SITRANS CV Siemens
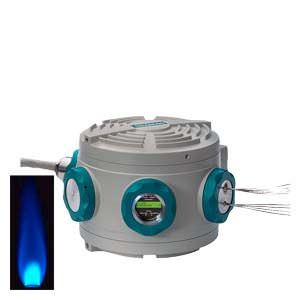
Область применения
- Analysis of natural gas in power plants:
- For quality control
- For turbine optimization
- Pipeline monitoring
- Analysis of natural gas when opening up sea beds (off-shore plants).
- Analysis of bio-natural gas in preprocessing plants
- Analysis of natural gas in liquefaction and regasification plants (LNG Regasification and Storage)
- Determination of calorific value in natural gas for power plants, in gas transfer stations, or during turbine optimization
- Analysis of calorific value in natural gas preparation plants
Обзор
The SITRANS CV gas chromatograph (GC), which is based on the innovative analytical technology of the MicroSAM, is an analyzer that has been specially developed for natural gas analysis. The device concept enables the higher and lower calorific value, standard density and Wobbe index (according to ISO, AGA 8, Gost standard) to be determined in a way that is not only cost-effective, but also quick, precise and reliable.
Дизайн
Enclosure
- EEx d version standard
- Heating adjustable from 60 to 165 °C (isothermal)
- Decentralized installation close to sampling point
Analytical modules
The compact analytical modules contain all the functional components of a chromatograph. The SITRANS CV operates with:
- Live injection
- Valveless live switching on microchip basis
- Standardized analytical modules
- Multidetection through use of up to 8 micro thermal conductivity detectors in smallest possible areas (e.g. on all column/purging outputs and injection)
Функции
Live injection
The SITRANS CV has a two-stage injection system. Using a micro injection valve, a defined quantity of sample is first brought up to the carrier gas pressure. This eliminates the pressure-dependent error in the dosing quantity present with conventional systems. In the second stage, the sample is transferred to the column by a valveless micro injection system (live dosing). The result is an "active" injection.
The injection volume can be varied time-controlled, and exactly matched to the column requirements.
Valveless live column switching
Because of the high dead volume of conventional valves, only the valveless version can be considered for a miniaturized system. In this case, the generation of differences in flow using several electronic pressure regulators at appropriate positions of the column setup causes a change in the flow directions. (The system operates according to the Wheatstone principle, but pneumatically.) The functions "Cut" and "Backflushing" can then be implemented free of dead volume.
The column system
The separation system consists of up to three separation columns connected in series. Micro TCDs or micro live circuits are installed in sequence ("inline") upstream and downstream of the individual columns. Three electronic pressure regulators supply the columns with carrier gas and carry out the switching functions (injection, backflushing and cut).
By using narrow-bore capillary columns, the separation at high resolution is carried out within a much shorter time, approx. factor 2 to 3 compared to standard capillary columns.
Electronic pressure regulators
A high pressure stability together with rapid changing rates in the hPa range are required for precise and fast switching. This is achieved in the electronic pressure regulators by means of a piezo actuator.
Detector
The micro TCDs (silicon wafer technology) work on the principle of continuous measurement of the different thermal conductivities of the carrier gas and the components to be measured.
The measurement can be carried out without falsification by avoiding catalytic effects on the heating wires and maintaining a constant flow velocity. This permits consistent in-line detection, i.e. without qualitative or quantitative losses of substances.
Modules
The standardized application modules generally feature live injection and live switching functions, detectors and separation columns.
Detector | Column 1 | Detector | Column 2 | Detector | Circuit | Column 3 | Detector | |
---|---|---|---|---|---|---|---|---|
C09 Injection | Sil5 Non-polar aromatic and aliphatic hydrocarbons | TCD | Sil5 Non-polar aromatic and aliphatic hydrocarbons | TCD | Live | Porabond Q All components except molecular filter components | TCD | |
C01 Injection | TCD | Sil5 C3, C4, C5, C6+ | TCD | PoraPLOT/Porabond Q CO2, C2, H2O | TCD | Live | Molecular filter H2, (Ar+O2), N2, C1, CO | TCD |
C13 Injection | TCD | RTX-1 C3, i-C4, n-C4, neo-C5, i-C5, n-C5 Sum C6+ as sum peak in the backflush | TCD | HayeSepN N2, CH4, CO2, C2 | TCD | Live |
Application
The SITRANS CV is a storage product. Precalibration is carried out at the factory, using helium and argon (as the carrier gas) and a calibration gas. The measured components and switching functions (live injection, backflushing, cut) are saved in the GC. The calibration process itself should be performed during commissioning on-site.
Measurements can be made within the following working ranges:
Component | Checked working range (%) | Possible working range (%) |
---|---|---|
Methane | 57 ... 100 | 50 ... 100 |
Nitrogen1) | 0 ... 22 | 0 ... 25 |
Carbon dioxide | 0 ... 12 | 0 ... 20 |
Ethane | 0 ... 14 | 0 ... 20 |
Propane | 0 ... 5 | 0 ... 15 |
i-butane | 0 ... 0.9 | 0 ... 10 |
n-butane | 0 ... 1.8 | 0 ... 10 |
Neopentane | 0 ... 0.1 | 0 ... 1 |
i-pentane | 0 ... 0.12 | 0 ... 1 |
n-pentane | 0 ... 0.12 | 0 ... 1 |
Hexane+2) | 0 ... 0.08 | 0 ... 3 |
Hexane | 0 ... 1 | |
Heptane+3) | 0 ... 1 | |
Octane | 0 ... 1 | |
Nonane+4) | 0 ... 1 | |
Helium | Concentration can be entered as a fixed value in the component list | |
H2S | < 500 ppm | No measured component |
High/low calorific value | Calculated | Calculated |
Density and relative density | Calculated | Calculated |
Wobbe index | Calculated | Calculated |
Compressibility factor | Calculated | Calculated |
Normalization factor | Calculated | Calculated |
Table 1: Measured components and performance parameters for Pos. 8_0 (master setup, standard calorific value analysis in accordance with ISO 6976-1995)
1) Any oxygen or carbon monoxide present in the sample will be detected along with the nitrogen and, therefore, taken into account when the nitrogen concentration is determined.
2) Hexane+ = group(iso/n-hexane to iso/n-nonane)
3) Heptane+ = group(iso/n-hexane) and group(iso/n-heptane to iso/n-nonane)
4) Nonane+ = group(iso/n-hexane), group(iso/n-heptane), group(iso/n-octane), group(iso/n-nonane)
Component | Possible working range (%) |
---|---|
Oxygen | 0 ... 4 |
Table 2: Measuring range of the additional measured component oxygen of the extended calorific value analysis (see article no. 7KQ3105-1)
The remark in footnote 1 about the detection of oxygen and nitrogen is not valid in the case of an extended calorific value analysis. In this case, all components from Table 1 "Measured components and performance parameters for Pos. 8_0 (master setup, standard calorific value analysis in accordance with ISO 6976-1995)" plus oxygen are detected and quantified.
For the analysis of biomethane the following components and their working ranges are measured (Table 3).
Component | Possible working range (%) | Calibration gas for biomethane measurement (%). |
---|---|---|
Methane | > 80 | 89 |
Nitrogen | < 8 | 4 |
Ethane | < 6 | 2.5 |
Carbon dioxide | < 4 | 2.5 |
Propane | < 5 | 1.0 |
Butane | < 1.2 | 0.2 |
Oxygen | < 3 | 0.2 |
2-Methylpropane (isobutane) | < 0.7 | 0.2 |
Hydrogen | < 3 | 0.2 |
Table 3: Measured components, working ranges and calibration gas for the analysis of biomethane
For analysis of natural gas with backflush summation, the following components and working ranges are measured:
Component | Possible working range (%) |
---|---|
Methane | 50 ... 100 |
Nitrogen | 0 ... 25 |
Carbon dioxide | 0 ... 20 |
Ethane | 0 ... 20 |
Propane | 0 ... 15 |
i-butane | 0 ... 10 |
n-butane | 0 ... 10 |
Neopentane* | |
i-pentane | 0 ... 1 |
n-pentane | 0 ... 1 |
Hexane+ | 0 ... 3 |
Helium | Concentration can be entered as a fixed value in the component list |
H2S | No measured component |
High/low calorific value | Calculated |
Density and relative density | Calculated |
Wobbe index | Calculated |
Compressibility factor | Calculated |
Normalization factor | Calculated |
Table 4: Component and measuring ranges for the analysis, including backflush summation
* Because the neopentane concentration is very small in practice, this component is not calibrated and is measured with the relative response factor of isopentane. For this reason, a possible working range is not indicated.
Analyses within the checked working range as well as the quality parameters resulting from these (high and low compression and normalization factors, calorific value, density, relative density and Wobbe index) correspond to the requirements listed below.
Measurements within the scope of the possible working ranges (Table 1 "Measured components and performance parameters for Pos. 8_0 (Master setup, standard analysis of calorific value in accordance with ISO 6976-1995)", right column, and Table 2 "Measuring range of the additional measured component oxygen of the extended analysis of calorific value (see article no. 7KQ3105-1)") are possible. However, checking of the repeatability and correctness has not been carried out by the official German body "Physikalisch technischer Bundesanstalt (PTB)".
Concentration range (mol.%) | Repeatability according to ISO 6974-5 (2001); molar fraction (%), absolute |
---|---|
50 < xi < 100 | 0.03 ... 0.035 |
1 < xi < 50 | 0.011 ... 0.03 |
0.1 < xi < 1 | 0.006 ... 0.011 |
xi < 0.1 | < 0.006 |
Table 5: The repeatability of the measured components complies with ISO 6974-5 (2001) – Annex B (article no. 7KQ3105-0, 7KQ3105-1)
The repeatability of the calorific value and standard density achieve a relative standard deviation of < 0.01%. SITRANS CV for the analysis of biomethane achieves a relative standard deviation of < 0.05%.
The calibration gas is an extremely important factor for consideration in terms of the MPE (maximum permissible error), and has a significant effect on the accuracy of the overall measuring system. For this reason, SITRANS CV - based on a comparative measuring procedure - can never be more accurate than the calibration gas used. Other parameters besides the accuracy data on the calibration gas certificate are important for the accuracy of a system. Examples of these include the optimum gas composition, the ambient temperatures of the calibration gas cylinders during transportation and operation, potential condensation of, for instance, higher hydrocarbons in a calibration gas cylinder, and the functionality of the sample preparation system.
Under optimum conditions, the SITRANS CV achieves an MPE of < 0.1% for the calorific value and the standard density, whereby the system for measuring biomethane produces an MPE of < 0.5%.
SITRANS CV is designed for measuring with various configurations; the calibration gases required for this purpose are shown below. (Table 6, Measurement and calibration gas components):
SITRANS CV – Overview of possible configurations and the required calibration gases | |||||
---|---|---|---|---|---|
Carrier gas | He | He | Ar | He | |
Analyzer module | C09 | C01 | C01 | C13 | |
Calorific value analysis C6+ | Calorific value analysis C6+ with oxygen | Basic Bio-CH4 | Extended calorific value analysis Bio-CH4 | C6+ backflush | |
Calculation standard | Calculation standard is ISO 6976, GOST and AGA 8 can be selected | ||||
Article No. | 7KQ 3105-0 | 7KQ 3105-1 | 7KQ 3105-2 | 7KQ 3105-2 | |
Hydrogen | - | - | - | M CR | - |
Oxygen | - | M CR | M CR | M CR | - |
Nitrogen | M CR | M CR | M CR | M CR | M CR |
Carbon dioxide | M CR | M CR | M CR | M CR | M CR |
Methane | M CR | M CR | M CR | M CR | M CR |
Ethane | M CR | M CR | - | M CR | M CR |
Propane | M CR | M CR | - | M CR | M CR |
Isobutane | M CR | M CR | - | M CR | M CR |
Butane | M CR | M CR | - | M CR | M CR |
Neopentane | M*1 | M*1 | - | - | M*1 |
Isopentane | M CR | M CR | - | - | M CR |
Pentane | M CR | M CR | - | - | M CR |
Group C6+ | M*2 CR | M*2 CR | - | - | - |
Group C6+ backflush | - | - | - | - | M*2 CR |
Extended application 7KQ 3105- B02 | |||||
Separate measurement of Group C6 and Group C7+ | M*3 CR*3 | M*3 CR*3 | - | - | - |
Separate Groups C6, C7, C8, C9 | M*4 CR*4 | M*4 CR*4 | - | - | - |
Caution! | Use of the SITRANS CV with a carrier gas different to that of the supplied solution can lead to faults and to the destruction of the analysis module. Depending on the composition of the calibration gas, external heating for the calibration gas cylinder may be necessary. | ||||
M | Measured | ||||
CR | Required as calibration component; composition see catalog PA 01 – SITRANS CV - Function | ||||
M*1 | Neopentane is measured with the response factor of isopentane; for direct calibration of neopentane: see operating instructions | ||||
M*2 | Group C6+ is measured with the relative response factor of n-hexane | ||||
M*3/CR*3 | Groups C6 and C7+ are measured separately and calibrated with n-hexane and n-heptane, respectively | ||||
M*4/CR*4 | Group C6, Group C7, Group C8, Group C9 are measured and calibrated separately |
Table 6: Overview of device versions and available measurement configurations and the calibration gas compositions required for them
SITRANS CV with SIMATIC Extension Unit
Чертеж
SITRANS CV, dimensions in mm
Особенности
Flexible installation: The rugged and compact design enables installation in even extreme areas of application, such as offshore exploration, or directly at the pipeline. The SITRANS CV has the certification required (such as explosion protection or splashwater protection) to meet the requirements of these applications.
Like the MicroSAM, the SITRANS CV consists of a basic unit and an analysis module, which, if necessary, can be replaced in as short a time as possible. Combined with low power and gas consumption, this keeps operating costs down.
Notable features of the CVControl software, which has been specially developed for calibration-related applications, includes its ease of operation and transparency.
The automatic method optimization integrated in the software increases the repeatability of the calorific value measurement and reduces the cost of ownership.
The serial RS 485/RS 232 and Ethernet interfaces enable communication with both the control system and a flow computer.
Like the MicroSAM, the unit’s high analytical capability can be attributed to narrow-bore capillary columns, live injection, live switching and in-line detection.
Технические данные
Climatic conditions | |
Permissible ambient temperature | -20 ... +55°C (depending on oven temperature) |
Permissible storage/transport temperature | -30 ... +70℃ |
Permissible relative humidity | Max. 90% |
Protection against dust and moisture | |
| IP 65 |
| NEMA 4X |
Power supply | |
Auxiliary power | 24 V DC (18.5 ... 30.2 V) |
External fuse | T2.5 A |
Power consumption, typical | 18 W |
Power consumption, maximum | 60 W |
Dimensions and weights | |
Width x depth x height | 360 x 300 x 220 mm (approx. 14" x 12" x 9") |
Weight | 15 kg (35 lb.) |
Mounting | |
Installation on | Post, pipe or wall |
Distance from wall or next chromatograph | 300 mm (12") |
Distance from ceiling or floor | 200 mm (8") |
Electromagnetic compatibility | |
Noise suppression | According to CISPR 11 / EN 55011 / DIN VDE 0875 Limit class B |
EMC immunity | According to IEC 60801/DIN VDE 0843 |
Conducted interferences on AC supply lines | |
| 2 kV |
| 1 kV |
| 2 kV |
Conducted interferences on signal lines | |
| 1 kV |
Immunity to static discharge | |
| 8 kV |
Immunity to fields | |
| 10 V/m |
Safety | |
Electrical safety | IEC 61010 / DIN VDE 0411 |
Explosion protection | ATEX and IEC Ex: II 2 G Ex d IIC T4 Gb Class I, Zone 1, Group IIB + H2 T4 Class I, Div 1, Groups B, C, D T4 Factory Sealed |
Oven | |
Number/type | 1 / isothermal |
Purging with N2 | Possible |
Dimensions (D x H) | 160 x 10 mm |
Max. heating power | 35 VA |
Temperature range | 60 … 165 °C |
Temperature stability | ± 0.1 K (60 ... 165 °C) |
Temperature accuracy | ± 3 K (60 ... 165 °C) |
Retention time variations per 10 °C change in ambient temperature | Approx. 0.3% |
Warm-up period from 30 … 100 °C | 10 minutes |
Columns and gases | |
Separating column switching | Multidimensional chromatography with backflushing and cut in live system |
Multifunctional diaphragm valve | For injection and backflushing |
Gas connections | Swagelok 1/8" |
Pressure regulators | Max. 4 single-channel electronic pressure regulators |
Solenoid valves for control of diaphragm valve | 2 NC contacts, 2 NO contacts |
Carrier gas | He, Ar Notice: The carrier gas defined for the delivered state must be used. Changing the carrier gas could destroy the thermal conductivity detectors. |
| ≥ 99.999 % (5.0) |
| < 0.1 μm |
| Degree of separation 99.99 % for 0.1 μm particles |
| < 35 ml/min |
| 500 …700 kPa (g) 600 kPa (g) recommended Important: |
Instrument air | Not required |
Sample and injection | |
Sample streams | 3 |
Calibration sample streams | 1 |
Phase | Gaseous |
Permissible sample pressure | 10 … 60 kPa above atmospheric pressure |
Sample flow | 20 … 100 ml/min |
Max. sample temperature | 120°C |
Solid components | < 0.1 μm |
Required filtration | Degree of separation 99.99 % for 0.1 μm particles |
Material with which the sample comes into contact | Stainless steel, fused silica, polyimide |
Injection | "Valveless" live injection |
| With multifunctional diaphragm valve |
| From 2 ... 50 μl |
Detectors, calibration and performance data | |
Detector type | TCD, max. 8 sensors |
Cell volume | 0.02 µl |
Calibration | Manual or automatic, single level |
Repeatability for calorific value and density | ≤ 0.01% (for natural gas) |
Accuracy for calorific value and density | ≤ 0.1% (for natural gas) |
Linear range | Typically ≥ 104 |
Cycle time | Application-dependent |
Ambient temperature influence | Negligible |
Mean Time to Repair/MTBF | < 1 hour / 3 years (without consumables) |
Electronics: Communication and analytical controller (CAC) | |
Microprocessor | Intel 586 architecture |
Flash EPROM | 128 MB |
Dynamic RAM | 64 MB |
Operating system | Windows CE 5.0 |
Software | Preinstalled. Modifications or upgrades for operation PC downloadable via network or locally |
Electronics: Realtime signal processor (RSP) | |
Microprocessor | Motorola 68376, 20 MHz |
Flash EPROM | 1 MB |
Static RAM | 1 MB |
Operating system | Forth |
Software | Preinstalled. Modifications or upgrades downloadable via internal service interface |
Interfaces | |
Communication | 1 x Ethernet 10BaseT/TCP/IP |
Control system coupling | 1 x Modbus RS 485/RS 232 RTU/ASCII |
Inputs/outputs: Basic equipment | |
Digital outputs (relay contact 0.4 A/24 V DC) | 4, 3 x samples, 1 x calibration |
Digital inputs (24 V to optocoupler) | 4, for 1 = sample flow; 2 = time synchronization; 3 = revision (results have no effect on average values); 4 = calibration |
Status indicator | |
LEDs for |
|
LCD for |
|
Recommended operator panel | |
Personal computer | Desktop or laptop |
Processor | At least Pentium III |
Clock | ≥ 800 MHz |
Interfaces | 1 x Ethernet |
Operating system | Windows XP, Windows 7 |
Software | CV Control version 1.30.0.0 and higher |
Дальнейшая информация
Notes on 7KQ3105-..
Support bracket
For easy mounting, incl. support for 8 gas connections consisting of:
- Mounting part: Dimensions 380 x 110 mm (W x H)
- Bracket for gas connection: Dimensions 146 x 110 mm (D x H), bracket on right side, mounted at right angle
Sample flow switchover
The chromatograph enables automatic selection and switchover of 3 sample flows and 1 calibration flow. The DO signal from the gas chromatograph requires an external relay for the solenoid valve. The sample preparation system can be ordered separately.
Ambient temperatures
Particularly in warmer zones, weather protection is necessary to protect the SITRANS CV against direct solar radiation. The chromatograph is designed as standard for temperatures from -20 to +55 °C. A version in a thermostatically-controlled casing is also available as an option for temperatures outside these limits.
Communication
SITRANS CV has a serial interface (RS 485/RS 232) for MODBUS communication (RTU/ASCII). Modbus mapping can be flexibly used (see manual for more information).
The operator input is by means of another separate interface via Ethernet (TCP/IP).
Other serial and analog (4 to 20 mA) interfaces are optionally possible using an external solution package (see Article No. 7KQ2160).
Documentation
The documentation includes a SITRANS CV Manual and CVControl Operating Manual in English and German. The documents can be found on the enclosed CD. Safety manuals in all EU languages are also available on the CD.
CVControl operating software
The operating software (language: English or Russian) is included in the scope of supply. Windows XP or Windows 7 must be installed on the computer in order to install this software.
Application
A general system check is made of the basic unit and the integrated application module. The module and basic unit are described in the manual. In addition to the standard configuration, additional country-specific and user-specific sub-configurations are available. The performance record ex works contains the analysis check, including a repeatability record (4h test).
The chromatograph is preconfigured; In addition, three CD-ROMS are enclosed:
- SITRANS CV Software (including manuals and CVControl Operating Instructions)
- Country-specific sub-setups
- Parameter backup
Article numbers Pos. 8_0: Applications – Standard calorific value analysis
This application comprises the standard calorific value analysis. The chromatograph''s measurement method is set at the factory, using a synthetic natural gas mixture. The performance parameters specified in Table 5 and the criteria explained in the subsequent text apply to the individual components in Table 1 and their physical variables.
The calculation of the calorimetric variables is possible according to the following standards: ISO 6976-95, GOST, AGA 8, where the former is preset. The reference states for the combustion and for the gas volume that must be specified for calculation purposes are preset to the standard state (Tb=25 °C, Tn = 0 °C) and can be easily changed to other reference states during commissioning using the operating software (Tb= operating temperature, Tn= standard temperature).
The CVControl software provides the energy units BTU/ft3, KWh/m3 and MJ/m3.
Article numbers Pos. 8_1: Applications – extended calorific value analysis with oxygen
This position includes the extended calorific value analysis of the components and possible working ranges from Table 1. Oxygen is measured in addition to the listed components (see Table 2).
A carrier gas dry filter (article no. filter set A5E00400116) on the mounting bracket of the SITRANS CV or enclosed separately is used as standard for this measurement.
The remarks concerning oxygen and CO in footnote 1 of Table 1 are no longer applicable to this position. The information concerning calculation and performance parameters are identical to Pos. 8_0.
Important:
For correct operation of SITRANS CV in accordance with Pos. 8_0 and 8_1, all measured components must be present in the calibration gas. The calibration gases listed in the table "Recommended calibration gases for Pos. 8_0 and 8_1" are recommended (also see Table 6):
Component | Pos. 8_0 (mol%) | Pos. 8_1 (mol%) |
---|---|---|
Oxygen | 0.5 | |
Nitrogen | 4 | 4 |
Carbon dioxide | 1.5 | 1.5 |
Methane | 88.9 | 88.4 |
Ethane | 4 | 4 |
Propane | 1 | 1 |
Isobutane | 0.2 | 0.2 |
n-butane | 0.2 | 0.2 |
Neopentane | 0.05 | 0.05 |
Isopentane | 0.05 | 0.05 |
n-pentane | 0.05 | 0.05 |
n-hexane |
Запрос коммерческого предложения× Сообщение отправлено× В ближайшее время сообщение будет обработано. Письмо с номером обращения отправлено на Ваш почтовый ящик. Спасибо за то, что выбрали Первый ZIP! Что-то пошло не так...× К сожалению, наша система расценила Ваше сообщение как спам. Если это произошло по ошибке, пожалуйста, обратитесь к нам по электронной почте. Приносим извинения за возможные неудобства. |