PROFINET Siemens
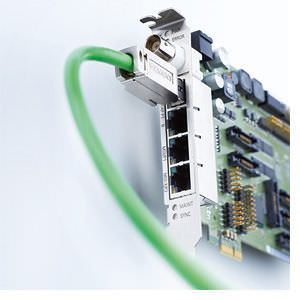
Обзор
PROFINET – стандарт Ethernet для автоматизации
С наличием более чем 5.8 миллионов применений по всему миру, PROFINET - лидирующий Industrial Ethernet стандарт для автоматизации (источник: PROFIBUS & PROFINET International (PI) Edition 2013). Объединяя преимущества полевой шины PROFIBUS и открытого сетевого стандарта Ethernet, Profinet характеризуется черезвычайной гибкостью, эффективностью и производительностью. Эти факторы существенны для для ускорения информационных процессов, повышения их надежности и эффективности.
Функции
PROFINET aspects focused on process automation
Open standard
The open vendor-independent standard (IEC 61158/61784), PROFINET, is supported by PROFIBUS and PROFINET International (PI). It stands for maximum transparency, open IT communication, network security and real-time communication down to the field level.
Due to its openness, PROFINET creates the basis for a uniform automation network in the plant to which all of the devices can be connected. Existing plant parts, for example those implemented with the PROFIBUS fieldbus, can be easily integrated.
Flexible topologies
In addition to a line topology, PROFINET also supports star, tree and ring topologies. This is made possible by switching technology, which is based on active network components (Industrial Ethernet switches and media converters) and field devices/components with integrated switch functionality. This all results in more flexibility for plant planning as well as savings in cabling.
The PROFINET network meets all the requirements relevant for the industrial sector. It can be installed without any specialist knowledge. A PROFINET "Cabling and Interconnection Technology" guideline provides network installation support for manufacturers and users. Symmetrical copper cables or fiber-optic cables resistant to electromagnetic interference are used depending on the application. Devices from various manufacturers are easily connected via rugged, standardized plug-in connectors (up to IP65/IP67).
Expandability
Integrating existing systems and networks is simple and requires little effort and expense. This enables you to protect your investments in plant units with communication via PROFIBUS and other fieldbuses (e.g. AS-Interface).
Additional PROFINET stations can be integrated at any time as well. The use of additional network components allows both wired and wireless network infrastructures to be expanded.
Safety
The PROFIsafe safety profile, which has been tried and tested with PROFIBUS and which permits the transmission of standard and safety-related data on a single bus cable, can also be used with PROFINET. No special network components are required for fail-safe communication, standard switches and standard network transitions can be used without restrictions.
Industrial Wireless LAN (IWLAN)
PROFINET also supports wireless communication with Industrial Wireless LAN and thus opens up new application fields.
Device and network diagnostics
Retaining the proven PROFIBUS model makes the same diagnostic information available for PROFINET. In addition, device diagnostics also includes read-out of module-specific and channel-specific data from the devices. This enables simple and fast location of faults. In addition to the availability of device information, the top priority in network management is to achieve reliable network operation. PROFINET uses the Simple Network Management Protocol (SNMP) for maintenance and monitoring of the network components and their functions.
Easy cabling
Industry-standard networks require no specialist knowledge and can be configured without problems in the shortest possible time. At the same time, stringent demands are placed on the installation of cables in the industrial environment.
Siemens offers the FastConnect assembly system, which meets these requirements. FastConnect is the standards-compliant, industry-standard cabling system for PROFINET networks consisting of cables, connectors, and assembly tools.
The time required for connecting the terminal devices is minimized due to the easy installation using just one tool. The practical color coding helps avoid installation errors. Both copper cables and glass fiber-optic cables can be easily assembled on-site in this way.
Ruggedness/stability
An automation network must be extremely resistant to external sources of interference. Switched Ethernet prevents faults in one section of the network from influencing the entire plant network. Highly resistant fiber-optic cables can be used in particularly EMC-critical areas.
Speed and precision
PROFINET communication is fast, deterministic and precise. It is based on Real Time Ethernet (RT) with prioritization of the transmission and division of the bandwidth.
With PROFIdrive, the standardized drive profile, vendor-independent communication between CPUs and drives can be implemented as well.
Large quantity structures
A SIMATIC PCS 7 controller (automation system) can manage up to 256 devices in the field via PROFINET. The number of nodes in a PROFINET network is practically unlimited since the entire IP address range is available.
With 64 KB of user data per message frame, the transmittable volume of data on PROFINET is significantly greater than with PROFIBUS DP with 244 bytes.
High transmission rate
Based on Ethernet, PROFINET with 100 Mbit/s in full duplex mode achieves a significantly higher transmission rate than previous fieldbuses. The transmission of large volumes of data has no effect on the I/O data transfer.
Media redundancy
Higher plant availability can be achieved by means of a redundant installation (ring topology). Media redundancy can be implemented with both external switches and via integrated PROFINET interfaces. It prevents plant standstill should an interruption in the communication in part of the ring installation occur. Re-configuration times of 200 ms can be achieved. Required maintenance and repair work can thus be performed without time pressure.
Особенности
- PROFINET открытый промышленный Ethernet стандарт для автоматизации
- PROFINET базируется на Industrial Ethernet
- PROFINET использует TCP/IP и IT стандарты
- PROFINET - Ethernet реального времени
- PROFINET позволяет бесшовную интеграцию систем полевой шины
- PROFINET поддерживает fail-safe коммуникации через PROFIsafe