Condition Monitoring Siemens
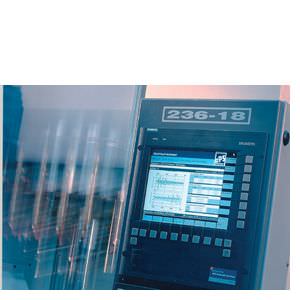
Обзор
Innovation potential for servicing and maintenance
Innovative, successful manufacturing enterprises focus their efforts on increasing the productivity and availability of machines and optimizing service and maintenance processes. Condition Monitoring makes an important contribution to the attainment of these goals.
Condition Monitoring
The investment decision depends increasingly on the analysis of costs over the complete lifecycle of a machine. Costs caused by machine downtime and unplanned maintenance dominate the calculation increasingly in accordance with the TCO principle (Total Cost of Ownership). The technical and organizational controlling of maintenance processes therefore becomes more and more important.
By means of standardized test procedures, Condition Monitoring supports machine operators, maintenance technicians and service engineers in determining the machine''s condition and monitoring the wear on the machine over time. Through continuous evaluation of the status of the machine tools, trends can be detected early and measures can be taken or planned on time. Individual machine components can also be monitored cyclically.
The integrated maintenance model is used to optimize downtimes resulting from maintenance work through a complete overview of preventative and/or status-oriented maintenance. The optimum time for maintenance can then be selected and productivity can be further improved.
By utilizing the full scope of Condition Monitoring functions, it is possible to optimize the costs incurred for production machine maintenance as well as the Total Cost of Ownership (TCO), and so benefit in the following ways:
- Increased plant availability
- Increased productivity
- Reduced overheads for inspection and maintenance
- Lower investment costs
- Freedom to concentrate on the core business
Monitoring of relevant components
In order to prevent undesirable machine downtimes and reduce unscheduled maintenance costs, the causes of prolonged outages and the drivers of lifecycle costs must also be included in the condition monitoring system.
On machine tools, this applies in equal measure to the linear axes and main spindles, the tool magazine, the chip conveyor and the automation system with pneumatic components and fluid technology.
Further advantages are gained by monitoring relevant components:
- Reduced risk of failure and consequential costs
- Lower spare parts costs through full utilization of wear margin
- Smaller spare part inventories particularly of expensive components
- Early notification when essential maintenance is required
- More effective planning of your resources
Condition monitoring methods
Condition Monitoring offers a variety of methods by which you can determine the exact condition of your machine tool.
Automated test procedures monitor the synchronism, friction, dynamic response and accuracy of linear axes. The variable monitor tracks freely selected PLC or NC variables accordingly without needing to make any changes to programs. All of this can be done with tools that are already integrated in the control system of your machine. The results of the measurements are stored and analyzed. They are displayed as individual measurements but also visualized in measurement series with trend display.
Furthermore, it is possible to integrate additional sensors into the overall process in order to incorporate more detailed information into the analysis of the machine''s condition.
The test procedures can be planned to suit requirements by means of the integrated maintenance planning function and performed if necessary with PLC support.
Workflow processes
Condition Monitoring automatically tracks the trend in significant performance characteristics and monitors them for violation of limit values. If a measurement delivers an inadmissible result, the application automatically informs the relevant partners by text message or e-mail. Where appropriate, it might even trigger a maintenance request directly for your machines.
You can of course integrate Condition Monitoring via interfaces into your maintenance system so that the maintenance request can also be issued there.
With Condition Monitoring you are laying the foundation for the creation of a condition-oriented maintenance system, thereby fulfilling one of the requirements for optimized production.
The platform
Siemens is offering Condition Monitoring as a standard clientserver application for operation in the customer''s own network, or via an Internet-based infrastructure with high-performance servers, storage media and links to e-mail/text message systems. The infrastructure and services are compatible with today''s IT security regulations. Periodic security audits ensure that our systems are always up-to-date in terms of security technology.
Дальнейшая информация
Security information
Siemens provides products and solutions with industrial security functions that support the secure operation of plants, solutions, machines, equipment and/or networks. They are important components in a holistic industrial security concept. With this in mind, Siemens'' products and solutions undergo continuous development. Siemens recommends strongly that you regularly check for product updates.
For the secure operation of Siemens products and solutions, it is necessary to take suitable preventive action (e.g. cell protection concept) and integrate each component into a holistic, state-of-the-art industrial security concept. Third-party products that may be in use should also be considered.
For more information about industrial security, visit
http://www.siemens.com/industrialsecurity
To stay informed about product updates as they occur, sign up for a product-specific newsletter.
For more information, visit
http://support.automation.siemens.com