PM240 Power Modules Siemens
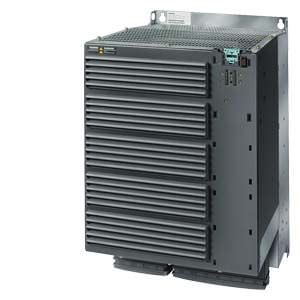
Обзор
SINAMICS G120 PM240 Power Module, frame size FSF
PM240 Power Modules have an integrated braking chopper.
The permissible cable lengths between inverter and motor are limited. Longer cables can be used if output reactors are connected (see load-side power components).
Line reactors are available to minimize line harmonics as well as voltage and current peaks (see line-side components).
Power Modules with integrated line filter class A are suitable for connection to TN systems. Power Modules without integrated line filter can be connected to grounded TN/TT systems and non-grounded IT systems.
Note:
Shield plates and shield connection kits are available. These can be used in the wiring installation for the Control Units and Power Modules to ensure that it complies with EMC guidelines.
For further information, see Shield connection kits and shield plates for Control Units and Power Modules in section Supplementary system components.
Характеристика
Derating data, PM240 Power Modules
Pulse frequency
Rated power | Rated output current in A for a pulse frequency of | ||||
---|---|---|---|---|---|
400 V | 460 V | ||||
kW | hp | 2 kHz | 4 kHz | 6 kHz | 8 kHz |
90 | 125 | – | 178 | 151.3 | 124.6 |
110 | 150 | 205 1) | 178 | – | – |
132 | 200 | 250 1) | 202 | – | – |
1) The pulse frequency can only be switched over from 4 kHz (default) to 2 kHz for the low overload (LO) duty cycle.
Ambient temperature
Low overload (LO) for PM240 Power Modules, frame size FSF
High overload (HO) for PM240 Power Modules, frame size FSF
Note:
The operating temperature ranges of the Control Units should be taken into account. The temperature ranges are specified in the section Technical specifications under Control Units.
Installation altitude
Permissible line supplies depending on the installation altitude
• Installation altitude up to 2000 m above sea level
- Connection to every supply system permitted for the inverter
• Installation altitudes between 2000 m and 4000 m above sea level
- Connection to a TN system with grounded neutral point
- TN systems with grounded line conductor are not permitted
- The TN line system with grounded neutral point can also be supplied using an isolation transformer
- The phase-to-phase voltage does not have to be reduced
Note:
The connected motors, power elements and components must
be considered separately.
Permissible output current as a function of the installation altitude for PM240 Power Modules, frame size FSF
Интеграция
All PM240 Power Modules have the following connections and interfaces:
- PM‑IF interface to connect the Power Module to the Control Unit. The Power Module also supplies power to the Control Unit using an integrated power supply
- Motor connection using screw terminals or screw studs
- 2 PE/protective conductor connections
- Terminals DCP/R1 and R2 for connection of an external braking resistor
- Control for the Brake Relay for controlling a motor brake
Connection diagram for PM240 Power Module with or without integrated line filter class A
Available optional power and DC link components
The following line-side power components, DC link components and load-side power components are optionally available in the appropriate frames sizes for the Power Modules:
| Frame size |
---|---|
| FSF |
PM240 Power Module with integrated braking chopper | |
Line-side power components | |
Line filter class A | F/S 1) |
Line reactor | S |
DC link components | |
Braking resistor | S |
Load-side power components | |
Output reactor | S |
Sine-wave filter | S |
S = Lateral mounting
F = Power Modules available with and without integrated filter class A
1) PM240 Power Modules, frame size FSF, 110 kW and higher, are available only without an integrated filter class A. An optional line filter class A for lateral mounting is available instead.
General design information
- With lateral mounting, the line-side components have to be mounted on the left side of the inverter,
and the load-side components on the right side. - Braking resistors have to be mounted directly on the control cabinet wall due to heating issues.
Recommended installation combinations of the inverter and optional power and DC link components
Power Module | Lateral mounting | |
---|---|---|
Frame size | Left of the inverter | Right of the inverter |
FSF | Line filter and/or | Output reactor or |
Maximum permissible cable lengths from the motor to the inverter when using output reactors or sine-wave filters depending on the voltage range
The following load-side power components in the appropriate frame sizes are optionally available for the Power Modules and result in the following maximum cable lengths:
PM240 Power Module, frame size FSF, with integrated braking chopper | Maximum permissible motor cable lengths (shielded/unshielded) in m |
---|---|
Without output reactor/sine-wave filter | 50/100 |
With optional output reactor | 200/300 |
With optional sine-wave filter | 200/300 |
Derating data
The following inverter output currents can still be achieved with long motor cables without output reactor and sine-wave filter.
Derating for PM240 Power Modules, frame size FSF, with a shielded motor cable.
Rated power 1) | Frame size | Rated output current Irated 2) | Base-load current IH | Motor connection cross-section | Current derating of the output current as a % of the base-load current for the cable lengths (MOTION-CONNECT) | ||||
---|---|---|---|---|---|---|---|---|---|
400 V | 460 V | ||||||||
kW | hp |
| A | A | mm2 | 50 m | 100 m | 150 m | 200 m |
90 | 125 | FSF | 178 | 145 | 95 | 100 % | 100 % | 100 % | 95 % |
1) Rated power based on the rated output current Irated. The rated output current Irated is based on the duty cycle for low overload (LO).
2) The rated output current Irated is based on the duty cycle for low overload (LO). These current values are valid for 400 V and are specified on the rating plate of the Power Module.
Чертеж
PM240 Power Modules, degree of protection IP20
Principle dimension drawing and drill pattern for PM240 Power Modules, frame size FSF, degree of protection IP20, without integrated line filter class A
Principle dimension drawing and drill pattern for PM240 Power Modules, frame size FSF, degree of protection IP20, with integrated line filter class A
Increased depth:
• When the CU230P-2 Control Unit is plugged on, the depth increases by 58 mm (2.28 in).
• When the IOP is plugged on, the depth increases by a further 25 mm (0.98 in)
• When the BOP‑2 is plugged on, the depth increases by a further 15 mm (0.59 in)
Технические данные
General technical specifications
Power Modules | PM240 |
---|---|
System operating voltage | 380 ... 480 V ±10 % 3 AC |
Grid requirement | >25 >100 line reactor recommended |
Input frequency | 47 ... 63 Hz |
Output frequency |
|
| 0 ... 550 Hz |
| 0 ... 240 Hz |
Pulse frequency | 75 kW (HO): 4 kHz as of 90 kW (HO): 2 kHz Higher pulse frequencies up to 16 kHz, see derating data |
Power factor λ | 0.7 ... 0.85 |
Offset factor cos φ | 0.95 |
Inverter efficiency | 95 ... 98 % |
Output voltage, max. As % of input voltage | 95% |
Overload capability |
|
Note: When the overload capability is used, the base-load current IL is not reduced. | 90 kW (LO): 110 kW and higher (LO): |
Note: When the overload capability is used, the base-load current IH is not reduced. | 75 kW (HO): 90 kW and higher (HO): |
Electromagnetic compatibility |
|
Possible braking methods |
|
Degree of protection | IP20 |
Operating temperature |
|
| 0 ... 40 °C (32 ... 104 °F) without derating |
| 0 ... 50 °C (32 ... 122 °F) without derating |
Storage temperature | -40 ... +70 °C (-40 ... +158 °F) |
Relative humidity | <95 % RH, condensation not permissible |
Cooling | Internal ventilation, power units with increased air cooling by built-in fans |
Installation altitude | Up to 1000 m (3281 ft) above sea level without derating, |
Protection functions |
|
Rated short-circuit current SCCR (Short-Circuit Current Rating) 1) | 65 kA |
Compliance with standards | UL, cUL, CE, C-Tick, SEMI F47 |
CE marking | According to Low-Voltage Directive No. 2006/95/EC, EMC Directive 2004/108/EC |
1) Applies to industrial control panel installations acc. to NEC Article 409 or UL 508A/508C.
PM240 Power Modules
Line voltage 380 ... 480 V 3 AC | PM240 Power Modules | |||
---|---|---|---|---|
Without integrated line filter | 6SL3224-0BE37-5UA0 | 6SL3224-0BE38-8UA0 | 6SL3224-0BE41-1UA0 | |
With integrated line filter | 6SL3224-0BE37-5AA0 | – | – | |
Output current at 50 Hz 400 V 3 AC |
|
|
|
|
| A | 178 | 205 | 250 |
| A | 178 | 205 | 250 |
| A | 145 | 178 | 205 |
| A | 290 | 308 | 375 |
Rated power |
|
|
|
|
| kW (hp) | 90 (125) | 110 (150) | 132 (200) |
| kW (hp) | 75 (100) | 90 (125) | 110 (150) |
Rated pulse frequency | kHz | 4 | 2 | 2 |
Efficiency η |
| >0.97 | >0.97 | >0.97 |
Power loss 3) at rated current | kW | 2.376 | 2.274 | 2.964 |
Cooling air requirement | m3/s (ft3/s) | 0.15 (5.3) | 0.15 (5.3) | 0.15 (5.3) |
Sound pressure level LpA (1 m) | dB | <65 | <65 | <65 |
24 V DC power supply for Control Unit | A | 1 | 1 | 1 |
Rated input current 4) |
|
|
|
|
| A | 186 | 210 | 250 |
| A | 204 | 245 | 299 |
Length of cable to braking resistor, max. | m (ft) | 15 (49) | 15 (49) | 15 (49) |
Line supply connection U1/L1, V1/L2, W1/L3 |
| M8 screw studs | M8 screw studs | M8 screw studs |
| mm2 | 25 ... 120 | 25 ... 120 | 25 ... 120 |
Motor connection U2, V2, W2 |
| M8 screw studs | M8 screw studs | M8 screw studs |
| mm2 | 25 ... 120 | 25 ... 120 | 25 ... 120 |
DC link connection, connection for braking resistor DCP/R1, DCN, R2 |
| M8 screw studs | M8 screw studs | M8 screw studs |
| mm2 | 25 ... 120 | 25 ... 120 | 25 ... 120 |
PE connection |
| On housing with M8 screw | On housing with M8 screw | On housing with M8 screw |
Motor cable length 5), max. |
|
|
|
|
| m (ft) | 50 (164) | 50 (164) | 50 (164) |
| m (ft) | 100 (328) | 100 (328) | 100 (328) |
Degree of protection |
| IP20 | IP20 | IP20 |
Dimensions |
|
|
|
|
| mm (in) | 350 (13.78) | 350 (13.78) | 350 (13.78) |
|
|
|
|
|
| mm (in) | 634 (24.96) | 634 (24.96) | 634 (24.96) |
| mm (in) | 934 (36.77) | – | – |
|
|
|
|
|
| mm (in) | 316 (12.44) | 316 (12.44) | 316 (12.44) |
| mm (in) | 387 (15.24) | 387 (15.24) | 387 (15.24) |
Frame size |
| FSF | FSF | FSF |
Weight, approx. |
|
|
|
|
| kg (lb) | 36 (79.4) | 39 (86) | 39 (86) |
| kg (lb) | 52 (115) | – | – |
1) The rated output current Irated and the base-load current IL are based on the duty cycle for low overload (LO).
2) The base-load current IH is based on the duty cycle for high overload (HO).
3) Typical values. You can find additional information on the Internet at http://support.automation.siemens.com/WW/view/en/94059311
4) The input current depends on the motor load and line impedance. The input currents apply for rated power loading (based on Irated) for a line impedance corresponding to uK = 1 %. These current values without line reactor are specified on the rating plate of the Power Module.
5) Max. motor cable length 25 m (82 ft) (shielded) for PM240 Power Modules with integrated line filter to maintain the limit values acc. to EN 61800‑3 Category C2.