIMIT Simulation Framework can be perfectly adapted to individual requirements with three software packages that are scaled in function and scope.
- SIMIT Simulation Framework Standard with
- portal view with workflow management for creation of simulation project
- Standard component library
- 3D viewer based on VRML (Virtual Reality Modeling Language)
- Interfaces for PROFIBUS DP, PROFINET IO and PRODAVE
- Interface for SIMIT Virtual Controller
- Trends and messages (TME)
- Scripting environment
- Editor for creating macro components (MCE)
- Editor for creating dynamic graphics and animations (DGE)
- Automatic Control Interface (ACI)
- Automatic generation of signal lists from SIMATIC Manager data
- Runtime for components developed with SIMIT Simulation Framework Ultimate
- SIMIT Simulation Framework Professional
All the features of SIMIT Simulation Framework Standard, plus:- Interfaces for S7-PLCSIM, OPC DA and Remote Control
- Modification of simulation model during runtime
- Simulation in virtual time
- Engineering efficiency for SIMATIC PCS 7 (SMD)
- Automatic model generation based on templates
- SIMIT Simulation Framework Ultimate
All the features of SIMIT Simulation Framework Professional, plus:- Shared memory interface for high-performance coupling
- XML interface for automatic generation of models and connections
- Development environment for custom components (CTE)
SIMIT Simulation Framework extension libraries
The following extension libraries make available specific technological components:
- SIMIT Simulation Framework FLOWNET Library:
Library for simulation of flow networks with homogeneous media (water/gases) including pressures, temperatures and flow rates - SIMIT Simulation Framework CONTEC Library:
Library for 2D simulation of material handling equipment
SIMIT Virtual Controller
SIMIT Virtual Controller
You can use SIMIT Virtual Controllers to implement testing and training systems of any size without physical hardware. This means you can test the original automation programs completely before commissioning and train operators in the practical work with the configured automation functions.
To do so, the SIMIT Simulation Framework Standard, Professional or Ultimate software packages are extended with cumulative SIMIT Virtual Controller instances. SIMIT Virtual Controller instances emulate the SIMATIC S7‑300, S7‑400 and S7‑410 automation systems used in a SIMATIC S7/SIMATIC PCS 7 automaton project on the latest notebooks or desktop computers with Windows 7 Professional/Ultimate (32/64 bit) operating system or in a virtual environment (ESXi Server V5.5).
The following products are offered for emulation:
- SIMIT Virtual Controller software for 1 controller
- SIMIT Virtual Controller software for 5 controllers
Specification/Configuration
- Almost unlimited number of SIMIT Virtual Controllers, distributed on multiple computers
- Maximum of two SIMIT Virtual Controller instances per CPU core
- Each computer with SIMIT Virtual Controller needs a SIMATIC NET instance (SIMATIC NET V12 SP2 or SIMATIC NET V8.2 SP2 HF4; not included in the scope of delivery of the SIMIT Virtual Controller, e.g. SOFTNET-IE S7 V12 or SOFTNET-IE S7 LEAN V12)
- A SIMIT Simulation Framework Standard, Professional or Ultimate is required for each simulation system (not included in the scope of delivery of the SIMIT Virtual Controller)
Функции
SIMIT Simulation Framework, Graphical User Interface (GUI)
SIMIT Simulation Framework
Component-based, signal flow oriented modeling of the plant via the graphical user interface of SIMIT Simulation Framework is based on extendable base libraries. For this, pre-defined components are selected from the library, placed on the graphic interface, connected with one another, and parameters are set. Special simulation skills are not required.
The efficient simulation is based on the abstraction at three different levels: Signals, devices (e.g. actuators and sensors) and technological response. Here, the technological response is represented mathematically and logically or by additive libraries.
Physical plant | Simulation with SIMIT Simulation Framework | |
Field equipment | Signals | Import (e.g. symbol table) |
Devices | Base library for
| |
Technological plant/unit | Technological response | Additive libraries
|
Production technology |
|
Abstraction levels of the simulation
The signal couplings can be created easily by importing the symbol table or a list of signal names. Files of the import/export wizard, control module (CM) files (SIMATIC PCS 7), or suitable Microsoft Excel files (SIMATIC S7) can be used together with simulation templates from the base library to simulate the devices.
Additive libraries support the simulation of the technological response and round off the SIMIT offer:
- FLOWNET can be used for rapid and simple simulation of the dynamic processes of pressures, flows and temperature distributions of water in pipeline networks.
- CONTEC can be used for simulation of material handling equipment.
The user can also create custom components and templates that enable effective customer-specific modeling.
Workflow to create a simulation
SIMIT Simulation Framework supports two types of virtual commissioning:
Software in the loop: Pretesting without a physical plant
When SIMIT Simulation Framework is coupled to the SIMIT Virtual Controller or the S7‑PLCSIM emulation software, the automation function can be tested in advance in the engineering office without the physical hardware – from the sensor through the automation system and back down to the actuator.
The user program is loaded in SIMATIC Manager into the automation system emulated by the SIMIT Virtual Controller or S7‑PLCSIM without modifications and started. It obtains the simulated I/O signals from the SIMIT Simulation Framework via the coupling of the emulated automation system.
Hardware in the loop: Factory Acceptance Test (FAT)
The physical automation systems are loaded with the user program for the Factory Acceptance Test (FAT). SIMIT Simulation Framework simulates the I/O signals, instrumentation, and field devices. The simulation values are sent as message frames to the automation systems via the hardware interfaces (simulation unit). When SIMIT Simulation Framework also simulates the technological response of the plant, the FAT becomes a plant test. Commissioning can be performed on the virtual process in an early phase of the project.
SIMIT Virtual Controller
SIMIT Virtual Controllers are powerful emulation systems for the SIMATIC S7‑300, S7‑400 and S7‑410 automation systems which are integrated in the SIMIT Simulation Framework. Coupling to the simulation model takes place by means of I/O signals.
Special features
- SIMIT Virtual Controller are synchronized with each other
- The automation system is loaded by means of the engineering system as in the actual automation system
- Runtime is independent of the engineering system
- Automation programs can run in virtual time (faster or slower than in real-time)
- Current states of the SIMIT Virtual Controller and the SIMIT simulation model can be saved in the shared snapshot
A separate emulation manager is supported:
- Definition of available computer hardware for virtual controllers, simulation and operator stations
- Specification of virtual controllers and assignment to computer hardware
- Configuration of communication connections between virtual controllers and operator stations (SIMATIC PCS 7, SIMATIC WinCC)
- Import of SIMATIC PCS 7 system configuration and symbol table
- Generation and distribution of configuration files
System and communication functions
For detailed information on supported SIMATIC S7/SIMATIC PCS 7 system and communication functions as well as communication services, see SIMIT manual:
http://support.automation.siemens.com/WW/view/en/93842565
Note:
The SIMIT Virtual Controller does not support, among others:
- SIMATIC PCS 7 Route Control
- BRAUMAT Classic
- Data record communication
- Named Connections via RFC1006
- Communication blocks TSEND, TRECV
Особенности
- Testing and training environments without real hardware
- Virtual controllers for emulation of automation systems
- Flexible simulation and emulation environment for projects of any size
- Synchronized simulation and emulation in real-time or virtual time
- Testing of original automation project
- Higher quality for automation engineering configuration
- Reduced commissioning time and risk due to pretesting
- No simulation configuration in the automation project
Дальнейшая информация
For additional information, refer to the Internet at
http://www.siemens.com/simit.