Technical definitions Siemens
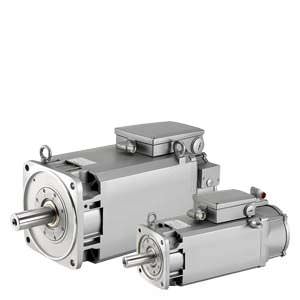
Обзор
Regulations, standards and specifications
The motors comply with the appropriate standards and regulations, see table below.
As a result of the fact that in many countries the national regulations have been completely harmonized with the international IEC 60034‑1 recommendation, there are no longer any differences with respect to coolant temperatures, temperature classes and temperature rise limits.
General specifications for rotating electrical machines | DIN IEC 60034‑1 |
Terminal designations and direction of rotation for electrical machines | DIN IEC 60034‑8 |
Types of construction of rotating electrical machines | DIN IEC 60034‑7 |
Cooling methods of rotating electrical machines | DIN IEC 60034‑6 |
Degrees of protection of rotating electrical machines | DIN IEC 60034‑5 |
Vibration severity of rotating electrical machines | DIN IEC 60034‑14 |
Noise limit values for rotating electrical machines | DIN IEC 60034‑9 |
Cylindrical shaft extensions for electrical machines | DIN 748 part 3/DIN IEC 60072 |
The motors listed below are UL-approved by Underwriters Laboratories Inc. and also comply with Canadian cUR standards:
SIMOTICS S‑1FK7/1FT7/SIMOTICS T‑1FW3/1FW6/SIMOTICS M‑1PH8 (without brake)/SIMOTICS L‑1FN3/1FN6.
Degrees of protection for AC motors
A suitable degree of protection must be selected to protect the machine against the following hazards depending on the relevant operating and environmental conditions:
- Ingress of water, dust and solid foreign objects
- Contact with or approach to rotating parts inside a motor
- Contact with or approach to live parts.
Degrees of protection of electric motors are specified by a code. This comprises 2 letters, 2 digits and, if required, an additional letter.
IP (International Protection)
Code letter designating the degree of protection against contact and the ingress of solid foreign objects and water
0 to 6
1st digit designating the degree of touch protection and protection against ingress of solid foreign objects
0 to 8
2nd digit designating the degree of protection against ingress of water (no oil protection)
W, S and M
Additional code letters for special degrees of protection
Most motors are supplied with the following degrees of protection: | ||||
---|---|---|---|---|
Motor | Degree of protection | 1st digit: | Protection against foreign objects | 2nd digit: |
Internally cooled | IP23 | Protection against finger contact | Protection against medium-sized, solid foreign objects above 12 mm ∅ | Protection against spray water up to 60° from the vertical |
Surface-cooled | IP54 | Complete protection against accidental contact | Protection against harmful dust deposits | Splash water from any direction |
IP55 | Jet-water from any direction | |||
IP64 | Complete protection against accidental contact | Protection against dust ingress | Splash water from any direction | |
IP651) | Jet-water from any direction | |||
IP671) | Motor under specified pressure and time conditions under water |
1) DIN VDE 0530 Part 5 or EN 60034 Part 5 specifies that there are only 5 degrees of protection for the first digit code and 8 degrees of protection for the second digit code in relation to rotating electrical machinery. However, IP6 is included in DIN 40050 which generally applies to electrical equipment.
Recommended degrees of protection for AC motors
When cooling lubricants are used, protection against water alone is inadequate. The IP rating should only be considered here as a guideline. The motors may have to be protected by suitable covers. Attention must be paid to providing suitable sealing of the motor shaft for the selected degree of protection for the motor (for 1FT7: degree of protection IP67 and flange 0).
The table can serve as a decision aid for selecting the proper degree of protection for motors. A permanent covering of liquid on the flange must be avoided when the motor is mounted with the shaft extension facing upwards (IM V3, IM V19).
Liquids | General workshop environment | Water/ |
---|---|---|
Effect | ||
Dry | IP64 | – |
Water-enriched environment/increased humidity | – | IP64 |
Mist | IP65 | |
Spray | – | IP65 |
Jet | – | IP67 |
Splash/brief immersion/constant inundation | – | IP67 |
Radial eccentricity tolerance of shaft in relation to housing axis
(refers to cylindrical shaft extensions)
Shaft height | Tolerance N | Tolerance R | Tolerance SPECIAL |
---|---|---|---|
SH | mm (in) | mm (in) | mm (in) |
28/36 | 0.035 (0.0014) | 0.018 (0.0007) | ‑ |
48/63 | 0.04 (0.0016) | 0.021 (0.0008) | ‑ |
80/100/132 | 0.05 (0.0020) | 0.025 (0.0010) | 0.01 (0.0004) |
160/180/225 | 0.06 (0.0024) | 0.03 (0.0012) | 0.01/ ‑ / ‑ |
280 | 0.07 (0.0028) | 0.035 (0.0014) | ‑ |
355 | 0.08 (0.0031) | 0.04 (0.0016) | ‑ |
Concentricity and axial eccentricity tolerance of the flange surface to the shaft axis
(referred to the centering diameter of the mounting flange)
Shaft height | Tolerance N | Tolerance R | Tolerance SPECIAL |
---|---|---|---|
SH | mm (in) | mm (in) | mm (in) |
28/36/48 | 0.08 (0.0031) | 0.04 (0.0016) | ‑ |
63/71/80/100 | 0.10 (0.0039) | 0.05 (0.0020) | ‑/0.03/0.04 (‑/0.0012/0.0016) |
132/160/180/225 | 0.125 (0.0049) | 0.063 (0.0025) | 0.04/0.04/ ‑ / ‑ (0.0016/0.0016/ ‑ / ‑) |
280/355 | 0.16 (0.0063) | 0.08 (0.0031) | ‑ |
Vibration severity and vibration severity grade A according to IEC 60034‑14
The vibration severity is the RMS value of the vibration velocity (frequency range from 10 to 1000 Hz). The vibration severity is measured using electrical measuring instruments in compliance with DIN 45666.
The values indicated refer only to the motor. These values can increase as a result of the overall system vibrational behavior due to installation.
Vibration severity limit values for shaft heights 20 to 132
The speeds of 1800 rpm and 3600 rpm and the associated limit values are defined in accordance with IEC 60034-14. Speeds of 4500 rpm and 6000 rpm and the specified values are defined by the motor manufacturer.
The motors maintain vibration magnitude grade A up to rated speed.
Vibration severity limit values for shaft heights 160 to 355
Balancing according to DIN ISO 8821
In addition to the balance quality of the motor, the vibration quality of motors with mounted belt pulleys and coupling is essentially determined by the balance quality of the mounted component.
If the motor and mounted component are separately balanced before they are assembled, then the process used to balance the belt pulley or coupling must be adapted to the motor balancing type. The following different balancing methods are used on motors of types SIMOTICS M‑1PH8:
- Half-key balancing
- Full-key balancing
- Plain shaft extension
The letter H (half key) or F (full key) is printed on the shaft extension face to identify a half-key balanced or a full-key balanced SIMOTICS M‑1PH8 motor.
SIMOTICS S‑1FT7/1FK7 motors with fitted key are always half-key balanced.
In general, motors with a plain shaft are recommended for systems with the most stringent vibrational quality requirements. For full-key balanced motors, we recommend belt pulleys with two opposite keyways, but only one fitted key in the shaft extension.
Vibration stress, immitted vibration values
The following maximum permissible vibration stress limits at full functionality apply only to the SIMOTICS S‑1FT7/1FK7 permanent-magnet servomotors and SIMOTICA T‑1FW3 torque motors.
Vibration stress in accordance with DIN ISO 10816:
1 g at 20 Hz to 2 kHz
For all main motors of type SIMOTICS M‑1PH8, the following limits are valid for (immitted) vibration values introduced into the motor from outside:
Vibration frequency | Vibration values for | |
---|---|---|
< 6.3 Hz | Vibration displacement s | ≤ 0.16 mm (0.01 in) |
6.3 ... 250 Hz | Vibration velocity Vrms | ≤ 4.5 mm/s (0.18 in/s) |
> 250 Hz | Vibration acceleration a | ≤ 10 m/s2 (32.8 ft/s2) |
Vibration frequency | Vibration values for | |
---|---|---|
< 6.3 Hz | Vibration displacement s | ≤ 0.25 mm (0.01 in) |
6.3 ... 63 Hz | Vibration speed Vrms | ≤ 7.1 mm/s (0.28 in/s) |
> 63 Hz | Vibration acceleration a | ≤ 4.0 m/s2 (13.1 ft/s2) |
For all torque motors of type SIMOTICS T‑1FW3, the following limits are valid for (immitted) vibration values introduced into the motor from outside:
Vibration frequency | Vibration values for | |
---|---|---|
< 6.3 Hz | Vibration displacement s | ≤ 0.26 mm (0.01 in) |
6.3 ... 63 Hz | Vibration speed Vam | ≤ 7.1 mm/s (0.28 in/s) |
> 63 Hz | Vibration acceleration a | ≤ 4.0 m/s2 (13.1 ft/s2) |
Coolant temperature (ambient temperature) and installation altitude
Operation (unrestricted): -15 °C to +40 °C (5 °F to 104 °F)
The rated power (rated torque) is applicable to continuous duty (S1) in accordance with EN 60034-1 at rated frequency, a coolant temperature of 40 °C (104 °F) and an installation altitude of 1000 m (3281 ft) above sea level.
Apart from the SIMOTICS M‑1PH8 motors, all motors are in temperature class 155 (F) and utilized in accordance with temperature class 155 (F). The SIMOTICS M‑1PH8 motors are designed for temperature class 180 (H). For all other conditions, the factors given in the table below must be applied to determine the permissible output (torque).
The coolant temperature and installation altitude are rounded to 5 °C and 500 m (1640 ft) respectively.
Installation altitude above sea level | Coolant temperature | |||
---|---|---|---|---|
m (ft) | < 30 °C | 30 ... 40 °C | 45 °C | 50 °C |
1000 (3281) | 1.07 | 1.00 | 0.96 | 0.92 |
1500 (4922) | 1.04 | 0.97 | 0.93 | 0.89 |
2000 (6562) | 1.00 | 0.94 | 0.90 | 0.86 |
2500 (8203) | 0.96 | 0.90 | 0.86 | 0.83 |
3000 (9843) | 0.92 | 0.86 | 0.82 | 0.79 |
3500 (11484) | 0.88 | 0.82 | 0.79 | 0.75 |
4000 (13124) | 0.82 | 0.77 | 0.74 | 0.71 |
Duty types S1 and S6 in accordance with EN 60034‑1
Rated torque
The torque supplied on the shaft is indicated in Nm (lbf-ft) in the selection and ordering data.
Mrated = 9.55 × Prated × 1000/nrated
Prated Rated power in kW
nrated Rated speed in rpm
Mrated Rated torque in Nm
Mrated = Prated × (5250/nrated)
Prated Rated power in HP
nrated Rated speed in rpm
Mrated Rated torque in lbf-ft
DURIGNIT IR 2000 insulation system
The DURIGNIT IR 2000 insulation system consists of high-quality enamel wires and insulating sheeting in conjunction with a solvent-free resin impregnation.
The insulating material system ensures that these motors will have a high mechanical and electrical stability, high service value and a long service life.
The insulation system protects the winding to a large degree against aggressive gases, vapors, dust, oil and increased air humidity. It can withstand the usual vibration stressing.
Characteristic curves
Torque characteristic of a synchronous motor operating on a converter with field weakening (example)
nrated Rated speed
nmax Inv Maximum permissible electric speed limit
nmax mech Maximum permissible mechanical speed limit
M0 Static torque
Mrated Rated torque at rated speed
Mmax Inv Achievable maximum torque with recommended motor module
Mmax Maximum permissible torque
Motor protection
The KTY84‑130 temperature sensor is used to measure the motor temperature for converter-fed motor operation.
This sensor is a semi-conductor that changes its resistance depending on temperature in accordance with a defined curve.
Siemens converters determine the motor temperature using the resistance of the temperature sensor.
Their parameters can be set for specific alarm and shutdown temperatures.
The SIMOTICS L‑1FN3/‑1FN6 and SIMOTICS T‑1FW6 motors are additionally equipped with PTC sensors (PTC elements). In these motor series, evaluation is performed using the SME120/SME125 Sensor Module External or TM120 Terminal Module (see SINAMICS S120 drive system).
The KTY84‑130 temperature sensor is embedded in the winding overhang of the motor like a PTC thermistor.
The sensor is evaluated in the SINAMICS S120 drive system as a standard function.
If the motors are operated on converters that do not feature a KTY84 evaluation circuit, the temperature can be measured with the external 3RS1040 temperature monitoring relay. For a detailed description, please see Catalog IC 10 or Siemens Industry Mall:
http://www.siemens.com/industrymall
Paint finish
Motors without a paint finish have an impregnated resin coating. Motors with primer have corrosion protection.
All motors can be painted over with commercially available paints. Up to 2 additional paint coats are permissible.
Version | Suitability of paint finish for climate group | |
---|---|---|
Paint finish | Moderate (expanded) | Briefly up to 150 °C (302 °F) |
Continuously up to 120 °C (248 °F) | ||
Special paint finish | Worldwide (expanded) | Briefly up to 150 °C (302 °F) |
Continuously up to 120 °C (248 °F) | ||
Also for corrosive atmospheres up to 1 % acid and alkali concentration or permanent dampness in sheltered rooms |
Built-in encoder systems without DRIVE‑CLiQ interface
For motors without an integrated DRIVE‑CLiQ interface, the analog encoder signal in the drive system is converted to a digital signal. For these motors as well as external encoders, the encoder signals must be connected to SINAMICS S120 via Sensor Modules.
Built-in encoder systems with DRIVE‑CLiQ interface
For motors with an integrated DRIVE‑CLiQ interface, the analog encoder signal is internally converted to a digital signal. There is no further conversion of the encoder signal in the drive system. The motor-internal encoders are the same encoders that are used for motors without a DRIVE‑CLiQ interface. Motors with a DRIVE‑CLiQ interface simplify the commissioning and diagnostics, for example, due to automatic identification of the encoder system.
The different encoder types, incremental, absolute or resolver, are uniformly connected with one type of MOTION-CONNECT DRIVE‑CLiQ cable.
Short designations for the encoder systems
The first letters of the short designation define the encoder type. This is followed by the resolution in signals per revolution if S/R is specified (for encoders without DRIVE-CLiQ interface) or in bits if DQ is specified (for encoders with DRIVE-CLiQ interface).
Type | Resolution/interface | |
---|---|---|
AM | xxxxS/R | Encoder without DRIVE‑CLiQ interface |
AM | xxDQ | Encoder with DRIVE‑CLiQ interface |
AM | Multi-turn absolute encoder |
Overview of the motor encoder systems
Encoder without DRIVE‑CLiQ interface | Encoder with DRIVE‑CLiQ interface | Absolute position within a revolution (single-turn) | Absolute position over 4096 revolutions (multi-turn) | For use in Safety applications1) | ||||||||
---|---|---|---|---|---|---|---|---|---|---|---|---|
Identification letter in the | Identification letter in the motor order number | |||||||||||
Encoder | 1FT7 | 1FK7 | 1FW3 | 1PH8 | Encoder | 1FT7 | 1FK7 | 1FW3 | 1PH8 | |||
– | – | – | – | – | AM24DQI | C | C | – | – | Yes | Yes | Yes |
– | – | – | – | – | AM20DQI | – | R | – | – | Yes | Yes | Yes |
– | – | – | – | – | AS24DQI | B | B | – | – | Yes | No | Yes |
– | – | – | – | – | AS20DQI | – | Q | – | – | Yes | No | Yes |
AM2048S/R | M | E | E | E | AM22DQ | F | F | F | F | Yes | Yes | Yes |
AM512S/R | – | H | – | – | AM20DQ | – | L | – | – | Yes | Yes | Yes |
AM32S/R | – | G | – | – | AM16DQ | – | K | – | – | Yes | Yes | No |
AM16S/R | – | J | – | – | AM15DQ | – | V | – | – | Yes | Yes | No |
AS2048S/R | – | – | N | – | AS22DQ | – | – | P | – | Yes | No | No |
IC2048S/R | N | A | A | M | IC22DQ | D | D | D | D | No | No | Yes |
IN2048S/R | – | – | – | – | IN22DQ | – | – | – | Q | No | No | Yes |
HTL1024S/R | – | – | – | H | – | – | – | – | – | No | No | No |
HTL2048S/R | – | – | – | J | – | – | – | – | – | No | No | No |
Resolver | – | T | – | – | R14DQ | – | P | – | – | Yes | No | No |
Resolver | – | S | S | – | R15DQ | – | U | U | – | No | No | No |
Resolver | – | S | S | – | R15DQ | – | U | U | – | No | No | No |
1) Not for 1FW3 motors.
Not all encoders are available for every motor shaft height.
– Not possible
Multi-turn absolute encoder
Multi-turn absolute encoder
This encoder outputs an absolute angular position between 0° and 360° in the specified resolution. An internal measuring gearbox enables it to differentiate 4096 rotations. With a ball screw, for example, the absolute position of the slide can be determined over a long distance.
Single-turn absolute encoder
This encoder outputs an absolute angular position between 0° and 360° in the specified resolution. In contrast to the multi-turn absolute encoder, it has no measuring gearbox and can therefore only supply the position value within one revolution. It does not have a traversing range.
Absolute encoder without DRIVE‑CLiQ interface | |
---|---|
AM2048S/R | Absolute encoder 2048 S/R, 4096 revolutions |
AM512S/R | Absolute encoder 512 S/R, 4096 revolutions |
AM32S/R | Absolute encoder 32 S/R, 4096 revolutions |
AM16S/R | Absolute encoder 16 S/R, 4096 revolutions |
AS2048S/R | Absolute encoder single-turn 2048 S/R |
Absolute encoder with DRIVE‑CLiQ interface | |
AM24DQI | Absolute encoder 24 bit (resolution 16777216, internal 2048 S/R)+ 12 bit multi-turn (traversing range 4096 revolutions) |
AM20DQI | Absolute encoder 20 bit (resolution 1048576, internal 512 S/R)+ 12 bit multi-turn (traversing range 4096 revolutions) |
AM22DQ | Absolute encoder 22 bit (resolution 4194304, internal 2048 S/R)+ 12 bit multi-turn (traversing range 4096 revolutions) |
AM20DQ | Absolute encoder 20 bit (resolution 1048576, internal 512 S/R)+ 12 bit multi-turn (traversing range 4096 revolutions) |
AM16DQ | Absolute encoder 16 bit (resolution 65536, internal 32 S/R)+ 12 bit multi-turn (traversing range 4096 revolutions) |
AM15DQ | Absolute encoder 15 bit (resolution 32768, internal 16 S/R)+ 12 bit multi-turn (traversing range 4096 revolutions) |
AS24DQI | Single-turn absolute encoder 24 bit |
AS20DQI | Single-turn absolute encoder 20 bit |
AS22DQ | Single-turn absolute encoder 22 bit |
Technical specifications | |
Absolute encoder without DRIVE‑CLiQ interface | |
Supply voltage | 5 V |
Absolute position interface | |
Traversing range (multi-turn)1) | 4096 revolutions |
Incremental signals | |
Signals per revolution | 2048/512/32/16 |
Absolute encoder with DRIVE‑CLiQ interface | |
Supply voltage | 24 V |
Absolute position via DRIVE-‑LiQ | |
Resolution within one revolution | 224/222/220/216/215 bit |
Traversing range (multi-turn)1) | 4096 revolutions |
1) Not for absolute encoder, single-turn AS.
2) The single-turnabsolute encoder is used for the previous incremental encoders.
Incremental encoder
Incremental encoder IC/IN (sin/cos), commutation position for IC only
This encoder senses relative movements and does not supply absolute position information. In combination with evaluation logic, a zero point can be determined using the integrated reference mark, which can be used in turn to calculate the absolute position.
Incremental encoder IC/IN (sin/cos)
The encoder outputs sine and cosine signals. These can be interpolated using evaluation logic (usually 2048 points) and the direction of rotation can be determined.
In the version with DRIVE‑CLiQ interface, this evaluation logic is already integrated in the encoder.
Commutation position
The position of the rotor is required for commutation of a synchronous motor. Encoders with commutation position (also termed C and D track) detect the angular position of the rotor.
Incremental encoder IC/CN (sin/cos), commutation position only for IC
HTL incremental encoder
Incremental encoder without DRIVE-CLiQ interface | |
---|---|
IC2048S/R | Incremental encoder sin/cos 1 Vpp 2048 S/R |
IN2048S/R | Incremental encoder sin/cos 1 Vpp 2048 S/R |
Incremental encoder with DRIVE-CLiQ interface | |
IC22DQ | Incremental encoder 22 bit |
IN22DQ | Incremental encoder 22 bit |
Technical specifications | |
Angular error | |
| ± 40'''' |
| ± 120'''' |
Incremental encoder IC/IN (sin/cos) without DRIVE-CLiQ interface | |
Supply voltage | 5 V |
Incremental signals per revolution | |
| 2048 |
| 1 sin/cos |
| 1 |
Incremental encoder IC/IN (sin/cos) with DRIVE-CLiQ interface | |
Supply voltage | 24 V |
Incremental signals per revolution | |
| 222 bit |
| 11 bit |
| 1 |
HTL incremental encoder
The encoder outputs square wave signals. The direction of rotation can be evaluated by means of edge evaluation.
The resolution is four times the number of encoder pulses. This encoder type is preferred for long signal cables.
HTL incremental encoder
Incremental encoder without DRIVE‑CLiQ interface | |
---|---|
IC2048S/R | Incremental encoder sin/cos 1 Vpp 2048 S/R |
IN2048S/R | Incremental encoder sin/cos 1 Vpp 2048 S/R |
HTL2048S/R | Incremental encoder HTL 2048 S/R |
HTL1024S/R | Incremental encoder HTL 1024 S/R |
Incremental encoder without DRIVE‑CLiQ interface | |
IC22DQ | Incremental encoder 22 bit Запрос коммерческого предложения× Сообщение отправлено× В ближайшее время сообщение будет обработано. Письмо с номером обращения отправлено на Ваш почтовый ящик. Спасибо за то, что выбрали Первый ZIP! Что-то пошло не так...× К сожалению, наша система расценила Ваше сообщение как спам. Если это произошло по ошибке, пожалуйста, обратитесь к нам по электронной почте. Приносим извинения за возможные неудобства. |