CU310-2 Control Units for single-axis drives Siemens
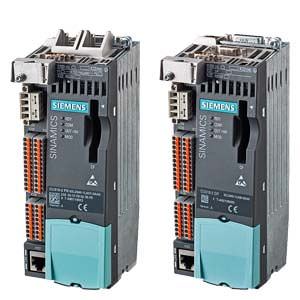
Обзор
CU310‑2 PN and CU310‑2 DP Control Units
The CU310‑2 Control Unit that is designed for the communication and open-loop/closed-loop control functions of a SINAMICS S120 (AC/AC) is combined with the PM340 Power Module to create a powerful single-axis drive. PROFINET (PN) and PROFIBUS (DP) variants are available for fieldbus communication.
CompactFlash Card for CU310-2 Control Units
The CompactFlash card contains the firmware and parameter settings. The CompactFlash card is plugged into the appropriate slot on the CU310‑2 Control Unit.
A CU310-2 Control Unit can perform the communication, open-loop and closed-loop control functions for one Power Module. The performance expansion is not required in this case.
In addition to the firmware, the CompactFlash card also contains licensing codes which are required to enable firmware options.
Currently, the following firmware options can be ordered in addition to the article number:
- Safety Integrated Extended Functions, order code F01
- High output frequency 1), order code J01
- DCB Extension, order code U01
The firmware option can also be enabled on-site, for example, if the Safety Integrated Extended functions should be enabled later. You will need the serial number of the CompactFlash card and the Article No. of the firmware option to be enabled. With this information, you can purchase the associated license code from a license database and enable the firmware option. The license code is only valid for the CompactFlash card declared and cannot be transferred to other CompactFlash cards.
1) For more information, visit http://support.automation.siemens.com/WW/view/en/104020669
Дизайн
The CU310-2 Control Unit features the following connections and interfaces as standard:
- Fieldbus interface
- CU310‑2 PN: 1 PROFINET interface with 2 ports
(RJ45 sockets) with PROFIdrive V4 profile - CU310‑2 DP: 1 PROFIBUS interface with PROFIdrive V4 profile
- CU310‑2 PN: 1 PROFINET interface with 2 ports
- 1 DRIVE-CLiQ socket for communication with the DRIVE-CLiQ motor or other DRIVE-CLiQ devices (e.g. Sensor Modules or Terminal Modules)
- 1 encoder evaluation for evaluating the following encoder signals
- Incremental encoder TTL/HTL
- SSI encoder without incremental signals
- 1 PE/protective conductor connection
- 1 connection for the electronics power supply via the 24 V DC power supply connector
- 1 temperature sensor input (KTY84‑130 or PTC)
- 3 parameterizable, fail-safe (can be used with firmware version 4.5 and higher) digital inputs (isolated) or alternatively 6 parameterizable digital inputs (isolated).
The fail-safe digital inputs can be routed, i.e. they can be routed via PROFIsafe to a higher-level controller. - 5 parameterizable digital inputs (isolated)
- 1 parameterizable, fail-safe (can be used with firmware version 4.5 and higher) digital output (floating) or alternatively 1 digital output (floating) 1)
- 8 parameterizable bidirectional digital inputs/outputs (non-floating) 1)
- 1 analog input, either ±10 V (resolution 12 bit + sign) or ±20 mA (11 bit + sign)
- 1 Ethernet interface (socket RJ45) for commissioning and diagnostics
- 1 slot for the CompactFlash card on which firmware and parameters are stored
- 1 PM‑IF interface for communication with the Power Modules in blocksize format
- 3 test sockets and one reference ground for commissioning support
- 1 interface to the BOP20 Basic Operator Panel
The status of the CU310-2 Control Unit is indicated via multi-color LEDs.
A BOP20 Basic Operator Panel can also be snapped directly onto the CU310‑2 Control Unit for diagnostic purposes, for example.
As the firmware and parameter settings are stored on a plug-in CompactFlash card, the Control Unit can be changed without the need for software tools.
1) In order to use the digital outputs, a 24 V supply voltage must be connected to terminal X124.
Интеграция
The CU310‑2 Control Unit drives Power Modules in blocksize format via the PM‑IF interface. DRIVE‑CLiQ motors or Sensor Modules (SMC) can also be connected to the integrated DRIVE‑CLiQ socket to permit the operation of motors without a DRIVE‑CLiQ interface.
With the BOP20 Basic Operator Panel, parameters can be changed directly on the device. The BOP20 Basic Operator Panel can also be snapped onto the CU310‑2 Control Unit during operation to perform diagnostics.
The CU310‑2 Control Unit and other connected components are commissioned and diagnosed with the STARTER commissioning tool. The CU310‑2 Control Unit requires a CompactFlash card with firmware V4.4 or higher.
A CU310‑2 PN Control Unit communicates with the higher-level control system using PROFINET IO and the PROFIdrive V4 profile.
The SINAMICS S120 drive system with the CU310‑2 PN Control Unit then assumes the function of a PROFINET IO device and can perform the following functions:
- PROFINET IO device
- 100 Mbit/s full duplex
- Supports real-time classes of PROFINET IO:
- RT (Real-Time)
- IRT (Isochronous Real-Time), minimum send cycle 500 μs
- Connects to controls as PROFINET IO devices using PROFIdrive compliant with Specification V4
- Standard TCP/IP communication for engineering processes with the STARTER commissioning tool and for accessing the integrated web server
- Integrated 2‑port switch with two RJ45 sockets based on the ERTEC ASIC. The optimum topology (line, star, tree) can therefore be configured without additional external switches.
A 24 V supply voltage must be connected to terminal X124 for the digital outputs to be used. A CompactFlash card with firmware version V4.4 or higher is a mandatory requirement for operation of the CU310‑2 Control Unit.
Connection example of a CU310‑2 Control Unit
Технические данные
PROFINET: | CU310‑2 Control Unit 6SL3040-1LA01-0AA0 |
---|---|
Power requirement, max. At 24 V DC, | 0.35 A for CU310‑2 + 0.5 A for PM340 Power Module |
Conductor cross-section, max. | 2.5 mm2 |
Fuse protection, max. | 20 A |
Digital inputs | In accordance with IEC 61131-2 Type 1 5 floating digital inputs 8 bidirectional non-floating digital inputs/digital outputs 3 parameterizable, fail-safe digital inputs (floating) or alternatively 6 parameterizable digital inputs (floating) 5 bidirectional floating digital inputs/outputs |
| -3 ... +30 V |
| -3 ... +5 V |
| 15 ... 30 V |
| 10 mA |
|
|
| 50 μs |
| 100 μs |
|
|
| 5 μs |
| 50 μs |
| 1.5 mm2 |
Digital outputs (continuously short-circuit-proof) | 8 bidirectional non-floating digital outputs/digital inputs |
| 24 V DC |
| 500 mA |
| |
| 150 μs/400 μs |
| 75 μs/100 μs |
| 1.5 mm2 |
Analog input | The analog input can be switched between current input and voltage input |
| -10 ... +10 V; Ri > 100 kΩ Resolution: 12 bit + sign (with respect to the maximum range that can be resolved -11 ... +11 V) |
| -20 ... +20 mA; Ri > 250 Ω Resolution: 11 bit + sign (based on -22 ... 22 mA) Max. range that can be resolved: -44 ... +44 mA |
Encoder evaluation |
|
|
|
| 570 Ω |
| 16 mA |
| 24 V DC/0.35 A or 5 V DC/0.35 A |
| 300 kHz |
| 100 ... 250 kbaud |
| 30 bit |
|
|
| 100 m (328 ft) (only bipolar signals permitted) 3) |
| 100 m (328 ft) for unipolar signals 300 m (984 ft) for bipolar signals 3) |
| 100 m (328 ft) |
Power loss | <20 W |
PE connection | M5 screw |
Dimensions |
|
| 73 mm (2.87 in) |
| |
| 191 mm (7.52 in) |
| 187 mm (7.36 in) |
| 75 mm (2.95 in) |
Weight, approx. | 0.95 kg (2.09 lb) |
Approvals, according to | cULus |
1) The specified delay times refer to the hardware. The actual reaction time depends on the time slot in which the digital input or output is processed.
2) In order to use the digital outputs, an external 24 V power supply must be connected to terminal X124.
3) Signal cables twisted in pairs and shielded.
Дальнейшая информация
Firmware version
The firmware version is encoded as follows in the Article No. printed on the CompactFlash card:
Article No.: | 6SL3054‑0❑❑00‑1BA0 | |
---|---|---|
Firmware version |
4 | ↑ E |
Version |
.4 .5 .6 .7 | ↑ E F G H |
Example:
A CompactFlash card with firmware version V4.7 and a safety license for a CU310‑2 PN Control Unit are required:
Article No.: 6SL3054-0EH00-1BA0-Z
F01