Power Modules Siemens
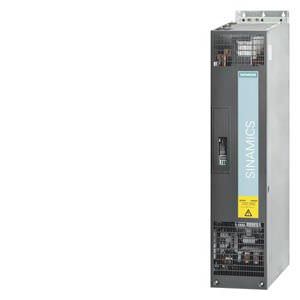
Обзор
The Power Module comprises a line rectifier, a DC link and an inverter to supply the motor.
Power Modules are designed for drives that are not capable of regenerating energy to the mains supply. Regenerative energy produced while braking is converted to heat using braking resistors.
Power Modules in the chassis format can be connected to grounded TN/TT systems and non-grounded IT systems.
Дизайн
The Power Modules have the following interfaces as standard:
- 1 line supply connection
- 2 DC link connections for options, e.g. Braking Modules
- 3 DRIVE-CLiQ sockets
- 1 connection for Safety Integrated
- 1 temperature sensor input (KTY84-130, PTC or Pt100)
- 1 connection for the 24 V DC electronics power supply
- 1 motor connection
- 2 PE/protective conductor connections
The Power Modules are controlled by the CU310 Control Unit that can be integrated into the Power Module.
The scope of supply of the Power Modules includes:
- 1 DRIVE-CLiQ cable for connection to the CU310/ SIMOTION D410 Control Unit
- 1 24 V DC connecting cable for the power supply to the CU310/SIMOTION D410 Control Unit
- 1 mounting plate for attaching the CU310/SIMOTION D410 Control Unit
Интеграция
The Power Modules communicate with the higher-level control module via DRIVE-CLiQ. The control module in this case can be a CU310, CU320-2 or a SIMOTION D Control Unit.
Connection example of a Power Module
Note: The integrated 24 V power supply at connector X42 can have a maximum load of 2 A. When the Control Unit is supplied from the integrated power supply, the total load of the digital outputs must be carefully observed in order that the 2 A is not exceeded.
Технические данные
General technical specifications
Electrical specifications | |
---|---|
Line supply voltage Up to 2000 m above sea level | 380 … 480 V 3 AC ±10 % (-15 % < 1 min) |
Line power factor for a three-phase AC line supply voltage and output power | |
| > 0.96 |
| 0.75 … 0.93 |
DC link voltage, approx. 1) | 1.35 × line voltage |
Output voltage, approx. | 0.97 × Uline |
Output frequency 2) | |
| 0 … 650 Hz |
| 0 … 600 Hz |
| 0 … 600 Hz |
Main contactor control | |
| 240 V AC, max. 8 A |
Conformity | CE (EMC Directive No. 2004/108/EC and Low-Voltage Directive No. 2006/95/EC) |
Approvals, according to | cULus |
Safety Integrated | Safety Integrity Level 2 (SIL2) acc. to IEC 61508, Performance Level d (PLd) acc. to EN ISO 13849-1 and Control Category 3 acc. to EN ISO 13849-1 (previously EN 954-1). |
1) The DC link voltage is unregulated and load-dependent. For additional information, please refer to the SINAMICS Low Voltage Engineering Manual.
2) Please note:
- The correlation between the maximum output frequency, pulse frequency and current derating. Higher output frequencies for specific configurations are available on request.
- The correlation between the minimum output frequency and permissible output current (current derating).
Information is provided in the SINAMICS Low Voltage Engineering Manual.
Line Voltage 380 … 480 V 3 AC | Power Modules | |||||
---|---|---|---|---|---|---|
|
| 6SL3310-1TE32-1AA3 | 6SL3310-1TE32-6AA3 | 6SL3310-1TE33-1AA3 | 6SL3310-1TE33-8AA3 | 6SL3310-1TE35-0AA3 |
Type rating | ||||||
| kW | 110 | 132 | 160 | 200 | 250 |
| kW | 90 | 110 | 132 | 160 | 200 |
| hp | 150 | 200 | 250 | 300 | 400 |
| hp | 150 | 200 | 200 | 250 | 350 |
Output current | ||||||
| A | 210 | 260 | 310 | 380 | 490 |
| A | 205 | 250 | 302 | 370 | 477 |
| A | 178 | 233 | 277 | 340 | 438 |
| A | 307 | 375 | 453 | 555 | 715 |
Input current | ||||||
| A | 229 | 284 | 338 | 395 | 509 |
| A | 335 | 410 | 495 | 606 | 781 |
Current demand | ||||||
| A | 0.8 | 0.8 | 0.9 | 0.9 | 0.9 |
Pulse frequency 5) | ||||||
| kHz | 2 | 2 | 2 | 2 | 2 |
| ||||||
| kHz | 2 | 2 | 2 | 2 | 2 |
| kHz | 8 | 8 | 8 | 8 | 8 |
Power loss, max. 6) | ||||||
| kW | 2.46 | 3.27 | 4 | 4.54 | 5.78 |
| kW | 2.54 | 3.36 | 4.07 | 4.67 | 5.96 |
Cooling air requirement | m3/s | 0.17 | 0.23 | 0.36 | 0.36 | 0.36 |
Sound pressure level LpA (1 m) at 50/60 Hz | dB | 64/67 | 64/67 | 69/73 | 69/73 | 69/73 |
Line supply connection U1, V1, W1 |
| M10 screw | M10 screw | M10 screw | M10 screw | M10 screw |
| mm2 | 2 × 185 | 2 × 185 | 2 × 240 | 2 × 240 | 2 × 240 |
Motor connection U2/T1, V2/T2, W2/T3 |
| M10 screw | M10 screw | M10 screw | M10 screw | M10 screw |
| mm2 | 2 × 185 | 2 × 185 | 2 × 240 | 2 × 240 | 2 × 240 |
Cable length, max. 7) | ||||||
| m | 300 | 300 | 300 | 300 | 300 |
| m | 450 | 450 | 450 | 450 | 450 |
PE1/GND connection |
| M10 screw | M10 screw | M10 screw | M10 screw | M10 screw |
| mm2 | 2 × 185 | 2 × 185 | 2 × 240 | 2 × 240 | 2 × 240 |
PE2/GND connection |
| M10 screw | M10 screw | M10 screw | M10 screw | M10 screw |
| mm2 | 2 × 185 | 2 × 185 | 2 × 240 | 2 × 240 | 2 × 240 |
Degree of protection |
| IP20 | IP20 | IP20 | IP20 | IP20 |
Dimensions | ||||||
| mm | 326 | 326 | 326 | 326 | 326 |
| mm | 1400 | 1400 | 1533 | 1533 | 1533 |
| mm | 356 8) | 356 8) | 549 | 549 | 549 |
Weight, approx. | kg | 104 | 104 | 162 | 162 | 162 |
Frame size |
| FX | FX | GX | GX | GX |
1) Rated power of a typ. 6-pole standard induction motor based on IL or IH with 400 V 3 AC 50 Hz.
2) Rated power of a typ. 6-pole standard induction motor based on IL or IH with 460 V 3 AC 60 Hz.
3) The base load current IL is the basis for a duty cycle of 110 % for 60 s or 150 % for 10 s with a duty cycle duration of 300 s.
4) The base load current IH is the basis for a duty cycle of 150 % for 60 s or 160 % for 10 s with a duty cycle duration of 300 s.
5)Information regarding the correlation between the pulse frequency and maximum output current/output frequency is provided in the SINAMICS Low Voltage Engineering Manual.
6) The specified power loss represents the maximum value at 100 % utilization. The value is lower under normal operating conditions.
7) Longer cable lengths depending on the configuration on request.
Additional information is provided in the SINAMICS Low Voltage Engineering Manual.
8) Depth = 421 mm including front cover when the CU 310 Control Unit is installed.