Complementary S7-400 systems Siemens
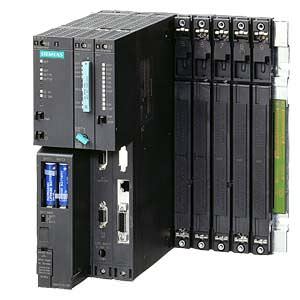
Обзор
With the S7-400 automation systems, which are scalable via different types of CPU, you have an alternative to AS 410 automation systems. The systems that can be used in plants with SIMATIC PCS 7 V7/V8 can be classified as follows:
- Standard automation systems
- High availability automation systems
- Safety-related automation systems
Standard automation systems
The AS 414‑3, AS 414‑3IE, AS 416‑2, AS 416‑3, AS 416‑3IE and AS 417‑4 standard automation systems are extremely robust and feature high processing and communication performance.
The AS 414-3 and AS 414-3IE are tailored for smaller-scale applications with smaller quantity structures. This allows for a low-cost starter solution with a modular and scalable system based on the S7-400 controller range. Larger quantity frameworks can be implemented with the AS 416-2, AS416-3/416-3IE and AS 417-4 automation systems. These systems are preferred for medium and large-sized plants.
High availability automation systems
The aim in using high availability automation systems is to minimize the risk of a production outage. In accordance with their basic design, these systems are categorized as:
- AS Single Stations: AS 412-5-1H, AS 414‑5‑1H, AS 416‑5‑1H, and AS 417‑5‑1H with only one CPU, e.g. for the following applications:
- Subsequent expansion to a redundant system
- Redundant configuration on UR1 racks, comprising 2 single stations, 4 sync modules, and 2 sync fiber-optic cables
- AS Redundancy Stations: AS 412‑5‑2H, AS 414‑5‑2H, AS 416‑5‑2H and AS 417‑5‑2H with two redundant CPUs, mounted on one common rack (UR2‑H) or two separate racks (UR2)
Safety-related automation systems
Safety-related automation systems (F/FH systems) are available for safety-relevant applications in which an incident can result in danger to persons, plant damage or environmental pollution. These are based on the hardware of the high availability automation systems, which is expanded by safety functions with S7 F systems.
In accordance with the design variant, they are categorized as:
- AS Single Stations
AS 412F, AS 414F, AS 416F, and AS 417F with only one CPU (safety-related) - AS Redundancy Stations
AS 412FH, AS 414FH, AS 416FH, and AS 417FH with two redundant CPUs (safety-related and high availability)
The safety-related F/FH systems collaborate with safety-related F modules of the ET 200 distributed I/O systems or fail-safe transmitters connected directly via the fieldbus to detect not only faults in the process, but also their own, internal faults. They automatically transfer the plant to a safe state in the event of a fault. The redundancy of the FH systems is only used to increase the availability. It is not relevant to processing of the safety functions and the associated fault detection.
All F/FH systems are TÜV-certified and comply with the safety requirements up to SIL 3 according to IEC 61508.
Дизайн
Racks
Automation systems based on only one CPU (AS Single Station) can be mounted on a UR1 rack (18 slots) or UR2 rack (9 slots).
The automation systems (AS Redundancy Station) consisting of two electrically isolated redundant subsystems can be mounted on a UR2‑H compact rack with divided backplane bus or on two separate racks (UR1 or UR2). The design with two racks allows physical separation of the redundant subsystems, e.g. by a fireproof partition and over a distance of up to 10 km. As a result of the galvanic isolation, the system is insensitive to electromagnetic interferences.
Redundant power supply
If you have two separate power supplies for supplying your system, you can increase the availability of the automation systems with redundant power supplies (2 power supplies for one AS Single Station or 1 or 2 power supplies for each subsystem of an AS Redundancy Station).
Communication via the Industrial Ethernet (IE) plant bus
Each standard automation system is connected to the Industrial Ethernet plant bus by means of a CP 443‑1 communication module.
If the PN/IE interface integrated in the CPUs of the high availability and safety-related automation systems is not used for PROFINET IO, it is available for the connection to the Industrial Ethernet plant bus. Otherwise, the 1H/F systems (AS Single Station) and the two subsystems of the 2H/FH systems (AS Redundancy Station) can be connected to the plant bus via one CP 443‑1 communication module each.
I/O connection via PROFIBUS DP
The distributed process I/O can be integrated into a PROFIBUS DP segment either directly or via a lower-level fieldbus (PROFIBUS PA or FOUNDATION Fieldbus H1).
Several PROFIBUS DP segments with distributed process I/Os can be operated on a standard automation system, an 1H/F system (AS Single Station), or a 2H/FH system (AS Redundancy Station). The following table provides an overview of the number and type of configurable PROFIBUS DP interfaces.
AS type | PROFIBUS interfaces | |||||||
1 | 2 | 3 | 4 | 5 | 6 | 7 | 8 | |
AS 412-5-1H/AS 412F | MPI/DP | DP | CP | CP | CP | CP | ||
AS 412-5-2H/AS 412FH | MPI/DP | DP | CP | CP | CP | CP | ||
AS 414-5-1H/AS 414F | MPI/DP | DP | CP | CP | CP | CP | ||
AS 414-5-2H/AS 414FH | MPI/DP | DP | CP | CP | CP | CP | ||
AS 416-5-1H/AS 416F | MPI/DP | DP | CP | CP | CP | CP | ||
AS 416-5-2H/AS 416FH | MPI/DP | DP | CP | CP | CP | CP | ||
AS 417-5-1H/AS 417F | MPI/DP | DP | CP | CP | CP | CP | ||
AS 417-5-2H/AS 417FH | MPI/DP | DP | CP | CP | CP | CP | ||
AS 416-2 | MPI/DP | DP | CP | CP | CP | CP | ||
AS 414-3IE | MPI/DP | IF | CP | CP | CP | CP | ||
AS 416-3IE | MPI/DP | IF | CP | CP | CP | CP | ||
AS 414-3 | MPI/DP | DP | IF | CP | CP | CP | CP | |
AS 416-3 | MPI/DP | DP | IF | CP | CP | CP | CP | |
AS 417-4 | MPI/DP | DP | IF | IF | CP | CP | CP | CP |
Overview of number and type of configurable PROFIBUS interfaces
MPI/DP = integrated MPI/DP interface (for up to 32 PROFIBUS DP nodes) DP = integrated PROFIBUS DP interface IF = optional PROFIBUS DP interface module CP = additive PROFIBUS DP interface module CP 443-5 Extended
I/O connection via PROFINET (PN)
Standard automation systems, high availability and safety-oriented automation systems (AS Single Stations and AS Redundancy Stations) can be networked simply and effectively with ET 200M remote I/O stations over PROFINET IO. If a PN/IE interface is integrated in the CPU of the automation system (AS 414‑3IE, AS 416‑3IE, and all H/F/FH systems), then it is to be used for connecting ET 200M remote I/O stations via PROFINET IO. In standard automation systems, the PN/IE interfaces of type CP 443-1 communication modules can also be used for PROFINET IO.
The maximum availability with minimum error handling times is achieved by the AS Redundancy Station (2 H/FH systems) in conjunction with the system redundancy of the I/O devices. System redundancy refers to a type of PROFINET IO communication where each I/O device establishes a communication connection to each of the two CPUs of an AS Redundancy Station over the topological network.
Runtime licenses
Each automation system is already provided as standard with the SIMATIC PCS 7 Industry Library Runtime and the SIMATIC PCS 7 AS Runtime license for 100 process objects (PO); safety-oriented automation systems additionally with the S7 F Systems RT license. The 100 POs of the SIMATIC PCS 7 AS Runtime license can be expanded by additional Runtime licenses for 100, 1 000 or 10 000 POs. The process objects of additional Runtime licenses can be added to process objects which already exist. Number and type of additional Runtime licenses (for example, 100 or 1000) are irrelevant.
Individual configuration of AS bundles
The various versions of the SIMATIC PCS 7 automation systems AS 412 to AS 417 are available as AS bundles as follows:
- Individual components, combined per station in one consignment
- Preassembled and tested complete systems (no extra charge compared to delivery of individual components)
Typical combinations can be selected from tables in the section "Selection and ordering data".
The complete range is available to you via two configurators in the Industry Mall:
- SIMATIC PCS 7 AS Single Station configurator
- SIMATIC PCS 7 AS Redundancy Station configurator
Ordering notes
- For a redundant configuration based on 2 AS Single Stations, you additionally require 4 sync modules (up to 10 m or 10 km) and 2 fiber-optic sync cables. The selection depends on the distance between the two AS Single Stations.
- FO sync cables longer than 1 m must always be ordered separately (2 cables required in each case).
Дополнительно
Backup batteries
Lithium backup batteries of type AA with 2.3 Ah are used in the power supply modules of all SIMATIC PCS 7 automation systems AS 412 to AS 417. Since lithium batteries are easily inflammable, more rigorous transport and storage regulations apply to them.
To avoid subjecting the AS bundles to these more rigorous transport and storage regulations, the backup batteries must be ordered and delivered separately (order no. 6ES7971-0BA00).
The following backup batteries are required depending on the configuration of the AS bundles:
- SIMATIC PCS 7 AS Single Station:
- With 1 power supply module: 2 units
- With 2 redundant power supply modules: 4 units
- SIMATIC PCS 7 AS Redundancy Station:
- With 2 power supply modules: 4 units
- With 2 x 2 redundant power supply modules: 8 units