Проволока и кабель Siemens
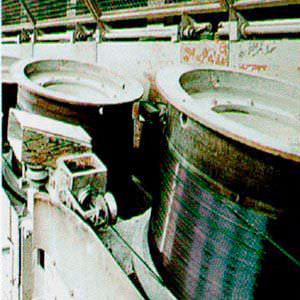
Обзор
Since it is easy to shape, wire has many applications ranging from electrical conductors and cables to wire ropes. Drawing processes allow the material structure and surface to be influenced as required. In this way it is also possible to extrude shaped parts (bar material) efficiently and cost-effectively. Cables are something we encounter every day, for instance as leads for electrical appliances or as conductors in high-voltage transmission systems. The properties of data or power cables can be predetermined during the manufacturing process. associated fields include the manufacture of flexible components or springs.
Wire-drawing
In wire-drawing machines the surface properties and structure of rolled or extruded wire are improved by reducing the cross-section (with a die). This is a commonly used and cost-effective process..
Straight-wire-drawing machines
The wire to be drawn is pulled off a reel or taken out of a barrel and fed to the first die. Dies cold-work the wire and reduce it to a specified diameter. The processed wire is then wound onto a reel.
The specifications for the wire product are obtained by the machine from a control system which generates the necessary data from order details. The SIMATIC S7 then calculates the setpoint values for the drives, the control, operator data monitoring and fault evaluation. The setpoint cascade is implemented with technology module T100 and peer-to-peer link in drives of the SIMOVERT MASTERDRIVES system. Tension control is taken care of in the same way. Communication at field level is performed by PROFIBUS DP. The drives consist of compact asynchronous motors of the 1PA6 range or standard asynchronous motors of the 1LA7 range.
Cabling machine
In an extrusion process, the wire received from the wire-drawing machine is provided with a layer of insulation. In a cabling machine this is laid up with other conductors to form a cable.
A laying-up curve α = f(s) is selected as a function of the length traveled, thus allowing the properties of the cable to be influenced as required. High production speeds call for cabling drives with fast dynamic responses. Here, it is necessary to handle reversal times as short as 30 ms.
In this case the laying-up curve is prescribed by the SIMATIC controller and passed on to the drives (Motion Control) via PROFIBUS. The cam disk technology software allows individual requirements to be taken into account in the form of the laying-up curve.
The motors employed are inertia-optimized, permanent-field synchronous motors of the 1FK6/1FT6 range.
Дальнейшая информация
I DT MC Technical Support
Phone: +49 180 50 50 222
Fax: +49 180 50 50 223