Flexible couplings BIPEX series Siemens
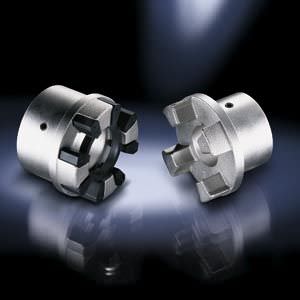
Область применения
The BIPEX coupling is available as a catalog standard in 13 sizes with rated torque of between 13.5 Nm and 3700 Nm.
The coupling is suitable for ambient temperatures of between –30 °C and +80 °C.
BIPEX couplings are particularly suited for electric motor drives which have a uniform torque load and are well aligned. BIPEX couplings are frequently fitted and used in motor bell housings.
Обзор
BIPEX couplings are torsionally flexible with low torsional backlash. They are outstanding for their particularly compact construction. BIPEX couplings link machine shafts.
BIPEX couplings are specially suited for electric motor drives which are well aligned and have uniform torque loads.
Дизайн
BIPEX couplings of types BWN, BWT and BNT each comprise two hub parts connected by a cam ring of elastomer material.
Type BWN
Type BWT
Type BNT
The couplings are inserted during fitting. The hubs are connected to the respective shafts via Taper clamping bushes or finished bores with parallel keyway connection.
BIPEX couplings are positive-locking and torsionally flexible thanks to the polyurethane cam ring. Shaft misalignment will result in deformation of the cam ring.
Coupling materials:
Hubs: EN-GJL-250
Cam ring: PU 92 ShoreA –30 °C bis +80 °C
Types of BIPEX coupling
Type | Description |
---|---|
BWN | Coupling as a shaft-to-shaft connection with drilled and grooved hubs |
BWT | Coupling as a shaft-shaft connection with Taper clamping bushes |
BNT | Coupling as a shaft-shaft connection with drilled and grooved hubs and a Taper clamping bush |
The coupling comprises the following:
- Cam ring
- 2 hub parts with identical cams. The hub parts are designed with a bore and keyway to DIN 6885 or with a taper bore for mounting a Taper clamping bush.
Fitting the clamping bush connects the hub firmly to the machine shaft. In the case of part 4 the Taper clamping bush is inserted from the machine housing side. If there is insufficient space, the Taper clamping bush cannot be fitted from this side. Besides space for fitting the Taper clamping bush, space for the fitting tool (offset screwdriver) must be taken into consideration. In the case of part 3 the Taper clamping bush is inserted from the shaft end face side. The hub must be fitted before the machines to be connected are pushed together.
Особенности
BIPEX couplings are suitable for mounting horizontally, vertically or at any desired angle. The coupling parts can be arranged as required on the shaft extensions to be connected.
The cam ring is mounted with low backlash and achieves progressive torsional stiffness, i.e. torsional stiffness increases in proportion to capacity utilization.
The BIPEX coupling is fail-safe, i.e. if the cam ring is worn, the cast cams of the coupling hub provide for emergency operation.
Технические данные
Power ratings
Size | Rated torque | Maximum torque | Overload torque | Fatigue torque | Maximum speed | Torsional stiffness at 50 % capacity utilization | Assembly | Permissible shaft misalignment at speed n = 1500 rpm 1) | ||
---|---|---|---|---|---|---|---|---|---|---|
TKN | TKmax | TK0L | TKW | nmax | CTdyn 50 % | ΔS | ΔKa | ΔKr | ΔKw | |
Nm | Nm | Nm | rpm | Nm/rad | mm | mm | mm | Degrees | ||
43 | 13.5 | 40.5 | 54 | 2.7 | 5000 | 1160 | 0.5 | 0.25 | 0.08 | 0.1 |
53 | 24 | 72 | 96 | 4.8 | 5000 | 2100 | 0.5 | 0.25 | 0.09 | 0.1 |
62 | 42 | 126 | 168 | 8.4 | 5000 | 3500 | 0.5 | 0.25 | 0.11 | 0.1 |
72 | 75 | 225 | 300 | 15 | 5000 | 6100 | 0.5 | 0.25 | 0.12 | 0.1 |
84 | 130 | 390 | 520 | 26 | 5000 | 9600 | 0.5 | 0.25 | 0.14 | 0.1 |
97 | 220 | 660 | 880 | 44 | 5000 | 15800 | 1.0 | 0.5 | 0.16 | 0.1 |
112 | 360 | 1080 | 1440 | 72 | 5000 | 23100 | 1.0 | 0.5 | 0.19 | 0.1 |
127 | 550 | 1650 | 2200 | 110 | 5000 | 37000 | 1.0 | 0.5 | 0.21 | 0.1 |
142 | 800 | 2400 | 3200 | 160 | 4900 | 57000 | 1.0 | 0.5 | 0.24 | 0.1 |
162 | 1250 | 3750 | 5000 | 250 | 4200 | 85000 | 1.0 | 0.5 | 0.27 | 0.1 |
182 | 1750 | 5250 | 7000 | 350 | 3800 | 127000 | 1.0 | 0.5 | 0.30 | 0.1 |
202 | 2650 | 7950 | 10600 | 530 | 3400 | 171000 | 1.0 | 0.5 | 0.34 | 0.1 |
227 | 3700 | 11100 | 14800 | 740 | 3000 | 285000 | 2.0 | 1.0 | 0.38 | 0.1 |
1) The maximum speed of the respective type must be noted. For further information on permissible shaft misalignment, please see the operating instructions.
Torsional stiffness and damping
The values stated in the above table apply to a capacity utilization of 50 %, an excitation amplitude of 10 % TKN with the frequency 10 Hz and an ambient temperature of 20 °C. Dynamic torsional stiffness is dependent on load and increases in proportion to capacity utilization. The following table shows the correction factors for different nominal loads.
CTdyn = CTdyn 50 % · FKC
Capacity utilization TN/TKN | |||||||
---|---|---|---|---|---|---|---|
20 % | 40 % | 50 % | 60 % | 70 % | 80 % | 100 % | |
Correction factor FKC | 0.7 | 0.9 | 1.0 | 1.1 | 1.25 | 1.4 | 1.7 |
The damping coefficient is Ψ = 1.4
Furthermore, torsional stiffness and damping depend on the ambient temperature and the frequency and amplitude of the torsional vibration excitation. More precise torsional stiffness and damping parameters on request.
Permitted shaft misalignment
The permitted shaft misalignment depends on the operating speed. As the speed increases, lower shaft misalignment values are permitted. The following table shows the correction factors for different speeds.
The maximum speed for the respective coupling size and type must be observed!
ΔKperm = ΔK1500 · FKV
Speed in rpm | ||||
---|---|---|---|---|
500 | 1000 | 1500 | 3000 | |
Correction factor FKV | 1.20 | 1.10 | 1.0 | 0.70 |
The axial misalignment may occur dynamically at frequencies up to 10 Hz. For fitting, a maximum gap dimension of Smax = S + ΔS and a minimum gap dimension of Smin = S – ΔS are permitted.
Shaft misalignments ΔKa, ΔKr and ΔKw may occur simultaneously.