SIPLUS IM 153-1/153-2 Siemens
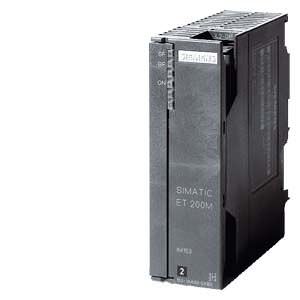
Область применения
The IM 153-1 / IM 153-2 HF interface modules are required to connect the modular I/O device ET 200M to the PROFIBUS DP fieldbus.
These heads can be used in many different applications.
Special functions and modules for PCS7
The IM 153-2 is provided with special functions, such as clock synchronization, time stamping or I&M functions. In addition, special modules are available that take into account the increased diagnosis requirements in process engineering. For example, digital input modules allow for the connection of NAMUR sensors, have wire-break detectors at "0" and "1" signals and functions such as flatter monitoring or pulse stretching. In order to obtain a reasonable channel price, 8-channel HART modules may be used.
High availability systems
High availability systems are used in all cases where no system outage is permitted or the system restart after an unscheduled outage is tied to very high costs. Typical applications include, for example, power generation, power distribution, tunnel systems, baggage conveyor systems at airports, oil platforms, oil refineries, the manufacture of special glass, the semiconductor industry, etc.
In conjunction with the high-availability S7-400H (redundant CPUs), the ET 200M can be connected one-way (normal availability) or switched (increased availability).
Furthermore, the IM 153-2 can also be used in applications with S5-155H, with S7-300 / S7-400 with software redundancy as well as with the normal redundancy standardized in the PNO.
Area subject to explosion hazard
Various digital and analog modules exist as intrinsically safe versions for the Ex area. This means the modules themselves are installed in Zone 2 cost effectively; however, they can reach the sensors and actuators to be connected up to Zone 1. They are used, for example, in the chemical and pharmaceutical industry, on oil rigs or also in classic manufacturing plants, such as the printing industry or in paint shops in the automobile industry. They allow channel-wise, isolated processing of signals from the Ex zone 1. For use in the non-Ex area, the isolation from channel to channel for these modules is 250 V AC. In addition, there are still HART-capable analog modules.
Fail-safe systems
Fail-safe controllers switch to a safe state when a fault occurs and thus protect operators, machines, and the environment, e.g. for presses, robots or passenger transportation. For the connection of fail-safe signals to S7-300F or S7-400F/FH, several signal modules are available that provide SIL 2 or SIL 3 depending on the type of connection.
For the application of safety-related I/O modules, the IM 153-2 HF interface module must be used.
Highly dynamic production processes
Distributed solutions for the control of high-speed machines for production and machining processes with high accuracy are becoming increasingly important, e.g. for drive controls. For this reason, the time from the acquisition of a signal by the distributed I/O through to the appropriate response of the actuator must be kept as short and as accurately reproducible as possible. Synchronous coupling of a SIMATIC automation solution to the equidistant PROFIBUS is called "isochronous mode" and is supported by various signal modules of the ET 200M.
Обзор
Note:
SIPLUS extreme products are based on SIMATIC standard products. The contents listed here were taken from the respective standard products. SIPLUS extreme specific information was added.
For technical documentation on SIPLUS, see:
http://www.siemens.de/siplus-extreme
Дизайн
- The IM 153-1/153-2 interface module serves as the head module (IM; Interface Module) of the ET 200M. Up to 8 or 12 I/O modules from the module product range of the S7-300 automation system can be connected to the interface module.
- The interface module and the necessary I/O modules are assembled on a profile rail for the S7-300. During assembly, the I/O modules are connected to one another using bus connectors and using the IM 153 interface modules.
- For redundant operation, two IM 153-2 are mounted onto the BM IM/IM bus module. Special profile rails are available to accommodate the bus modules.
- When equipping the IM153 with S7-300 modules, slot rules do not have to be taken into account.
Функции
Features | IM 153-1 (Standard) 6ES7 153-1AA03-0XB0 | IM153-2 High Feature 6ES7 153-2BA02-0XB0 6ES7 153-2BA82-0XB0 |
---|---|---|
Mechanical data |
|
|
Dimensions (W x H x D) | 40 x 125 x 117 mm | 40 x 125 x 117 mm |
PROFIBUS-DP interface |
|
|
Physics | RS485 (copper) | RS485 (copper) |
PROFIBUS addresses | 1 ... 125 (via DIP switch) | 1 ... 125 (via DIP switch) |
Baud rates | 9.6 kBd ... 12 MBd | 9.6 kBd ... 12 MBd |
Autom. baud rate search | Yes | yes |
SYNC / FREEZE capable | yes | yes |
Specifications |
|
|
Number of insertable modules | 8 | 12 |
Number of E / A bytes (user data specifications) | 128 / 128 | 244 / 244 |
Parameterized data | 244 | 244 |
Diagnosis data | 64 | 96 |
Module range |
|
|
Digital IO | Unrestricted | unrestricted |
Analog IO | unrestricted | unrestricted |
FM | Restricted | unrestricted |
CP | Restricted | Restricted |
F modules | No | unrestricted |
HART modules | no | unrestricted |
IQ Sense | no | Unrestricted |
Functionality |
|
|
FW update | no | Yes (PROFIBUS) |
I&M data1) | no | yes |
Clock synchronization | no | yes |
Module change during operation | Yes, with active backplane bus | yes, with active backplane bus |
Clock synchronization | no | Yes |
| yes | |
Accuracy class | no | 10 ms / 1 ms |
Number of signals/station | no | 128 |
Redundancy | ||
| no | Yes |
| no | Yes |
| no | Yes |
| no | yes |
Direct data exchange with F modules | no | yes |
Forwards parameterized data from PG / PC ("C2 channel") | no | yes |
Extended range of environmental conditions (outdoors) | no | Yes (only -2BA82-) |
Configuration change in RUN 4) | ||
| no | Yes |
| no | Yes |
1) I&M data: Set-up and data access in accordance with the provisions in the PROFIBUS Guideline – Order No. 3.502, Version 1.1 of May 2003
2) Changes to digital inputs are tagged with a time stamp locally (in the IM 153 of the ET 200M) and transferred to the CPU by means of a process interrupt. If you want to achieve high-precision time stamping of 1ms with the IM153-2BAx2, a max. of 8 modules per IM can remain plugged in.
3) Normal redundancy according to PNO: "Flying Redundancy" according to standard Slave Redundancy Specification V1.2, Nov. 2004 of PROFIBUS International; Order No 2.212.
4) Changing the configuration in RUN means that changes to the hardware configuration, e.g. reparameterization or the addition of modules, can be performed during normal operation without any adverse effects.
How they work
The IM 153 interface module completely handles communication of the modular ET 200M I/O device with the host master device on the PROFIBUS DP.
The inputs and outputs are assigned to the respective master during configuration.
The IM 153-2 interface module allows the design of redundant PROFIBUS DP systems. On failure of the active branch, the passive IM 153-2 takes over the corresponding functions without interruption.
Parameterization
STEP 7
Configuration is carried out using HW Config by selecting the respective headend from the corresponding HW catalog. The configuration with modules is also carried out from the corresponding HW catalog.
Third-party tools
Interfacing to third-party masters and configuration using third-party tools is carried out using the GSD file.
Технические данные
Order number | 6AG1153-1AA03-2XB0 | 6AG1153-2BA02-2XY0 | 6AG1153-2BA02-7XB0 | |
---|---|---|---|---|
SIPLUS IM153-1 | SIPLUS ET200M IM153-2 EN50155 | SIPLUS_IM153-2 | ||
General information |
|
|
| |
Vendor identification (VendorID) | 801Dh | 801Eh | 801Eh | |
Supply voltage |
|
|
| |
Rated value (DC) | ||||
| Yes | Yes | Yes | |
permissible range (ripple included), lower limit (DC) | 20.4 V | 20.4 V | 20.4 V | |
permissible range (ripple included), upper limit (DC) | 28.8 V | 28.8 V | 28.8 V | |
external protection for power supply lines (recommendation) | not necessary | 2,5 A | 2,5 A | |
Mains buffering |
|
|
| |
| 5 ms | 5 ms | 5 ms | |
Input current |
|
|
| |
Current consumption, max. | 350 mA; at 24 V DC | 600 mA | 600 mA | |
Inrush current, typ. | 2.5 A | 3 A | 3 A | |
I²t | 0.1 A²·s | 0.1 A²·s | 0.1 A²·s | |
Output voltage |
|
|
| |
Rated value (DC) | 5 V | 5 V | 5 V | |
Output current |
|
|
| |
for backplane bus (5 V DC), max. | 1 A | 1.5 A | 1.5 A | |
Power loss |
|
|
| |
Power loss, typ. | 3 W | 5.5 W | 5.5 W | |
Address area |
|
|
| |
Addressing volume |
|
|
| |
| 128 byte | 244 byte | 244 byte | |
| 128 byte | 244 byte | 244 byte | |
Hardware configuration |
|
|
| |
Number of modules per DP slave interface, max. | 8 | 12 | 12 | |
Time stamping |
|
|
| |
Accuracy | 1 ms; 1ms at up to 8 modules; 10ms at up to 12 modules | 1 ms; 1ms at up to 8 modules; 10ms at up to 12 modules | ||
Number of message buffers | 15 | 15 | ||
Messages per message buffer | 20 | 20 | ||
Number of stampable digital inputs, max. | 128; Max. 128 signals/station; max. 32 signals/slot | 128; Max. 128 signals/station; max. 32 signals/slot | ||
Time format | RFC 1119 | RFC 1119 | ||
Time resolution | 0.466 ns | 0.466 ns | ||
Time interval for transmitting the message buffer if a message is present | 1 000 ms | 1 000 ms | ||
Time stamp on signal change | rising / falling edge as signal entering or exiting | rising / falling edge as signal entering or exiting | ||
Interfaces |
|
|
| |
Interface physics, RS 485 | Yes | Yes | Yes | |
Interface physics, FOC | No | No | No | |
PROFIBUS DP |
|
|
| |
| 1 to 125 permitted | 1 to 125 permitted | 1 to 125 permitted | |
| Yes | Yes | Yes | |
| 90 mA | 70 mA | 70 mA | |
| 12 Mbit/s | 12 Mbit/s | 12 Mbit/s | |
| RS 485 | RS 485 | RS 485 | |
| Yes | Yes | Yes | |
| Yes | Yes | Yes | |
| Yes; Sender | Yes; Sender | Yes; Sender | |
| 9-pin sub D socket | 9-pin sub D | 9-pin sub D | |
1. Interface |
|
|
| |
DP slave |
|
|
| |
| (for DPV1) SIEM801D.GSD; SI01801D.GSG | SI04801.GSG | SI04801.GSG | |
| Yes | Yes | Yes | |
Protocols |
|
|
| |
Bus protocol/transmission protocol | PROFIBUS DP to EN 50170 | PROFIBUS DP to EN 50170 | PROFIBUS DP to EN 50170 | |
Isolation |
|
|
| |
Isolation tested with | Isolation voltage 500 V | 500V AC for 1 minute | Isolation voltage 500 V | |
Degree and class of protection |
|
|
| |
Degree of protection acc. to EN 60529 | ||||
| Yes | Yes | Yes | |
Standards, approvals, certificates |
|
|
| |
CE mark | Yes | Yes | Yes | |
UL approval | Yes; File E239877 | Yes; File E239877 | Yes; File E239877 | |
FM approval | Yes; CofC 3028431 | Yes; CofC 3028431 | Yes; CofC 3028431 | |
RCM (formerly C-TICK) | Yes | Yes | Yes | |
KC approval | Yes | Yes | Yes | |
EAC (formerly Gost-R) | Yes | Yes | Yes | |
EN 50155 | Yes; T1 Cat. 1 Cl. A/B horizontal mounting position | |||
Ambient conditions |
|
|
| |
Ambient temperature during operation |
|
|
| |
| -40 °C; = Tmin | -25 °C; = Tmin | -40 °C; = Tmin | |
| 70 °C; = Tmax; 60 °C @ UL/cUL, ATEX and FM use | 60 °C; = Tmax; the rated temperature range of -25 ... +55 °C (T1) applies for the use on railway vehicles according to EN50155 | 70 °C; = Tmax; 60 °C @ UL/cUL use | |
Extended ambient conditions |
|
|
| |
| Tmin ... Tmax at 1080 hPa ... 795 hPa (-1000 m ... +2000 m) Запрос коммерческого предложения× Сообщение отправлено× В ближайшее время сообщение будет обработано. Письмо с номером обращения отправлено на Ваш почтовый ящик. Спасибо за то, что выбрали Первый ZIP! Что-то пошло не так...× К сожалению, наша система расценила Ваше сообщение как спам. Если это произошло по ошибке, пожалуйста, обратитесь к нам по электронной почте. Приносим извинения за возможные неудобства. |