SINAMICS S120M distributed servo drive Siemens
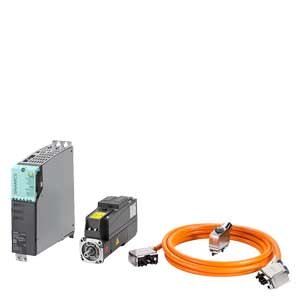
Область применения
Typical SINAMICS S120M applications include the packaging, printing, glass and textile industries.
Обзор
SINAMICS S120M
SINAMICS S120M is the distributed version of the modular SINAMICS S120 drive system. This drive is a compact and turnkey drive unit that comprises
- AM600 Adapter Module for supplying the distributed drive unit
- Distributed drive unit (synchronous servomotor with integrated power unit and encoder)
- Hybrid cable for power and communication
The power unit is not integrated in the control cabinet, as is normally the case, but in the motor for the driven axis. This brings advantages and freedoms for existing or new machine concepts.
Дизайн
The SINAMICS S120M distributed drive system comprises the following units:
- AM600 Adapter Module
- Distributed drive unit (1FK7 synchronous servomotor with integrated Motor Module and multi-turn absolute encoder)
- MOTION-CONNECT hybrid cable
- DRIVE-CLiQ Extension (necessary with more than 6 distributed drive units)
- Hybrid Cabinet Bushing, optional
- Terminating connector (essential for achieving the degree of protection; included in scope of supply of AM600 Adapter Module)
Функции
- The 24 V electronics power supply is either provided from an external supply or from a Control Supply Module (CSM). The supply can also be taken from the central drive line-up using the 24 V terminal connector
- Use of Line Modules (Active Line Module, Basic Line Module and Smart Line Module) from the SINAMICS S120 product family
- The AM600 Adapter Module opens a line of distributed drive units. It feeds the DC link, auxiliary voltage, and DRIVE-CLiQ in a hybrid cable.
- If several drive units are to be operated, then the possible number depends on the central Control Unit. If an additional Control Unit is used, the closed-loop control signals are fed into the DRIVE-CLiQ line via a DRIVE-CLiQ Extension
- AM600 Adapter Module, DRIVE-CLiQ Extension and Hybrid Cabinet Bushing are not "visible" DRIVE-CLiQ nodes in the topology. The number of DRIVE-CLiQ Extensions is not restricted.
- As Control Unit or control, all multi-axis Control Units in the SINAMICS/SIMOTION/SINUMERIK range can generally be used (CU320‑2, D4xx‑2, CX32‑2, NCUxx). The releases of SINAMICS S120M for the corresponding systems are published via the Siemens Industry Online Support Portal: http://support.automation.siemens.com
Principle of a SINAMICS S120M topology
Интеграция
Integration of SINAMICS S120M into the SINAMICS S120 drive system
Modular system for complex drive tasks
SINAMICS S120 solves complex drive tasks for a very wide range of industrial applications and is, therefore, designed as a modular system. Users can choose from many different harmonized components and functions to create a solution that best meets their requirements.
The powerful SIZER for Siemens Drives configuration tool makes it easier to choose and determine the optimum drive configuration.
SINAMICS S120 optimally supports:
- Synchronous and asynchronous motors
- Linear and torque motors
- SINAMICS S120M
System architecture with a central Control Unit:
On the SINAMICS S120, the drive intelligence is combined with closed-loop control functions into Control Units. These units are capable of controlling drives in the vector, servo and V/f modes. They also perform the speed and torque control functions plus other intelligent drive functions for all axes on the drive. Inter-axis connections can be established within a component and easily configured in the STARTER commissioning tool using a mouse.
Functions for higher efficiency
- Basic functions: Speed control, torque control, positioning functions
- Intelligent starting functions for independent restart after power supply interruption
- BICO technology with interconnection of drive-specific DI/DOs for easy adaptation of the drive system to its machine environment
- Integrated safety functions for rational implementation of safety concepts
- Regulated infeed/regenerative feedback functions for preventing undesirable reactions on the supply, allowing recovery of braking energy and ensuring greater stability against line fluctuations.
DRIVE-CLiQ – the digital interface between SINAMICS components
The SINAMICS S120 components, including the motors and encoders, are interconnected via a joint serial interface called DRIVE-CLiQ. The standardized cables and connectors reduce the variety of different parts and cut storage costs. Encoder evaluations for converting standard encoder signals to DRIVE-CLiQ are available for third-party motors or retrofit applications.
Electronic rating plates in all components
An important digital linkage element of the SINAMICS S120 drive system are the electronic rating plates integrated in every component. They allow all drive components to be detected automatically via DRIVE-CLiQ wiring. As a result, data do not need to be entered manually during commissioning or component replacement – helping to ensure that drives are commissioned successfully!
The electronic rating plate contains all the relevant technical data about that particular component. In the motors, for example, this data includes the parameters of the electric equivalent circuit diagram and characteristic values for the built-in motor encoder. In addition to the technical data, the rating plate includes logistical data (manufacturer ID, article number, and ID). Since this data can be called up electronically on site or remotely, all the components used in a machine can always be individually identified, which helps simplify servicing.
Особенности
- Reduced heat losses in the control cabinet thanks to distributed configuration
- Reduced air conditioning in the control cabinet thanks to the power unit integrated into the motor
- Reduced control cabinet volume thanks to the power unit integrated into the motor
- Increased degree of flexibility for modernizations/retrofits thanks to specified control cabinet sizes
- Less time spent on cabling, because the pre-assembled hybrid cable contains all signal and power cables
- Reduction in overall cable length, because the pre-assembled hybrid cable contains all signal and power cables
- Up to 12 distributed drive units can be operated on one AM600 Adapter Module, depending on their power ratings
- Any number of AM600 Adapter Modules can be operated on one appropriately dimensioned infeed
- Drive-integrated DI/DOs for easy adaptation to the machine environment
- All safety variants and communication variants of the SINAMICS S120 system are also available in SINAMICS S120M
- With the Terminal Module (TM54F), all of the safety functions available in the SINAMICS S120 drive system are available
- Optimum integration into the SIMOTION and SINUMERIK system landscape
Технические данные
AM600 Adapter Module | 6SL3555-2BC10-0AA0 |
---|---|
Line connection voltage | 380 ... 480 V 3 AC ±10 % (in operation -15 % <1 min) |
Line frequency | 47 ... 63 Hz |
Electronics power supply (input) |
|
| 24 V DC -15 ... +20 % |
| 20 A |
| 20 A |
Electronics line supply (output) |
|
| 48 V DC |
| 0.45 kW |
| 10 A |
DC link supply |
|
| 510 ... 720 V DC |
| 25 A |
| 21.3 A |
| 30 A |
| 50 A |
| 705 μF ±20 % |
| 100 A |
Rated power, electrical For a DC link voltage of 600 V DC | 14.7 kW |
Total power loss Including electronics losses | 0.06 kW |
Minimum cable length to the 1st axis | 3 m (9.84 ft) |
Format | Booksize compact |
Degree of protection | IP20 |
Ambient temperature during operation, perm. | 0 ... 40 °C (32 ... 104 °F) |
Dimensions |
|
| 75 mm (2.95 in) |
| 270 mm (10.63 in) |
| 224 mm (8.82 in) |
Weight, approx. | 3.2 kg (7 lb) |
1) Only applies for an electronics input voltage > 26.5 V.
Distributed drive unit (synchronous servomotor with Motor Module and encoder) |
| 6SL3532-6DF71-0R.. | 6SL3540-6DF71-0R.. | 6SL3542-6DF71-0R.. | 6SL3562-6DF71-0R.. | 6SL3563-6DF71-0R.. |
---|---|---|---|---|---|---|
Type of construction |
| IM B5 | IM B5 | IM B5 | IM B5 | IM B5 |
Cooling method |
| Surface convection | Surface convection | Surface convection | Surface convection | Surface convection |
Ambient temperature during operation, perm. | °C (°F) | -15 ... +40 (5 ... 104) | -15 ... +40 (5 ... 104) | -15 ... +40 (5 ... 104) | -15 ... +40 (5 ... 104) | -15 ... +40 (5 ... 104) |
Installation altitude, max. | m (ft) | 1000 (3281) | 1000 (3281) | 1000 (3281) | 1000 (3281) | 1000 (3281) |
Max. sound pressure level LpA (1 m) in accordance with DIN EN ISO 1680 Tolerance +3 dB | dB | 55 | 55 | 55 | 65 | 65 |
Vibrational load in operation Acc. to IEC 68‑2‑6, DIN EN 60721 Part 3‑0 and Part 3‑3 |
| Class 3M3 | Class 3M3 | Class 3M3 | Class 3M3 | Class 3M3 |
| mm (in) | 1.5 (0.06) | 1.5 (0.06) | 1.5 (0.06) | 1.5 (0.06) | 1.5 (0.06) |
|
| 0.5 × g | 0.5 × g | 0.5 × g | 0.5 × g | 0.5 × g |
Shock load in operation Acc. to DIN EN 60721 Part 3‑0 and Part 3‑3 |
| Class 3M3 | Class 3M3 | Class 3M3 | Class 3M3 | Class 3M3 |
|
| 7 × g | 7 × g | 7 × g | 7 × g | 7 × g |
| ms | 22 | 22 | 22 | 22 | 22 |
Degree of protection |
|
|
|
|
|
|
|
| IP54 | IP65 | IP65 | IP65 | IP65 |
|
| IP67 | IP67 | IP67 | IP67 | IP67 |
Weight, approx. with brake | kg (lb) | 4.5 (9.9) | 5.7 (12.6) | 7.5 (16.5) | 13 (29) | 15 (33) |
Synchronous servomotor | ||||||
Shaft height |
| 36 | 48 short | 48 long | 63 short | 63 long |
Rated speed | rpm | 3000 | 3000 | 3000 | 3000 | 3000 |
Max. speed | rpm | 9000 | 9000 | 6400 | 5600 | 6400 |
Rated torque | Nm (lbf-in) | 0.8 (7.08) | 1.05 (9.29) | 1.8 (15.9) | 2.7 (23.9) | 2.2 (19.5) |
Max. torque | Nm (lbf-in) | 3 (26.6) | 4.9 (43.4) | 10 (88.5) | 19.3 (171) | 27 (239) |
Static torque | Nm (lbf-in) | 1 (8.85) | 1.3 (11.5) | 2.5 (22.1) | 5 (44.3) | 7.1 (62.8) |
Stall current | A | 1.4 | 1.9 | 1.8 | 3.15 | 5 |
Moment of inertia |
|
|
|
|
|
|
| kgm2 (lbf-in-s2) | 0.065 × 10-3 (0.58 × 10-3) | 0.16 × 10-3 (1.42 × 10-3) | 0.29 × 10-3 (2.57 × 10-3) | 1.12 × 10-3 (9.91 × 10-3) | 1.47 × 10-3 (13 × 10-3) |
| kgm2 (lbf-in-s2) | 0.075 × 10-3 (0.66 × 10-3) | 0.192 × 10-3 (1.7 × 10-3) | 0.32 × 10-3 (2.83 × 10-3) | 1.22 × 10-3 (10.8 × 10-3) | 1.57 × 10-3 (13.9 × 10-3) |
Shaft torsional stiffness | Nm/rad | 4100 | 13000 | 11400 | 26500 | 25000 |
Motor Module | ||||||
Electronics power supply | V DC | 48 | 48 | 48 | 48 | 48 |
Power consumption, max. | W | 12 | 12 | 12 | 12 | 12 |
Power consumption, brake | W | 10 | 15 | 15 | 20 | 20 |
Rated DC link voltage | V DC | 600 | 600 | 600 | 600 | 600 |
DC link voltage | V DC | 510 ... 720 | 510 ... 720 | 510 ... 720 | 510 ... 720 | 510 ... 720 |
Output voltage | V AC | 0 ... 0.717 × DC link voltage | 0 ... 0.717 × DC link voltage | 0 ... 0.717 × DC link voltage | 0 ... 0.717 × DC link voltage | 0 ... 0.717 × DC link voltage |
Overvoltage trip | V DC | 820 ±2 % | 820 ±2 % | 820 ±2 % | 820 ±2 % | 820 ±2 % |
Undervoltage trip | V DC | 380 ±2 % | 380 ±2 % | 380 ±2 % | 380 ±2 % | 380 ±2 % |
Current-carrying capacity of the DC link | A | 25 | 25 | 25 | 25 | 25 |
DC link capacitance | μF | 8 | 24 | 24 | 48 | 48 |
Pulse frequency | kHz | 4 | 4 | 4 | 4 | 4 |
Output current |
|
|
|
|
|
|
| A | 1.2 | 1.7 | 1.4 | 1.9 | 2 |
| A | 1.1 | 2.5 | 2 | 1.4 | 1.5 |
| A | 1.7 | 1.3 | 1.1 | 2.8 | 2.9 |
| A | 4.5 | 7.7 | 7.6 | 14 | 21 |
Surface temperature | °C (°F) | <100 (212) | <100 (212) | <100 (212) | <100 (212) | <100 (212) |
Encoder (absolute encoder AM20DQI) | ||||||
Resolution within one revolution | bit | 20 | 20 | 20 | 20 | 20 |
Traversing range (multi-turn) | Revolutions | 4096 | 4096 | 4096 | 4096 | 4096 |
Hybrid cable | 6FX8002-7HY..-.... |
---|---|
Cross-section | 4 mm2 |
Max. line length per AM600 Adapter Module | 100 m (328 ft) |
Max. current-carrying capacity | 25 A |
Дальнейшая информация
Further information is available at
http://www.siemens.com/sinamics-s120
In the SITRAIN learning concept, SINAMICS S120M is handled in courses DR‑SN‑UEB and DR‑SNS‑SI.
Further information about the courses is available at
http://www.siemens.de/sitrain