Manage MyTools Siemens
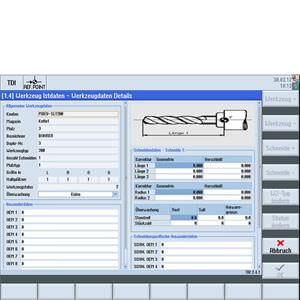
Обзор
Network-wide tool management
SINUMERIK Integrate for production Manage MyTools offers an integrated software solution for tool cycle management from adjustment, through tool storage, to the machine.
This ensures that machine downtime due to missing tools is reduced through preventive tool planning. Clock times and downtimes with regard to tools are optimized.
Tool organization across the entire production area is one of the central tasks of CNC production. Requirements are:
- Smooth processes within tool cycles
- Cost transparency
- Inventory and cost overview
SINUMERIK Integrate for production Manage MyTools makes this potential for rationalization transparent, and provides functions that help realize the potential savings identified. SINUMERIK Integrate for production Manage MyTools has the correct connection concepts and functions for providing a complete overview of the tools used and a closed tool data cycle in the production area for:
- Single machines, flexible transfer lines, or a complete machine park
- Highly automated SINUMERIK CNCs
- Integration of tool setting stations or cross-factory tool management systems.
Функции
All SINUMERIK Integrate for production Manage MyTools functions are designed so that they can operate on a single machine or within networked, interconnected systems, e.g., they can display an overview of all actual tool data on a single machine or a central control system.
Scope of functions of single, non-networked machines
- Actual tool data
- Service life can be varied from 10 to 100%
- Block tool and tool details
- Import/export file interface
- Tool transfer
Thanks to the consistent design as a client-server solution and the use of communication mechanisms, it is possible to vary the distribution of the modules in the network and to access them from any position. This means that up-to-date information can always be accessed wherever it is needed.
The following functions are available:
- Availability of actual tool data throughout the network
- Operator-prompted loading and unloading with TO data import from the tool setting station
- Planning of tool demand based on current magazine assignment
- Statistical evaluations of tool use
- Interface for connecting external management systems
- All available functions combined on a single server and network-wide operation of client-based interfaces
- Stand-alone non-network-compatible function package for tool planning and connection to tool setting stations
Интеграция
Requirements:
- It is assumed that the standard tool management option is installed in the SINUMERIK CNCs. SINUMERIK CNCs without standard tool management or with tool management that is specific to the machine manufacturer must be connected for the specific project.
- In the case of third-party control systems, the manageable tool data is reduced to a simplified tool data structure. The basic requirements are that the control panel must be Windows-based, the CNC must be accessible via Ethernet, and the interface must be OPC-compatible. Third-party controls are connected for the specific project.
- If tools stored in tool cabinets are to be recorded and managed, a user interface for loading and unloading the tools must be assigned to the respective storage location, e.g. a Windows PC integrated in the network.
Особенности
- Cost transparency in the tool cycle
- Detailed inventory overview, cost overview and productivity potentials in tool management
- The modularity of the SINUMERIK Integrate for production Manage MyTools modules permits optimized customer-oriented and demand-oriented applications.
- Use scalable from a single machine up to a complete machine park.