SINUMERIK Safety Integrated Siemens
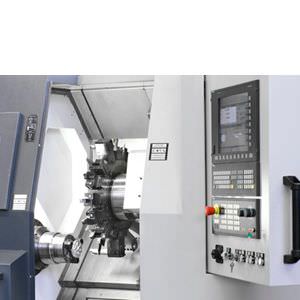
Обзор
SINUMERIK Safety Integrated provides integrated safety functions that support the implementation of highly effective personnel and machine protection. The safety functions comply with the requirements of Category 3 as well as Performance Level PL d according to EN ISO 13849-1 and safety integrity level SIL 2 according to EN 61508. Consequently, important functional safety requirements can be implemented easily and economically. Available functions include, among others:
- Functions for safety monitoring of velocity and standstill
- Functions for establishing safe boundaries in work spaces and protected spaces, and for range recognition
- Direct connection of all safety-related signals and their internal logical linkage
Функции
The safety functions are available in all modes and can communicate with the process using safety-oriented input/output signals.
They can be implemented for each individual axis and spindle:
Safety Integrated system-integrated (option)
- Safe shutdown
Ensures safe transition of the drive from motion to standstill when a monitoring device or a sensor (e.g. a light barrier) responds. - Safe braking ramp (SBR)
Monitoring of the speed curve. The speed must be reduced after a stop request has been issued - Safe operating stop (SBH)
Monitors drives for standstill. The drives remain fully functional in closed loop position control - Safe standstill (SH)
Suppression of drive pulses, providing safe electronic interruption of the energy supply - Safely limited speed (SLS)
Monitoring of configurable speed limits - Safety-related output n < nx
Safe speed recognition of a drive - Safe software limit switches (SE)
Variable traversing range limitations - Safe software cams (SN)
Range recognition - Safety-related input/output signals (SGE/SGA)
Interface with process - Safe programmable logic (SPL)
Direct connection of all safety-related signals and their internal logical operation - Safe brake management (SBM)
- 2-channel braking signal (integrated in the SINAMICS S120 Motor Module) (SBC)
- Cyclic brake test (SBT)
- Safety-related communication via standard bus
- Connection of distributed I/O for process and safety signals via PROFIBUS/PROFINET using the PROFIsafe protocol.
- Safety-related CPU - CPU communication via PROFIBUS or PROFINET
- Integrated acceptance test
Partially automated acceptance test for all safety-related functions. Simple operation of the test process, automatic configuration of Trace functions and automatic generation of an acceptance record.
Safety Integrated drive-based (basic version)
- Safe Torque Off (STO)
Suppression of drive pulses, providing safe electronic interruption of the energy supply - Safe Brake Control (SBC)
Safe (2-channel) control of a holding brake (integrated in the SINAMICS S120 Motor Module) - Safe Stop 1 (SS1)
Safe shutdown of a drive followed by STO
Интеграция
Requirements:
- SINUMERIK 840D sl
- SINAMICS S120 in booksize format
- The encoder systems used must meet the requirements of SINUMERIK Safety Integrated.
- The measuring circuit cables must comply with the SINAMICS S120 specifications.
- Sensor/actuator integration with PROFIsafe I/Os
- Fail-safe modules:
- SIMATIC ET 200M
- SIMATIC ET 200S
- SIMATIC ET 200SP
- SIMATIC ET 200eco
- SIMATIC ET 200pro
- DP/AS-i F-Link
- SIMATIC S7 F Configuration Pack available as a download at:
http://support.automation.siemens.com/WW/view/en/15208817 - For the integrated acceptance test
- SinuCom software tool (can run on PC/PG)
Конфигурация
Only one SI-Basic and one SI-Comfort option can be ordered for each SINUMERIK 840D sl. If a machine with Safety Integrated requires up to 4 safe inputs and 4 safe outputs, the SI Basic option can be ordered. If five or more safe inputs/outputs are required, the SI-Comfort option should be ordered.
Ordering example 1:
The machine has 2 axes and 1 spindle, which are to be monitored by Safety Integrated. 4 safe inputs and 3 safe outputs are required. The following options must be ordered:
Number | Article No. | Remark |
---|---|---|
1 | 6FC5800-0AM63-0YB0 | SI-Basic |
2 | 6FC5800-0AC70-0YB0 | SI-axis/spindle package |
Ordering example 2:
The machine has 5 axes and 1 spindle, which are to be monitored by Safety Integrated. 9 safe inputs and 5 safe outputs are required. The following options must be ordered:
Number | Article No. | Remark |
---|---|---|
1 | 6FC5800-0AM64-0YB0 | SI-Comfort |
5 | 6FC5800-0AC70-0YB0 | SI-axis/spindle package |
Особенности
- High level of safety:
Complete implementation of the safety functions in Category 3/SIL 2/PL d - High level of flexibility:
Supports the implementation of practically sound safety and operating concepts - Extremely cost-effective:
Reduced hardware and installation costs - Enhanced availability:
Absence of interference-susceptible electromechanical switching elements
Дальнейшая информация
The Safety Integrated functions of the SINUMERIK are generally certified by independent institutes. An up-to-date list of certified components is available on request from your local Siemens office. If you have any questions relating to certifications that have not been completed, please ask your Siemens contact.
Encoder systems
If you require information about the use of suitable encoder systems with SINUMERIK Safety Integrated, please contact your local Siemens office.