1FK7 servomotors with series SP+ planetary gearbox Siemens
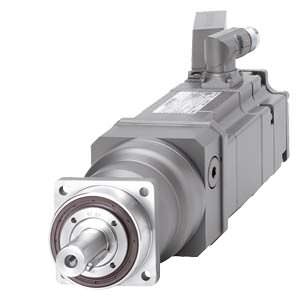
Обзор
SIMOTICS S-1FK7 motor with built-on SP+ planetary gearbox
SIMOTICS S-1FK7 motors can easily be combined with planetary gearboxes to form compact coaxial drive units. The gearboxes are flanged directly to the drive end of the motors.
When selecting the gearbox, ensure that its maximum permissible input speed is not exceeded by the maximum speed of the motor. In the case of high operating frequencies, allowance must be made for the factor f2 (see Configuration Manual, SIMOTICS S-1FK7 synchronous motors). The frictional losses of the gearbox must always be taken into account.
The gearboxes are only available in non-balanced design.
Интеграция
SIMOTICS S-1FK702 to 1FK710 motors can be supplied ex works (Siemens AG) complete with flange-mounted planetary gearbox.
The gearboxes assigned to the individual motors and gear ratios i available for these motor/gearbox combinations are listed in the subsequent selection table. When making a selection, account must be taken of the maximum permissible input speed of the gearbox (this is the same as the maximum motor speed).
The motor/gearbox combinations listed in the selection table are mainly intended for cycle operation S3-60 % (ON time ≤ 60 % and ≤ 20 min). Reduced maximum motor speeds and output torques apply for use in S1 continuous duty (ON time > 60 % or > 20 min). The gearbox temperature may not exceed 90 °C (194 °F).
Follow the instructions contained in the Configuration Manual for SIMOTICS S-1FK7 synchronous motors when assigning gearboxes to the motor.
Особенности
- High efficiency
Single-stage: > 97 %
Two-stage: > 94 % - Minimal torsional backlash
Single-stage: ≤ 4 arcmin
Two-stage: ≤6 arcmin - Power transmission from the central sun wheel via planet wheels
- No shaft deflections in the planet wheel set due to symmetrical force distribution
- Very low moment of inertia and hence short acceleration times of the motors
- Output shaft bearings dimensioned for high cantilever and axial loads with preloaded tapered-roller bearings
- The gearboxes are connected to the motor shaft via an integrated clamping hub. A plain motor shaft extension is necessary for this purpose. Shaft and flange accuracy tolerance N in accordance with DIN 42955 and vibration severity grade A in accordance with EN 60034-14 are sufficient. The motor flange is adapted by means of adapter plates.
- Output shaft of gearbox exactly coaxial with the motor
- The gearboxes are enclosed (seal between gearbox and motor) and filled with oil at the factory. They are lubricated and sealed for their service life.
The gearboxes are suitable for all mounting positions. - Degree of protection of gearbox: IP65
- Small dimensions
- Low weight
Технические данные
SIMOTICS S-1FK7 motors with SP+ planetary gearbox, single-stage | |||||||||
---|---|---|---|---|---|---|---|---|---|
Gearbox | Gear ratio | Motor speed | Output torque | Moments of inertia of gearbox (referred to the drive) | |||||
i | Continuous duty S11) | 1FK702 | 1FK703 | 1FK704 | 1FK706 | 1FK708 | 1FK710 | ||
nN1 | MN2 (T2N) | J1 | J1 | J1 | J1 | J1 | J1 | ||
rpm | Nm | kgcm2 (lbf-in2) | kgcm2 (lbf-in2) | kgcm2 (lbf-in2) | kgcm2 (lbf-in2) | kgcm2 (lbf-in2) | kgcm2 (lbf-in2) | ||
SP 060S‑MF1 | 4 | 3300 | 26 (19.2) | 0.15 (0.05) | 0.22 (0.08) | – | – | – | – |
5 | 3300 | 26 (19.2) | 0.12 (0.04) | 0.20 (0.07) | – | – | – | – | |
7 | 4000 | 26 (19.2) | 0.10 (0.034) | 0.18 (0.062) | – | – | – | – | |
10 | 4000 | 17 (12.5) | 0.09 (0.031) | 0.17 (0.058) | – | – | – | – | |
SP 075S‑MF1 | 4 | 2900 | 75 (55.3) | – | – | 0.78 (0.27) | – | – | – |
5 | 2900 | 75 (55.3) | – | – | 0.68 (0.23) | – | – | – | |
7 | 3100 | 75 (55.3) | – | – | 0.59 (0.20) | – | – | – | |
10 | 3100 | 52 (38.4) | – | – | 0.54 (0.19) | – | – | – | |
SP 100S‑MF1 | 4 | 2500 | 180 (133) | – | – | – | 3.04 (1.04) | – | – |
5 | 2500 | 175 (129) | – | – | – | 2.61 (0.89) | – | – | |
7 | 2800 | 170 (125) | – | – | – | 2.29 (0.78) | – | – | |
10 | 2800 | 120 (88.5) | – | – | – | 2.07 (0.71) | – | – | |
SP 140S‑MF1 | 4 | 2100 | 360 (266) | – | – | – | – | 11.0 (3.76) | – |
5 | 2100 | 360 (266) | – | – | – | – | 9.95 (3.40) | – | |
7 | 2600 | 360 (266) | – | – | – | – | 9.01 (3.08) | – | |
10 | 2600 | 220 (162) | – | – | – | – | 8.44 (2.88) | – | |
SP 180S‑MF1 | 4 | 1500 | 750 (553) | – | – | – | – | – | 33.9 (11.6) |
5 | 1500 | 750 (553) | – | – | – | – | – | 27.9 (9.53) | |
7 | 2300 | 750 (553) | – | – | – | – | – | 22.2 (7.59) | |
10 | 2300 | 750 (553) | – | – | – | – | – | 19.2 (6.56) | |
SP 210S‑MF1 | 10 | 2000 | 1000 (738) | – | – | – | – | – | 53.1 (18.1) |
1) The limit values in the table apply for S1 continuous duty (ON time > 60 % or > 20 min) for a maximum gearbox temperature of 90 °C (194 °F).
SIMOTICS S-1FK7 motors with SP+ planetary gearbox, two-stage | |||||||||
---|---|---|---|---|---|---|---|---|---|
Gearbox | Gear ratio | Motor speed | Output torque | Moments of inertia of gearbox (referred to the drive) | |||||
| i | Continuous duty S11) | 1FK702 | 1FK703 | 1FK704 | 1FK706 | 1FK708 | 1FK710 | |
nN1 | MN2 (T2N) | J1 | J1 | J1 | J1 | J1 | J1 | ||
rpm | Nm | kgcm2 (lbf-in2) | kgcm2 (lbf-in2) | kgcm2 (lbf-in2) | kgcm2 (lbf-in2) | kgcm2 (lbf-in2) | kgcm2 (lbf-in2) | ||
SP 060S‑MF2 | 16 | 4400 | 26 (19.2) | 0.08 (0.03) | 0.17 (0.058) | – | – | – | – |
20 | 4400 | 26 (19.2) | 0.07 (0.024) | 0.16 (0.055) | – | – | – | – | |
28 | 4400 | 26 (19.2) | 0.06 (0.021) | – | – | – | – | – | |
SP 075S‑MF2 | 16 | 3500 | 75 (55.3) | – | 0.23 (0.08) | 0.55 (0.19) | – | – | – |
20 | 3500 | 75 (55.3) | – | 0.20 (0.07) | 0.53 (0.18) | – | – | – | |
28 | 3500 | 75 (55.3) | – | 0.18 (0.062) | 0.5 (0.17) | – | – | – | |
40 | 3500 | 75 (55.3) | 0.10 (0.03) | 0.17 (0.058) | – | – | – | – | |
50 | 3800 | 75 (55.3) | 0.10 (0.03) | 0.16 (0.055) | – | – | – | – | |
SP 100S‑MF2 | 16 | 3100 | 180 (133) | – | – | 0.81 (0.28) | 2.18 (0.75) | – | – |
20 | 3100 | 180 (133) | – | – | 0.70 (0.24) | 2.07 (0.71) | – | – | |
28 | 3100 | 180 (133) | – | – | 0.60 (0.21) | 1.97 (0.67) | – | – | |
40 | 3100 | 180 (133) | – | 0.38 (0.13) | 0.55 (0.188) | – | – | – | |
50 | 3500 | 175 (129) | – | 0.38 (0.13) | 0.54 (0.185) | – | – | – | |
SP 140S‑MF2 | 16 | 2900 | 360 (266) | – | – | – | 3.19 (1.09) | 10.3 (3.52) | – |
20 | 2900 | 360 (266) | – | – | – | 2.71 (0.93) | 9.77 (3.34) | – | |
28 | 2900 | 360 (266) | – | – | – | 2.34 (0.80) | 9.41 (3.21) | – | |
40 | 2900 | 360 (266) | – | – | – | 2.1 (0.72) | 9.16 (3.13) | – | |
50 | 3200 | 360 (266) | – | – | 1.39 | 2.08 (0.71) | – | – | |
SP 180S‑MF2 | 16 | 2700 | 750 (553) | – | – | – | – | 12.4 (4.24) | 13.5 (4.61) |
20 | 2700 | 750 (553) | – | – | – | – | 10.9 (3.73) | 12.0 (4.10) | |
28 | 2700 | 750 (553) | – | – | – | – | 9.48 (3.24) | 10.6 (3.62) | |
40 | 2700 | 750 (553) | – | – | – | 5.51 (1.88) | 8.67 (2.96) | – | |
50 | 2900 | 750 (553) | – | – | – | 5.45 (1.86) | 8.61 (2.94) | – | |
SP 210S‑MF2 | 16 | 2500 | 1500 (1106) | – | – | – | – | – | 34.5 (11.8) |
20 | 2500 | 1500 (1106) | – | – | – | – | – | 31.5 (10.8) | |
28 | 2500 | 1500 (1106) | – | – | – | – | 30 (10.3) | 30 (10.3) | |
40 | 2500 | 1500 (1106) | – | – | – | – | 28.5 (9.74) | 28.5 (9.74) | |
50 | 2500 | 1500 (1106) | – | – | – | – | 28.3 (9.67) | 28.3 (9.67) | |
SP 240S‑MF2 | 28 | 2500 | 2500 (1844) | – | – | – | – | – | 30.5 (10.4) |
40 | 2500 | 2500 (1844) | – | – | – | – | – | 28.2 (9.64) | |
50 | 2500 | 2500 (1844) | – | – | – | – | – | 27.9 (9.53) |
1) The limit values in the table apply for S1 continuous duty (ON time > 60 % or > 20 min) for a maximum gearbox temperature of 90 °C (194 °F).