Manufacturing IT Siemens
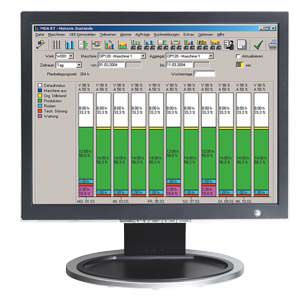
Обзор
Optimize production, servicing and maintenance withintegrated IT solutions!
Within the framework of SINUMERIK Manufacturing Excellence, Manufacturing IT offers you a holistic approach for optimizing your production-related processes involving machine tools with integrated IT solutions.
The building blocks are the IT products from SINUMERIK Integrate and extensive consultancy services for IT security and data security. We support you with our know-how during project implementation and operation of your solution.
Manufacturing IT supports your production and service processes with a wide range of consistently coordinated modular services that are based on SINUMERIK Integrate.
Production
Job management and preparation with SINUMERIK Integrate Analyze MyPerformance
The work in hand is flexibly controlled by a job management system based on Analyze MyPerformance (for example, with SIMATIC IT). Specifications and acknowledgements are exchanged between the ERP system (e.g. SAP) and production. Availability of the current information supports optimization of the manufacturing sequence and manufacturing resources. Further benefits are faster job throughput and reduced stock levels for materials.
Machine data acquisition and evaluation with SINUMERIK Integrate Analyze MyPerformance
Transparency is improved significantly by the use of machine data acquisition and evaluation (Analyze MyPerformance). This allows you to determine optimization potentials. Targeted analyses such as machine availability (OEE), cycle times, degree of utilization or alarm statistics prevent disturbances and result in longer machine runtimes.
Parts tracking and archiving with SINUMERIK Integrate Analyze MyPerformance
The functions for parts tracking and archiving based on Analyze MyPerformance and with SIMATIC IT support intelligent parts management as well as convenient parts tracking. This ensures that you are well-prepared for any warranty claims and product recalls. A reduction in costs accompanied by an increase in overall quality can also be expected.
Tool management with SINUMERIK Integrate Manage MyTools
Whether for individual machines, flexible transfer lines, or for the complete machine park – with our tool management (Manage MyTools), you have access to all tool data all the time. Through interfaces, the system ensures that the right data is at the right place at the right time. Tool statistics make your tool inventory transparent. You can detect potentials for rationalization with regard to tools much more easily and can achieve savings much more readily.
CNC program management and transfer with SINUMERIK Integrate Manage MyPrograms
CNC program management (Manage MyPrograms) offers you system-wide networking of your CNC machines and supports CNC program handling on transfer to and from the machine. It reduces costs in the CNC organization through secure and convenient CNC data archiving with versioning and administration functions.
Additional advantages:
- Optimized use of resources
- Shorter setup times and enhanced efficiency
- Reduced machine downtimes
- Automatic fault analyses
- Transparency in manufacturing down to the machine level
Maintenance
Preventive maintenance with SINUMERIK Integrate Manage MyMaintenance
The software module for maintenance management (Manage MyMaintenance) supports condition-oriented and/or preventive maintenance and optimizes servicing by early notification of the need for maintenance jobs such as cleaning, inspection and/or repair. This increases the machine runtime and reduces costs. The machine operators support the maintenance department by accepting responsibility for maintenance activities.
Data backup and archiving with SINUMERIK Integrate Access MyBackup
Data management supports backup, comparison and administration of control systems. This means: central data management with maximum fault tolerance and availability as well as efficient archiving of all machine data. When components are replaced, all the relevant data that is required for operation of these components is available again immediately. With Access MyBackup, we are providing an interface for accessing all the relevant backup data of a SINUMERIK 840D sl system. Manufacturers of data backup software can base their applications on this interface and are therefore authorized to implement SINUMERIK backup systems.
You will find Solution Partners at:
http://www.siemens.com/automation/partnerfinder
Condition Monitoring with SINUMERIK Integrate Analyze MyCondition (local or ASP1))
The investment decision depends increasingly on the analysis of costs over the complete lifecycle of a machine. Costs caused by machine downtime and unplanned maintenance dominate the calculation increasingly in accordance with the TCO principle (Total Cost of Ownership). The technical and organizational controlling of maintenance processes therefore becomes more and more important.
By means of standardized test procedures, Condition Monitoring supports machine operators, maintenance technicians and service engineers in determining the machine''s condition and monitoring the wear on the machine over time. Through continuous evaluation of the status of the machine tools, trends can be detected early and measures can be taken or planned on time. Individual machine components can also be monitored cyclically.
The integrated maintenance model is used to optimize downtimes resulting from maintenance work through a complete overview of preventive and/or condition-oriented maintenance. The optimum time for maintenance can then be selected and productivity can be further improved.
Additional advantages:
- Transparency and efficiency through optimization of the maintenance measures for your machine
- Reduction in inventory costs through forward scheduling of spare parts based on condition monitoring and evaluation of machine components
- Increased productivity through the implementation of condition-oriented maintenance measures
Service
Diagnostic Services with SINUMERIK Integrate Access MyMachine /Diagnosis (as ASP)
With Diagnostic Services, you can organize your service help desk and monitor the condition of your machines worldwide.
From tachograph data through to complex PLC logic, standard diagnostic cases can be preconfigured, stored as a template in the system and loaded onto your machines during commissioning.
On the control monitors you can trace the machine history in Diagnostic Services and thus find and analyze the causes of a fault quicker.
Your machines in the field are automatically synchronized with the servers on a regular basis. In the event of a fault, you can configure more specific diagnoses and transfer them to the machines. You are then able to further pinpoint faults dynamically.
If the results do not lead to a resolution of the problem, you caninvestigate the fault further by means of teleservice, rectify it online or consult other experts by means of a teleconference.
Worldwide and without need for time-consuming installation of software, as easy as web mail, as secure as online banking. And if fault rectification on-site is unavoidable, you will have planned your maintenance job optimally based on the machine status determined online and can deploy your resources effectively.
Additional advantages:
- Enhanced customer retention thanks to optimized service processes
- Remote operation and monitoring of the control systems using standard browsers helps to cut travel expenses
- Troubleshooting is speeded up by intelligent fault diagnostics supported by data and notification services
Internet service platform with SINUMERIK Integrate (ASP)
As an alternative to a local installation, Siemens offers the functions and services described above, including the entire
IT infrastructure, in the form of an ASP model.
In other words, an Internet-based infrastructure with high-performance servers, storage media and links to e-mail/text message systems.
The service platform supports you with:
- Availability of data and software functionality between different companies
- Assuring security for data access
- No need to change the security guidelines of participating companies
This type of environment is essential for quick and easy access to the knowledge of experts beyond corporate boundaries. A uniform view of the data of the machines and use of the same software enables faults to be rectified more quickly, resources to be implemented optimally, and costs to be reduced.
The infrastructure and services are compatible with today''s IT security regulations. Periodic security audits ensure that our systems are always up-to-date in terms of security technology.
Additional advantages:
- Low IT costs, and therefore cost-effective from the first machine onwards
- Accounting and investment security due to fixed prices
- High level of data security due to extremely fault-tolerant servers and multi-level access protection
1) ASP: Application Service Providing
Дальнейшая информация
Security information
Siemens provides products and solutions with industrial security functions that support the secure operation of plants, solutions, machines, equipment and/or networks. They are important components in a holistic industrial security concept. With this in mind, Siemens'' products and solutions undergo continuous development. Siemens recommends strongly that you regularly check for product updates.
For the secure operation of Siemens products and solutions, it is necessary to take suitable preventive action (e.g. cell protection concept) and integrate each component into a holistic, state-of-the-art industrial security concept. Third-party products that may be in use should also be considered.
For more information about industrial security, visit
http://www.siemens.com/industrialsecurity
To stay informed about product updates as they occur, sign up for a product-specific newsletter.
For more information, visit
http://support.automation.siemens.com