ATEX II 2G control unit Siemens
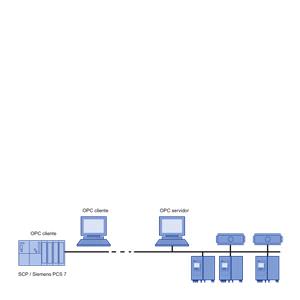
Обзор
EEx p safety equipment (purging unit)
The EEx p safety equipment to be connected to the analyzer must have at least the following features:
- Adjustable pre-purging phase; purging gas flow must be approximately 50 l/min
- Limitation of purging gas pressure during the pre-purging phase: < 165 hPa
- "Leakage compensation" or "Continuous purging"
- Connection for purging gas lines with Ø 10 mm or Ø 3/8" from and to the analyzer
- Pressure after pressure reducer
- 0.2 to 0.4 MPa (leakage compensation)
- 0.2 to 0.3 MPa (continuous purging)
- Max. permissible input pressure 0.6 MPa
- Relay contacts for all-pole isolation of the analyzer supply voltage
- Connection option for a key-operated switch and a pressure switch (intrinsically-safe circuits)
- Device version "Leakage compensation": Connection option for a pressure switch with intrinsically-safe scan
The Bartec control unit APEX 2003.SI/B meets the requirements for "Pressured enclosure with leakage compensation or continuous purging" in accordance with EN 50016 or ATEX guidelines, and can be used as explosion-proof equipment in Zones 1 and 2.
The purging unit ensures that in a closed enclosure, any explosive gases will be purged and then a pressure higher than the surrounding atmosphere will be generated and maintained.
A non-hazardous area is thus created in the enclosure in which electrical devices can be installed that are not themselves explosion-proof. After commissioning, a distinction is made between the pre-purging phase and the operating phase:
The pre-purging phase is necessary to ensure that any explosive atmposphere entering during the standstill time does not become a hazard; the enclosure must therefore be purged with protective gas (air from a non-hazardous area or inert gas) before commissioning.
Additional function
By connecting additional pressure sensors, the internal pressure of the enclosure is maintained at a pressure higher than that of the sample gas by means of a proportional valve. During the prepurging phase the purging gas flow is max. 4 100 Nl/h with an internal enclosure pressure of 50 hPa.
4 programmable relay inputs (8 relay contacts) are available to separate the data lines.
During the operating phase, the pressure inside the enclosure must be maintained at a level at least 50 Pa higher than that of the surrounding atmosphere. If the internal pressure drops below the defined minimum value, safety equipment must shut down the entire electical supply to the EEx-p enclosure autonomously (including the possible data lines) .
Enclosures frequently contain accessories to which flammable gases or sometimes also flammable gas mixtures are fed via a separate gas path. This is the case with gas analyzers, for example. In this case, it must be ensured that the pressure of the protective gas is always more than 50 Pa higher than the pressure of the sample gas.
After mounting the control device APEX 2003.SI/B on the EEx-p enclosure, and after connecting the mains power and the protective gas, the control module regulates and monitors the flow of purging gas automatically during the pre-purging phase, and the internal enclosure pressure during the operating phase.
If the minimum operating pressure of the enclosure is exceeded and if flow through the pressure monitoring module is sufficient, the pressure sensors forward the sensor module signals to the control module.