Flexible couplings N-EUPEX and N-EUPEX DS series Siemens
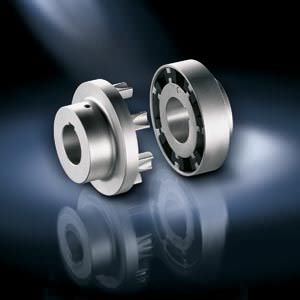
Область применения
The N-EUPEX coupling is available as a catalog standard in 23 sizes with a rated torque of between 19 Nm and 62000 Nm. The coupling is suitable for use at ambient temperatures of between –30 °C and +80 °C. By using alternative elastomer buffers, the permissible ambient temperature range can be extended to between –50 °C and +100 °C.
Frequently, the coupling is used to connect the motor to the gear unit input shaft. The coupling is suitable especially for drives with uniform to average dynamic loads. Examples of applications are pump drives, ventilator drives or crane running gear. Furthermore, N-EUPEX couplings can be used as add-on couplings, particularly on FLUDEX fluid couplings or ARPEX AKR safety couplings. In the case of drives with a diesel engine, N-EUPEX couplings are suitable for driven machines with a low mass moment of inertia.
In the case of diesel engine drives, the actual dynamic coupling load should be checked by measurement or torsional vibration calculations.
Coupling suitable for potentially explosive environments. Complies with Directive 94/9/EC for:
II 2 G T4 / T5 / T6 D120 °C
–30 °C ≤ Ta ≤ +80 °C / +50 °C / +40 °C
I M2
Обзор
N-EUPEX as overload-holding, fail-safe series
N-EUPEX DS as overload-shedding, non-fail-safe series
N-EUPEX and N-EUPEX DS claw couplings connect machines. They compensate for shaft misalignment, generating only low restorative forces.
The torque is conducted through elastomer flexibles, so the coupling has typically flexible rubber properties.
N-EUPEX couplings are overload-holding. By contrast, the N-EUPEX DS series is designed so that overload or advanced wear causes irreparable damage to the elastomer flexibles. The metal parts of N-EUPEX DS couplings can then rotate freely against one another without contact.
Elastomer flexible of the N-EUPEX series
The flexibles of the N-EUPEX coupling are subjected to compression. If the flexibles are irreparably damaged, the hub parts come into contact with metal. This “emergency operation capability” is required, e.g., in the case of fire pump drives.
Elastomer flexible of the N-EUPEX DS series
The flexibles of the N-EUPEX DS series are subjected to compression and bending forces. If the flexibles are irreparably damaged, the metal parts turn against one another without contact, and the power transmission is separated. Fitting new flexibles will make the coupling once more usable.
The capacity of the N-EUPEX DS series to shed overloads is especially in demand for highly sensitive machines.
Дизайн
N-EUPEX and N-EUPEX DS couplings consist of two hub parts mounted on the machine shafts. The coupling parts are connected positively by means of elastomer flexibles. On the twopart variant, the elastomer flexibles can be changed only if one of the coupled machines is moved. On the three-part variants, the bolted cam ring can be released and moved to enable the flexible to be changed without moving the coupled machines.
Materials
Cam parts, pocket parts, adapters and hubs
Grey cast iron EN-GJL-250
Flexible materials
- N-EUPEX Series
Material/description | Hardness | Identification | Ambient temperature |
---|---|---|---|
NBR standard type | 80 Shore A | Flexible black with blue stripe | –30 °C … +80 °C |
NBR soft | 65 Shore A | Flexible black with green stripe | –30 °C … +80 °C |
NBR hard | 90 Shore A | Flexible black with magenta stripe | –30 °C … +80 °C |
NBR normal low backlash | 80 Shore A | Flexible black with yellow stripe | –30 °C … +80 °C |
NBR soft low backlash | 65 Shore A | Flexible black with white stripe | –30 °C … +80 °C |
NR for low temperature | 80 Shore A | Flexible black with orange stripe | –50 °C … +50 °C |
HNBR high temperature | 80 Shore A | Flexible black with red stripe | –10 °C … +100 °C |
- N-EUPEX DS Series
Material/description | Hardness | Identification | Ambient temperature |
---|---|---|---|
NBR compound flexibles | 80/90 ShoreA | Flexible black | –30 °C … +80 °C |
NBR hard | 90 Shore A | Flexible black | –30 °C … +80 °C |
PU electrically insulating | 95 Shore A | Flexible blue | –30 °C … +50 °C |
PU elastomer flexibles in special design on request.
The technical data and the product codes do not include the flexible variants NBR low backlash, HNBR high temperature and
NR low temperature and the DS flexibles polyurethane electrically insulating.
Technical data, prices and product codes on request.
Brake disks
EN-GJS-400 spheroidal graphite cast iron or S355J2G3 steel
Brake drums
Grey cast iron EN-GJL-250
Low-temperature application
Shock loads in the drive caused by e.g. starting of drives with large masses to be accelerated (e.g. in fan drives) result in high component loads, particularly at low temperatures.
For such applications a particularly robust coupling series must be selected. Of the flexible couplings, the RUPEX pin-and-bush coupling is especially suited for this.
Types of N-EUPEX claw coupling
Type | Description |
---|---|
A | Fail-safe, 3-part |
B | Fail-safe, 2-part |
D | Fail-safe. 3-part, flange variant |
E | Fail-safe. 2-part, flange variant |
H | Fail-safe, with adapter |
O | Fail-safe, 2-part, with brake drum |
P | Fail-safe, 3-part, with brake drum |
EBD | Fail-safe, 2-part, with brake disk |
DBD | Fail-safe, 3-part, with brake disk |
DBDR | Fail-safe, 3-part, with brake disk, brake disk radially dismountable |
ADS | Non-fail-safe, 3-part |
BDS | Non-fail-safe, 2-part |
HDS | Non-fail-safe, with adapter |
Further application-related coupling types are available. Dimension sheets for and information on these are available on request.
Types of N-EUPEX claw coupling on request
Type | Description |
---|---|
AT | Fail-safe, 3-part, with Taper clamping bush |
BT | Fail-safe, 2-part, with Taper clamping bush |
G | Fail-safe, 2-part, with intermediate shaft |
F | Fail-safe, 3-part, with intermediate shaft |
K | Fail-safe, 3-part, with brake drum to customer''s requirement |
L | Fail-safe, 2-part, with brake drum to customer''s requirement |
M | Fail-safe, 2-part, with flange dimensions to SAE J620d |
Modular principle of N-EUPEX types
Types A and ADS
Types B and BDS
Type D
Type E
Type P
Type O
Type DBDR
Type DBD
Type EBD
Types H and HDS
Further application-related coupling types are available. Dimension sheets for and information on these are available on request.
Функции
The motor torque is transmitted to the hub at the drive end via the shaft-hub connection, which is mostly designed as a keyway connection. The torque is transmitted to the hub on the output side with the aid of elastomer flexibles. The hub on the output side further transmits the torque to the driven machine or a gear unit placed in between. Because of the primarily compressionloaded elastomer flexibles, the coupling has a progressive torsional stiffness.
In the case of the N-EUPEX DS coupling series, the elastomer flexible is subjected to bending and compression loads. In the event of overload or advanced wear, the coupling disconnects positively and the flexibles are irreparably damaged. The metal parts then rotate without touching one another. After new elastomer flexibles are fitted, the N-EUPEX DS coupling is once more operable.
N-EUPEX DS couplings are maintenance-free, even in potentially explosive environments, so long as the possible torque interruption does not lead to an unacceptable disruption of the production process.
Особенности
N-EUPEX couplings are designed on the modular principle and have a very simple construction. N-EUPEX types are made up of subassemblies to suit requirements. The couplings are assembled by simply fitting the coupling halves together. Wear is restricted to the elastomer flexibles, which must be replaced at the end of their service life.
Depending on type, the elastomer flexibles can be changed without moving the coupled machines.
The coupling parts are readily available from stock and are mostly finish-machined, i.e. with finished bore, keyway, set screw and balancing.
Optionally:
The wear indicator for N-EUPEX couplings enables the condition of the flexible to be easily assessed. The wear condition can also be ascertained with the aid of a stroboscope while the coupling is rotating. The production process can thus continue undisturbed.
If the stroboscope is to be used in a potentially explosive environment, you can enquire about the equipment for this at FLENDER.
The wear indicator must be attached to the outside diameter of the coupling after the coupling has been fitted.
Технические данные
Power ratings of the N-EUPEX series
Size | Rated torque for | Torsional stiffness at 50 % | Assembly | Permitted shaft alignment at n = 1500 rpm 1) | ||||||
---|---|---|---|---|---|---|---|---|---|---|
65 ShoreA | 80 ShoreA | 90 ShoreA | 65 ShoreA | 80 ShoreA | 90 ShoreA | Gap dimension 2) | Axial | Radial | Angle | |
TKN | TKN | TKN | CTdyn 50 % | CTdyn 50 % | CTdyn 50 % | ΔS | ΔKa | ΔKr | ΔKw | |
Nm | Nm | Nm | kNm/rad | kNm/rad | kNm/rad | mm | mm | mm | ° | |
58 | 11 | 19 | 19 | 0.21 | 0.50 | 0.93 | 1.0 | 0.2 | 0.2 | 0.15 |
68 | 21 | 34 | 34 | 0.39 | 0.90 | 1.80 | 1.0 | 0.2 | 0.2 | 0.15 |
80 | 37 | 60 | 60 | 1.05 | 2.40 | 4.50 | 1.0 | 0.2 | 0.2 | 0.12 |
95 | 63 | 100 | 100 | 1.64 | 4.00 | 7.40 | 1.0 | 0.2 | 0.2 | 0.12 |
110 | 100 | 160 | 160 | 2.49 | 6.00 | 11.40 | 1.0 | 0.2 | 0.2 | 0.10 |
125 | 150 | 240 | 240 | 3.70 | 9.00 | 17 | 1.0 | 0.25 | 0.25 | 0.10 |
140 | 230 | 360 | 360 | 5.60 | 13.2 | 25 | 1.0 | 0.25 | 0.25 | 0.10 |
160 | 350 | 560 | 560 | 11.2 | 26.7 | 51 | 2.0 | 0.3 | 0.3 | 0.10 |
180 | 550 | 880 | 880 | 19.2 | 46 | 88 | 2.0 | 0.3 | 0.3 | 0.10 |
200 | 850 | 1340 | 1340 | 31.6 | 75 | 139 | 2.0 | 0.3 | 0.3 | 0.09 |
225 | 1260 | 2000 | 2000 | 48 | 115 | 212 | 2.0 | 0.35 | 0.35 | 0.09 |
250 | 1760 | 2800 | 2800 | 68 | 162 | 302 | 2.5 | 0.35 | 0.35 | 0.08 |
280 | 2460 | 3900 | 3900 | 95 | 226 | 420 | 2.5 | 0.4 | 0.4 | 0.08 |
315 | 3500 | 5500 | 5500 | 171 | 370 | 730 | 2.5 | 0.4 | 0.4 | 0.08 |
350 | 4850 | 7700 | 7700 | 235 | 520 | 950 | 2.5 | 0.5 | 0.5 | 0.08 |
400 | 6500 | 10300 | 10300 | 316 | 750 | 1420 | 2.5 | 0.5 | 0.5 | 0.08 |
440 | 8500 | 13500 | 13500 | 390 | 930 | 1920 | 2.5 | 0.6 | 0.6 | 0.08 |
480 | 10500 | 16600 | 16600 | 510 | 1200 | 2300 | 2.5 | 0.6 | 0.6 | 0.07 |
520 | 13300 | 21200 | 21200 | 600 | 1410 | 2710 | 2.5 | 0.65 | 0.65 | 0.07 |
560 | 18300 | 29000 | 29000 | 1000 | 2340 | 4400 | 3.0 | 0.65 | 0.65 | 0.07 |
610 | 24000 | 38000 | 38000 | 1300 | 3030 | 5700 | 3.0 | 0.75 | 0.75 | 0.07 |
660 | 30900 | 49000 | 49000 | 1640 | 3800 | 7100 | 3.0 | 0.8 | 0.8 | 0.07 |
710 | 39000 | 62000 | 62000 | 2140 | 4900 | 9100 | 3.0 | 0.9 | 0.9 | 0.07 |
1) The maximum speed of the respective type must be noted. For further information on permissible shaft misalignment, please see the operating instructions.
2) Does not apply to type H.
For maximum coupling torque: TKmax = 3.0 · TKN
For coupling overload torque: TKOL = 3.5 · TKN
For coupling fatique torque: TKW = 0.15 · TKN, where TN > TW must be adhered to.
Torsional stiffness and damping
The values stated in the above table apply to a capacity utilization of 50 %, an excitation amplitude of 10 % TKN with the frequency 10 Hz and an ambient temperature of 20 °C. Dynamic torsional stiffness is dependent on load and increases in proportion to capacity utilization. The following table shows the correction factors for different nominal loads.
CTdyn = CTdyn 50 % · FKC
Capacity utilization TN/TKN | |||||||
---|---|---|---|---|---|---|---|
20 % | 40 % | 50 % | 60 % | 70 % | 80 % | 100 % | |
Correction factor FKC | 0.54 | 0.84 | 1.00 | 1.18 | 1.36 | 1.55 | 1.97 |
The damping coefficient is Ψ = 1.4
Furthermore, torsional stiffness and damping depend on the ambient temperature and the frequency and amplitude of the torsional vibration excitation. More precise torsional stiffness and damping parameters on request
Permitted shaft misalignment
The permitted shaft misalignment depends on the operating speed. As the speed increases, lower shaft misalignment values are permitted. The following table shows the correction factors for different speeds.
The maximum speed for the respective coupling size must be observed!
ΔKperm = ΔK1500 · FKV
Speed in rpm | ||||
---|---|---|---|---|
500 | 1000 | 1500 | 3000 | |
Correction factor FKV | 1.7 | 1.2 | 1.0 | 0.70 |
The axial misalignment may occur dynamically at frequencies up to 10 Hz. For fitting a maximum gap dimension of Smax = S + ΔS and a minimum gap dimension of Smin = S – ΔS is permitted. Shaft misalignments ΔKa, ΔKr and ΔKw may occur simultaneously.
Power ratings of the N-EUPEX DS series
Size | Rated torque | Torsional stiffness at 50 % | Assembly | Permitted shaft misalignment at | ||
---|---|---|---|---|---|---|
Gap dimension 1) | Axial | Radial | Angel | |||
TKN | CTdyn | ΔS | ΔKa | ΔKr | ΔKw | |
Nm | kNm/rad | mm | mm | mm | ° | |
66 | 19 | 0.73 | 1.0 | 0.2 | 0.2 | 0.15 |
76 | 34 | 1.36 | 1.0 | 0.2 | 0.2 | 0.15 |
88 | 60 | 2.62 | 1.0 | 0.2 | 0.2 | 0.12 |
103 | 100 | 4.00 | 1.0 | 0.2 | 0.2 | 0.12 |
118 | 160 | 6.30 | 1.0 | 0.2 | 0.2 | 0.10 |
135 | 240 | 10.5 | 1.0 | 0.25 | 0.25 | 0.10 |
152 | 360 | 13.6 | 1.0 | 0.25 | 0.25 | 0.10 |
172 | 560 | 27.2 | 2.0 | 0.3 | 0.3 | 0.10 |
194 | 880 | 47.0 | 2.0 | 0.3 | 0.3 | 0.10 |
218 | 1340 | 70.0 | 2.0 | 0.3 | 0.3 | 0.09 |
245 | 2000 | 106 | 2.0 | 0.35 | 0.35 | 0.09 |
272 | 2800 | 149 | 2.5 | 0.35 | 0.35 | 0.08 |
305 | 3900 | 214 | 2.5 | 0.4 | 0.4 | 0.08 |
340 | 5500 | 350 | 2.5 | 0.4 | 0.4 | 0.08 |
380 | 7700 | 480 | 2.5 | 0.5 | 0.5 | 0.08 |
430 | 10300 | 730 | 2.5 | 0.5 | 0.5 | 0.08 |
472 | 13500 | 990 | 2.5 | 0.6 | 0.6 | 0.08 |
514 | 16600 | 1270 | 2.5 | 0.6 | 0.6 | 0.07 |
556 | 21200 | 1540 | 2.5 | 0.65 | 0.65 | 0.07 |
1) Does not apply to type HDS.
Flexibles of sizes 66 to 272 are of the compound type with a hard core and soft thrust pieces.
Sizes 305 to 556 are of 90 ShoreA NBR material.
For maximum coupling torque: TKmax = 2.0 · TKN
For coupling overload torque: TKOL = 3.0 · TKN
For coupling fatigue torque: TKW = 0.15 · TKN
Torsional stiffness and damping
The values stated in the above table apply to a capacity utilization of 50 %, an excitation amplitude of 10 % TKN with the frequency 10 Hz and an ambient temperature of 20 °C. Dynamic torsional stiffness is dependent on the load and increases in proportion to capacity utilization. The following table shows the correction factors for different rated loads.
CTdyn = CTdyn 50 % · FKC
Capacity utilization TN / TKN | |||||||
---|---|---|---|---|---|---|---|
20 % | 40 % | 50 % | 60 % | 70 % | 80 % | 100 % | |
Correction factor FKC | 0.7 | 0.9 | 1 | 1.1 | 1.2 | 1.3 | 1.5 |
The damping coefficient isΨ = 1,4
Torsional stiffness and damping is further dependent on the ambient temperature and the frequency and amplitude of the torsional vibration excitation. More precise torsional stiffness and damping parameters on request.
Permitted shaft misalignment
The permitted shaft misalignment depends on the operating speed. As the speed increases, lower shaft misalignment values are permitted. The following table shows the correction factors for different speeds.
The maximum speed for the respective coupling size must be noted!
ΔKperm = ΔK1500 · FKV
Speed in rpm | ||||
---|---|---|---|---|
500 | 1000 | 1500 | 3000 | |
Correction factor FKV | 1.6 | 1.20 | 1.0 | 0.70 |
The axial misalignment must occur dynamically at frequencies up to 10 Hz. For fitting a maximum gap dimension of Smax = S + ΔS and a minimum gap dimension of Smin = S – ΔS are permitted.
Shaft misalignment ΔKa, ΔKr and ΔKw may occur simultaneously.
Assignment of N-EUPEX sizes to IEC standard motors
The assignment applies to an application factor of 1.25.
Outputs PM of IEC motors and assigned N-EUPEX couplings
Three-phase motor | Output at ≈ 3000 rpm | N-EUPEX coupling | Output at ≈ 1500 rpm | N-EUPEX coupling | Output at ≈ 1000 rpm | N-EUPEX coupling | Output at ≈ 750 rpm | N-EUPEX coupling | DE shaft end D x E to IEC | |
---|---|---|---|---|---|---|---|---|---|---|
Size | PM | Size | PM | Size | PM | Size | PM | Size | D | E |
kW | kW | kW | kW | mm | mm | |||||
56 | 0.09 | 58 | 0.06 | 58 | 9 | 20 | ||||
0.12 | 58 | 0.09 | 58 | |||||||
63 | 0.18 | 58 | 0.12 | 58 | 11 | 23 | ||||
0.25 | 58 | 0.18 | 58 | |||||||
71 | 0.37 | 58 | 0.25 |
Запрос коммерческого предложения× Сообщение отправлено× В ближайшее время сообщение будет обработано. Письмо с номером обращения отправлено на Ваш почтовый ящик. Спасибо за то, что выбрали Первый ZIP! Что-то пошло не так...× К сожалению, наша система расценила Ваше сообщение как спам. Если это произошло по ошибке, пожалуйста, обратитесь к нам по электронной почте. Приносим извинения за возможные неудобства. |