SIPLUS MICROMASTER 440 Siemens
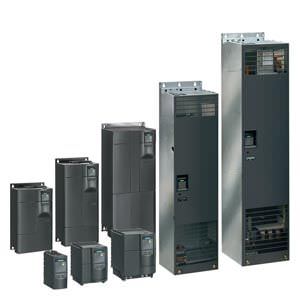
Обзор
General technical specifications of the SIPLUS MICROMASTER 440
Ambient temperature range | -10 ... +50 °C |
Conformal Coating | Coating of the printed circuit board and the electronic components |
Technical specifications | The technical specifications of the standard product apply with the exception of the ambient conditions. |
Ambient conditions | |
Relative atmospheric humidity | 5 … 100%, |
Application
The SIPLUS MICROMASTER 440 inverter can be used for a variety of variable-speed drive tasks. Its flexibility makes it suitable for a wide range of applications. This wide range includes cranes and hoisting gear, high-bay warehouses, machines for the food and beverages industry, packaging machines, etc.; i.e. applications that require frequency inverters with higher functionality and higher dynamic response than normal.
The inverter is especially characterized by its customer-oriented performance and ease-of-use. Its large range of line voltages enables it to be used all over the world.
Design
The SIPLUS MICROMASTER 440 inverter has a modular design. The operator panels and modules can be easily exchanged.
Main features
- Easy, guided commissioning
- Modular construction allows maximum configuration flexibility
- 6 programmable isolated digital inputs
- 2 analog inputs (0 V to 10 V, 0 mA to 20 mA, scalable) can also be used as a 7th/8th digital input
- 2 programmable analog outputs (0 mA to 20 mA)
- 3 programmable relay outputs (30 V DC/5 A, resistive load; 250 V AC/2 A, inductive load
- Low-noise motor operation through high pulse frequencies, adjustable (observe derating if necessary)
- Protection for motor and inverter
Accessories (overview)
- EMC filter, class A/B
- LC filter and sine-wave filter
- Line commutating reactors
- Output reactors
- Shield connection plates
- Basic Operator Panel (BOP) for parameterizing the inverter
- Plain-text Advanced Operator Panel (AOP) with multiple-language display
- Plain-text Asian Advanced Operator Panel (AAOP) with Chinese and English display
- Plain-text Cyrillic Advanced Operator Panel (CAOP) with Cyrillic, German and English display
- Communication modules
- PROFIBUS
- DeviceNet
- CANopen
- Incremental encoder evaluation module
- PC connection kits
- Mounting kits for installing the operator panels in control cabinet doors
- PC commissioning programs under Windows 98/NT/2000/XP Professional
- TIA integration with Drive ES
International standards
- The MICROMASTER 440 inverter fulfills the requirements of the EU low-voltage directive
- The MICROMASTER 440 inverter has CE marking.
- Certified according to uL and c uL
- c-tick
Mechanical characteristic data
- Modular design
- Operating temperature
- 0.12 kW to 75 kW: -10 °C to +50 °C (+14 °F to +122 °F)
- 90 kW to 200 kW: 0 °C to +40 °C (+32 °F to +104 °F)
- Compact enclosure due to high power density
- Simple cable connection, separate mains and motor connections for optimum electromagnetic compatibility
- Plug-in operator panels
- Screwless control terminal strip on removable I/O board
Performance characteristic data
- Latest IGBT technology
- Digital microprocessor control
- High-quality vector control
- Flux current control (FCC) for enhanced dynamic response and optimized motor control
- U/f characteristic linear
- U/f characteristic quadratic
- Multipoint characteristic (programmable U/f characteristic)
- Torque control
- Flying restart
- Slip compensation
- Automatic restart after mains failure or operational fault
- Free function blocks for logic and arithmetic operations
- Kinetic buffering
- Positioning down ramp
- High-quality internal PID controller for simple process control (autotuning)
- Programmable ramp-up/ramp-down times 0 s to 650 s
- Ramp smoothing
- Fast current limitation (FCL) for uninterrupted operation
- Fast, reproducible response from the digital inputs
- Precise setpoint input by means of 2 high-resolution 10-bit analog inputs
- Compound braking for controlled rapid braking
- Integrated Braking Module (only for inverters 0.12 kW to 75 kW)
- 4 skip frequencies
- Removable "Y" capacitor for use on IT networks (with ungrounded networks the "Y" capacitor must be removed and an output reactor installed)
Protection characteristic data
- Overload capability
- CT operation
0.12 kW to 75 kW:
overload current 1.5 x rated output current (i.e. 150% overload capability) for 60 s, cycle time 300 s,
and 2 x rated output current (i.e. 200% overload capability) for 3 s, cycle time 300 s
90 kW to 200 kW:
overload current 1.36 x rated output current (i.e. 136% overload capability) for 57 s, cycle time 300 s,
and 1.6 x rated output current (i.e. 160% overload capability) for 3 s, cycle time 300 s - VT operation
5.5 kW to 90 kW:
overload current 1.4 x rated output current (i.e. 140% overload capability) for 3 s,
and 1.1 x rated output current (i.e. 110% overload capability) for 60 s, cycle time 300 s
110 kW to 250 kW:
overload current 1.5 x rated output current (i.e. 150% overload capability) for 1 s,
and 1.1 x rated output current (i.e. 110% overload capability) for 59 s, cycle time 300 s
- CT operation
- Overvoltage/undervoltage protection
- Overtemperature protection for the inverter
- Special direct connection for PTC or KTY for motor protection
- Ground-fault protection
- Short-circuit protection
- Thermal motor protection I2t
- Motor blocking protection
- Stall protection
- Parameter locking
Технические данные
Technical data | MICROMASTER 440 | ||||||||
---|---|---|---|---|---|---|---|---|---|
Mains voltage and power ranges |
| CT (constant torque) | VT (variable torque) | ||||||
200 V to 240 V 1 AC ±10 % | 0.12 kW to 3 kW | - | |||||||
200 V to 240 V 3 AC ±10 % | 0.12 kW to 45 kW | 5.5 kW to 55 kW | |||||||
380 V to 480 V 3 AC ±10 % | 0.37 kW to 200 kW | 7.5 kW to 250 kW | |||||||
500 V to 600 V 3 AC ±10 % | 0.75 kW to 75 kW | 1.5 kW to 90 kW | |||||||
Input frequency | 47 Hz to 63 Hz | ||||||||
Output frequency | in V/f mode
| for inverter 0.12 kW to 75 kW | 0 Hz to 650 Hz (Due to legal restrictions a limitation to 550 Hz is under preparation) | ||||||
for inverter 90 kW to 200 kW | 0 Hz to 267 Hz | ||||||||
in vector mode
| for inverter 0.12 kW to 75 kW | 0 Hz to 200 Hz | |||||||
for inverter 90 kW to 200 kW | 0 Hz to 200 Hz | ||||||||
Power factor | ≥ 0.95 | ||||||||
Inverter efficiency | 0.12 kW to 75 kW: 96 % to 97 %; 90 kW to 200 kW: 97 % to 98 % | ||||||||
Overload capability CT mode | for inverter 0.12 kW to 75 kW | Overload current 1.5 x rated output current (i.e. 150 % overload capability) for 60 s, cycle time 300 s, and 2 x rated output current (i.e. 200 % overload capability) for 3 s, cycle time 300 s | |||||||
for inverter 90 kW to 200 kW | Overload current 1.36 x rated output current (i.e. 136 % overload capability) for 57 s, cycle time 300 s, and 1.6 x rated output current (i.e. 160 % overload capability) for 3 s, cycle time 300 s | ||||||||
Overload capability VT mode | for inverter 5.5 kW to 90 kW | Overload current 1.4 x rated output current (i.e. 140 % overload capability) for 3 s, and 1.1 x rated output current (i.e. 110 % overload capability) for 60 s, cycle time 300 s | |||||||
for inverter 110 kW to 250 kW | Overload current 1.5 x rated output current (i.e. 150 % overload capability) for 1 s, and 1.1 x rated output current (i.e. 110 % overload capability) for 59 s, cycle time 300 s | ||||||||
Inrush current | not higher than rated input current | ||||||||
Control method | Vector control, torque control, linear V/f characteristic; quadratic V/f characteristic; multipoint characteristic (programmable V/f characteristic); flux current control (FCC) | ||||||||
Pulse frequency | for inverter 0.12 kW to 75 kW | 4 kHz (standard); 16 kHz (standard with 230 V inverters 0.12 kW to 5.5 kW) | |||||||
for inverter 90 kW to 200 kW | 2 kHz (standard with VT mode); 4 kHz (standard with CT mode) | ||||||||
Fixed frequencies | 15, programmable | ||||||||
Skip frequency ranges | 4, programmable | ||||||||
Setpoint resolution | 0.01 Hz digital | ||||||||
Digital inputs | 6 fully programmable isolated digital inputs; switchable PNP/NPN | ||||||||
Analog inputs | 2 programmable analog inputs
| ||||||||
Relay outputs | 3, programmable | ||||||||
Analog outputs | 2, programmable (0/4 mA to 20 mA) | ||||||||
Serial interfaces | RS-485, optional RS-232 | ||||||||
Motor cable lengths | Without output choke | for inverter 0.12 kW to 75 kW | max. 50 m (shielded) | ||||||
for inverter 90 kW to 250 kW | max. 200 m (shielded) | ||||||||
With output choke | see variant dependent options | ||||||||
Electromagnetic compatibility (see Selection and Ordering Data) | EMC filter, Class A or Class B to EN 55 011 available as an option | ||||||||
Braking | Resistance braking with DC braking, compound braking, integrated brake chopper (integrated brake chopper only with 0.12 kW to 75 kW inverters) | ||||||||
Degree of protection | IP20 | ||||||||
Operating temperature (without derating) | for inverter 0.12 kW to 75 kW | CT: -10 °C to +50 °C (+14 °F to +122 °F) | |||||||
for inverter 90 kW to 200 kW | 0 °C to +40 °C (+32 °F to +104 °F) | ||||||||
Storage temperature | -40 °C to +70 °C (-40 °F to +158 °F) | ||||||||
Relative humidity | 95 % (non-condensing) | ||||||||
Installation altitude | for inverter 0.12 kW to 75 kW | up to 1000 m above sea level without derating | |||||||
for inverter 90 kW to 200 kW | up to 2000 m above sea level without derating | ||||||||
Standard SCCR | FSA, FSB, FSC: 10 kA | ||||||||
Protection features for | Undervoltage, overvoltage, overload, earth faults, short-circuits, stall prevention, locked motor protection, motor overtemperature, inverter overtemperature, parameter change protection | ||||||||
Compliance with standards | uL, c uL, CE, c-tick | ||||||||
CE marking | Conformity with low-voltage directive 73/23/EEC | ||||||||
Cooling-air volumetric flow required, dimensions and weights (without options) | Frame size (FS) | Cooling-air volumetric flow required (l/s)/(CFM) | H x W x D, max. (mm) | Weight, approx. (kg) | |||||
A | 4.8/10.2 | 173 x 73 x 149 | 1.3 | ||||||
B | 24/51 | 202 x 149 x 172 | 3.4 | ||||||
C | 54.9/116.3 | 245 x 185 x 195 | 5.7 | ||||||
D | 2 x 54.9/2 x 116.3 | 520 x 275 x 245 | 17 | ||||||
E | 2 x 54.9/2 x 116.3 | 650 x 275 x 245 | 22 | ||||||
F without filter | 150/317.79 | 850 x 350 x 320 | 56 | ||||||
F with filter | 150/317.79 | 1150 x 350 x 320 | 75 | ||||||
FX | 225/478.13 | 1400 x 326 x 356 | 116 | ||||||
GX | 440/935 | 1533 x 326 x 545 | 174 | ||||||
| CFM: |
|
|
1) Applies to industrial control cabinet installations to NEC article 409/UL 508A.
Derating data
Pulse frequency
Output | Rated output current in A for a pulse frequency of | ||||||
---|---|---|---|---|---|---|---|
kW | 4 kHz | 6 kHz | 8 kHz | 10 kHz | 12 kHz | 14 kHz | 16 kHz |
Mains operating voltage 200 V 1/3 AC | |||||||
0.12 to 5.5 | Values correspond to the 4 kHz standard values. No derating, since 16 kHz standard. | ||||||
7.5 | 28.0 | 26.6 | 25.2 | 22.4 | 19.6 | 16.8 | 14.0 |
11 | 42.0 | 37.8 | 33.6 | 29.4 | 25.2 | 21.0 | 16.8 |
15 | 54.0 | 48.6 | 43.2 | 37.8 | 32.4 | 27.0 | 21.6 |
18.5 | 68.0 | 64.6 | 61.2 | 54.4 | 47.6 | 40.8 | 34.0 |
22 | 80.0 | 72.0 | 64.0 | 56.0 | 48.0 | 40.0 | 32.0 |
30 | 104.0 | 91.0 | 78.0 | 70.2 | 62.4 | 57.2 | 52.0 |
37 | 130.0 | 113.8 | 97.5 | 87.8 | 78.0 | 71.5 | 65.0 |
45 | 154.0 | 134.8 | 115.5 | 104.0 | 92.4 | 84.7 | 77.0 |
Mains operating voltage 400 V 3 AC | |||||||
0.37 | 1.3 | 1.3 | 1.3 | 1.3 | 1.3 | 1.2 | 1.0 |
0.55 | 1.7 | 1.7 | 1.7 | 1.6 | 1.5 | 1.4 | 1.2 |
0.75 | 2.2 | 2.2 | 2.2 | 2.0 | 1.8 | 1.5 | 1.3 |
1.1 | 3.1 | 2.9 | 2.8 | 2.5 | 2.2 | 1.9 | 1.6 |
1.5 | 4.1 | 3.7 | 3.3 | 2.9 | 2.5 | 2.1 | 1.6 |
2.2 | 5.9 | 5.6 | 5.3 | 4.7 | 4.1 | 3.5 | 3.0 |
3.0 | 7.7 | 6.9 | 6.2 | 5.4 | 4.6 | 3.9 | 3.1 |
4.0 | 10.2 | 9.2 | 8.2 | 7.1 | 6.1 | 5.1 | 4.1 |
5.5 | 13.2 | 11.9 | 10.6 | 9.2 | 7.9 | 6.6 | 5.3 |
7.5 | 19.0 | 18.1 | 17.1 | 15.2 | 13.3 | 11.4 | 9.5 |
11.0 | 26.0 | 23.4 | 20.8 | 18.2 | 15.6 | 13.0 | 10.4 |
15.0 | 32.0 | 30.4 | 28.8 | 25.6 | 22.4 | 19.2 | 16.0 |
18.5 | 38.0 | 34.2 | 30.4 | 26.6 | 22.8 | 19.0 | 15.2 |
22 | 45.0 | 40.5 | 36.0 | 31.5 | 27.0 | 22.5 | 18.0 |
30 | 62.0 | 58.9 | 55.8 | 49.6 | 43.4 | 37.2 | 31.0 |
37 | 75.0 | 67.5 | 60.0 | 52.5 | 45.0 | 37.5 | 30.0 |
45 | 90.0 | 76.5 | 63.0 | 51.8 | 40.5 | 33.8 | 27.0 |
55 | 110.0 | 93.5 | 77.0 | 63.3 | 49.5 | 41.3 | 33.0 |
75 | 145.0 | 112.4 | 79.8 | 68.9 | 58.0 | 50.8 | 43.5 |
90 | 178.0 | - | - | - | - | - | - |
110 | 205.0 | - | - | - | - | - | - |
132 | 250.0 | - | - | - | - | - | - |
160 | 302.0 | - | - | - | - | - | - |
200 | 370.0 | - | - | - | - | - | - |
Mains operating voltage 500 V 3 AC | |||||||
0.75 | 1.4 | 1.2 | 1.0 | 0.8 | 0.7 | 0.6 | 0.6 |
1.5 | 2.7 | 2.2 | 1.6 | 1.4 | 1.1 | 0.9 | 0.8 |
2.2 | 3.9 | 2.9 | 2.0 | 1.6 | 1.2 | 1.0 | 0.8 |
4.0 | 6.1 | 4.6 | 3.1 | 2.4 | 1.8 | 1.5 | 1.2 |
5.5 | 9.0 | 6.8 | 4.5 | 3.6 | 2.7 | 2.3 | 1.8 |
7.5 | 11.0 | 8.8 | 6.6 | 5.5 | 4.4 | 3.9 | 3.3 |
11.0 | 17.0 | 12.8 | 8.5 | 6.8 | 5.1 | 4.3 | 3.4 |
15.0 | 22.0 | 17.6 | 13.2 | 11.0 | 8.8 | 7.7 | 6.6 |
18.5 | 27.0 | 20.3 | 13.5 | 10.8 | 8.1 | 6.8 | 5.4 |
22 | 32.0 | 24.0 | 16.0 | 12.8 | 9.6 | 8.0 | 6.4 |
30 | 41.0 | 32.8 | 24.6 | 20.5 | 16.4 | 14.4 | 12.3 |
37 | 52.0 | 39.0 | 26.0 | 20.8 | 15.6 | 13.0 | 10.4 |
45 | 62.0 | 52.7 | 43.4 | 40.3 | 37.2 | 32.6 | 27.9 |
55 | 77.0 | 67.4 | 57.8 | 52.0 | 46.2 | 42.4 | 38.5 |
75 | 99.0 | 84.2 | 69.3 | 64.4 | 59.4 | 52.0 | 44.6 |
Compliance with standards
CE marking
The MICROMASTER inverters meet the requirements of the Low-Voltage Directive 73/23/EEC.
Low-voltage directive
The inverters comply with the following standards listed in the Official Journal of the European Communities:
- EN 60 204
Safety of machinery, electrical equipment of machines
- EN 61 800-5-1
Electrical power drive systems with variable speed - Part 5-1: Requirements regarding safety - electrical, thermal and energy requirements
Machine directive
The inverters are suitable for installation in machines. Compliance with the machine directive 89/392/EEC requires a separate certificate of conformity. This must be furnished by the plant constructor or the installer of the machine.
EMC directive
- EN 61 800-3
Variable-speed electric drives
Part 3: EMC product standard including special test procedure.
The new EMC product standard EN 61 800-3 applies to electrical drive systems as of July 1, 2005. The transition period for the preceding standard EN 61 800-3/A11 dated February 2001 ends on October 1, 2007. The following explanations apply to frequency inverters of the 6SE6 series from Siemens:
- The EMC product standard EN 61 800-3 does not apply directly to a frequency inverter but to a PDS (Power Drive System), which comprises the complete circuitry, motor and cables in addition to the inverter.
- As a rule, frequency inverters are only supplied to qualified technical specialists for installation in machines or plants. A frequency inverter must therefore only be considered as a component which, as such, is not subject to the EMC product standard EN 61 800-3. However, the inverter''s instruction manual specifies the conditions under which the product standard can be complied with if the frequency inverter is expanded to become a PDS. For a PDS, the EMC directive in the EU is complied with through observance of the product standard EN 61 800-3 for variable-speed electrical drive systems. The frequency inverters on their own do not generally require marking according to the EMC directive.
- The new EN 61 800-3 of July 2005 no longer distinguishes between "general availability" and "restricted availability". Instead, different categories, namely C1 to C4, are defined according to the environment of the PDS at the place of use:
- Category C1:
Drive systems for rated voltages of < 1000 V for use in the first environment - Category C2:
Fixed-location drive systems which are not connected by means of plug-in devices, for rated voltages of < 1000 V. if used in the first environment, installation and start-up may only be carried out by qualified EMC personnel. Warning information must be provided. - Category C3:
Drive systems for rated voltages of < 1000 V, solely for use in the second environment. Warning information must be provided. - Category C4:
Drive systems for rated voltages of ≥ 1000 V or for rated currents of ≥ 400 A or for use in complex systems in the second environment. An EMC plan must be drawn up.
- Category C1:
- In the EMC product standard EN 61 800-3, limits for conducted interference voltages and radiated interference are also indicated for the so-called "second environment" (= industrial power supply systems which do not supply households). These limits are lower than the limits of filter class A according to EN 55 011. The use of unfiltered inverters in an industrial environment is permissible provided they are part of a system that is equipped with line filters on the higher-level infeed side.
- With MICROMASTER, power drive systems (PDS) which comply with EMC product standard EN 61 800-3 can be installed (see the installation instructions in the product documentation). The table entitled "Overview of MICROMASTER components and PDS categories" and the MICROMASTER ordering documents show which components the respective PDS installation supports directly.
- In general, a distinction must be made between the product standards for electrical drive systems (PDS) of the EN 61 800 series of standards (of which Part 3 covers EMC topics) and the product standards for devices/systems/machines etc. This will probably not result in any changes in the practical use of frequency inverters. Since frequency inverters are always part of a PDS and the latter is part of a machine, the manufacturer of the machine must observe various standards depending on the type of machine and the environment, e.g. EN 61 000-3-2 for power supply harmonics and EN 55 011 for radio interference. The PDS product standard alone is therefore inadequate or irrelevant.
- With regard to compliance with limits for power supply harmonics, the EMC product standard EN 61 800-3 for PDS refers to compliance with the EN 61 000-3-2 and EN 61 000-3-12 standards.
- Irrespective of configuration with MICROMASTER and its components, the machine builder can also modify the machines in other ways in order to comply with the EMC directive of the EU. As a rule, the EMC directive of the EU is observed through compliance with the EMC product standards applicable to the machine. If they are not available, the generic standards such as DIN EN 61 000-x-x can be used instead. What is important is that the conducted interference and the radiated interference voltages at the power-supply connection point and outside the machine remain below the corresponding limits. What technical means are used to ensure this is not prescribed.
Overview of MICROMASTER components and PDS categories
|
|
---|---|
First environment
| Category C1 |
Category C2 | |
Second environment
| Category C2 |
Category C3 | |
Category C4 |
Electromagnetic compatibility
No inadmissible electromagnetic emissions occur if the installation instructions specific to the product are correctly observed.
The table below lists the results of measurements relating to the emissions and immunity to interference of MICROMASTER inverters.
The inverters were installed with shielded motor cables and shielded control cables in accordance with the directives.
EMC phenomenon | Relevant criteria | Limit value | |
---|---|---|---|
Emitted interference | Conducted via mains cable | 150 kHz to 30 MHz | Unfiltered devices, not tested. |
Emitted by the drive | 30 MHz to 1 GHz | All devices. | |
ESD immunity | ESD through air discharge | Test severity level 3 | 8 kV |
ESD through contact discharge | Test severity level 3 | 6 kV | |
Immunity to electrical fields | Electrical field applied to unit | Test severity level 3 80 MHz to 1 GHz | 10 V/m |
Immunity to burst interference | Applied to all cable terminations | Test severity level 4 | 4 kV |
Surge immunity | Applied to mains cables | Test severity level 3 | 2 kV |
Immunity to RFI emissions, conducted | Applied to mains, motor and control cables | Test severity level 3 | 10 V |
UL listing
UL and cUL listed power conversion equipment of UL category NMMS, in accordance with UL508C.
UL list number E121068 and E192450
For use in environments with pollution degree 2.
Also refer to the Internet at http://www.ul.com/