SINAMICS G180 Siemens
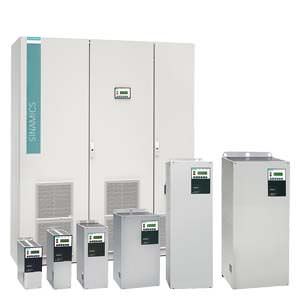
Область применения
The SINAMICS G180 is especially suited to applications in industries such as the
- chemical industry
- oil and gas industry
- power plant and utilities industries
- plastics industry
- process industry
- primary industry
- test bench systems
- conveyor systems
and for general mechanical engineering applications.
Обзор
The LOHER DYNAVERT T frequency converter integrated as SINAMICS G180 into the SINAMICS range has been deployed for over forty years for applications where maximum reliability and availability of the drive are of paramount importance.
SINAMICS G180 thus benefits from the many years of expertise acquired by LOHER Motors & Drives in the manufacture of motors and converters to the extent that the frequency converters are always systematically developed to take into account the requirements of the drive system as a whole.
SINAMICS G180 converters can be supplied for standard voltages 400, 500 and 690 V in the output range up to 6.6 MW. They are available as a compact unit, a cabinet system or a cabinet unit, with air or liquid cooling, for operation with synchronous and induction motors.
Output ranges of SINAMICS G180 (higher outputs with 400 and 500 V cabinet units available on request)
A wide range of add-on electrical components allow the drive system to be optimized for specific requirements. Configuring is greatly simplified by predefined interfaces and commissioning is speeded up by the preassignment of parameter settings at the factory.
The accuracy of the sensorless vector control makes the converter an ideal partner for many types of drives, such as those used for pumps, fans, centrifuges, presses, extruders or compressors, and an additional actual speed value encoder is therefore superfluous.
Appropriate encoder evaluation units are available for the SINAMICS G180 converters so that they can address applications that require an encoder for plant-specific reasons.
The SINAMICS G180 can be flexibly integrated into any automation concept whether it employs a conventional control or a bus system.
Apart from the standard converter interface (compliant with NAMUR NE37), the following can also be supplied as options to provide communication with the supervisory control system:
- PROFIBUS DP
- Modbus RTU
- Modbus TCP
- CANopen
- Ethernet (PROFIBUS DP with Ethernet-PROFIBUS converter)
Optionally available peripheral boards can be selected to add the following inputs/outputs to the converter:
- Digital and analog inputs and outputs
- 2 PTC thermistor inputs for ATEX-certified motor temperature monitoring for motors in hazardous zones (prewarning/trip)
Дизайн
Platform concept
All of the SINAMICS G180 versions are consistently based on an integrated, standardized, common, modular platform concept. Shared hardware and software components, as well as standardized tools for dimensioning, configuring and commissioning tasks ensure a high level of integration between all components.
All devices - from the lowest rating class in compact unit form to the largest version in the form of an air-cooled or liquid-cooled cabinet unit - have the same features with a virtually identical scope of functions.
All frequency converters in the SINAMICS G180 range operate with the Control Board. All Control Boards utilize the same firmware and all are operated via the Inverter Management Software IMS. Both the IMS and the firmware can be upgraded and downgraded as required to facilitate communication.
Функции
Power unit
- Complies with EMC guidelines defined in EN 61800‑3 thanks to line filter which is integrated as standard (with grounded supply system)
- Category C2 for compact units in TN/TT system of the first environment (residential area), category C1 available as an option
- Category C3 for cabinet units (TN/TT system) of the second environment (industrial area)
- Category C4 for compact and cabinet units in IT system of the second environment (industrial area)
- SINAMICS G180 converters cause minor line harmonics: Thanks to line reactors integrated in cabinet units and DC reactors integrated in compact units
- Output filter to permit the use of long motor cables for motors with standard insulation
- Insulation monitoring for IT systems integrated in 500/690 V units and ground fault monitoring for TN and TT systems integrated in 400 V units
- Wide range of input voltages
- Lower additional motor noise emissions of typically 3 dB(A) as well as minor losses in converter and motor thanks to optimized pulse pattern and converter clock frequency
- Units can be protected by standard fuses (gL characteristic)
- Standardized user interface on units rated from 2.2 to 6 600 kW
Control section
- High level of protection for personnel and plant is provided by protective separation of the safety extra-low voltage in accordance with IEC/EN 61800‑5‑1 at the analog and digital control inputs and outputs of the power unit.
Operation and settings
- Straightforward to operate and set by means of a menu-assisted, 4-line plaintext display with membrane keyboard on the converter unit or remotely from the control room via an RS485 link at a distance of up to 1000 m
- Extensive range of functions using a Windows-based PC operating program
Explosion protection
- ATEX-certified tripping concept in accordance with Directive 94/9 EC for the safe operation of motors in hazardous zones 1 and 2, which means that no main contactor is required
Safe Torque Off
Available with options G04, G05, G08
- Shutdown mechanism to prevent unexpected starting. Category 0 stop function in accordance with EN 60204‑1 (stop by disconnection of power supply to the machine).
- Functional safety in accordance with:
- SIL 2 as per EN 61508
- Category 3 to EN ISO 13849‑1
- Performance Level (PL) d to EN ISO 13849‑1
- Functional safety in accordance with IEC 61508: SIL 3 is possible in conjunction with options S01+Y11 or S02+Y11.
Communication
- Communication via conventional terminal strip with freely programmable digital and analog inputs/outputs with
- parameterizable limit value signals
- parameterizable timers
- parameterizable attenuators
- parameterizable converter behavior when inputs/outputs respond
- parameterizable logic elements
- Communication and parameterization by means of
- PC using IMS (Inverter Management Software) via USB interface
- External operator panel via RS485 link
- Bus systems such as Ethernet
(PROFIBUS with Ethernet-to-PROFIBUS converter board), PROFIBUS DP, CANopen, Modbus RTU or Modbus TCP
Drive behavior
- Closed-loop control of synchronous and induction motors
- Two control modes for induction motors:
- Space vector control for standard applications (without feedback)
- Field-oriented closed-loop control for dynamic requirements
- Optimum braking without any supplementary equipment by means of oversaturation control system. With approximately 10 % braking torque at high speed range and up to 50 % at low to medium speed range.
General
- Automatic slip compensation
- Stall protection provided by current limitation control
- Flying restart function for connection to rotating motor
- Automatic adjustment of the overload times
- Parameterizable DC braking for precise deceleration down to zero speed
- Torque control
- Automatic restart (Auto Restart)
- Voltage and current control systems
(AC as well as DC with variable frequency) - Mains supply backup is possible
- Integrated process controller for basic, higher-level closed-loop control tasks
- Optionally available integrated braking chopper for increased braking torque
- Operation of groups of units with interconnected DC links is possible
Особенности
- The converters are exceptionally quiet and compact thanks to state-of-the-art IGBT power semiconductors and an innovative cooling concept.
- The clock frequency is optimized to reduce system losses to a minimum.
- The "random pattern" function significantly reduces motor noise.
- Plant and system availability are increased by being able to quickly and simply replace power components.
- Essential spare parts can be requested at any time for any individual converter by means of the "SparesOnWeb" Internet tool.
- Optimized use of components reduces cabinet dimensions to a minimum.
- Easy integration into automation solutions via analog and digital interfaces. Number of interfaces can also be expanded through installation of an optional peripheral board.
- Data are transmitted over popular bus systems (PROFIBUS DP, CANopen, Modbus RTU or Modbus TCP)
- Fast, easy commissioning and parameterization using interactive menus on an operator panel with illuminated graphic LCD and plain-text display, or PC-supported using the IMS commissioning tool (Inverter Management Software).
- The entire production process is required to meet stringent quality standards and subject to extensive controls, thereby ensuring a high degree of functional reliability during installation, commissioning and operation.
Технические данные
Overview of data for SINAMICS G180 compact units, cabinet systems and cabinet units
Type | Converter |
---|---|
Output range | 2.2 to 6600 kW (3 to 8851 hp) |
Input voltage | 230 to 690 V AC (standard), 50/60 Hz |
Pulse number | 6-/12-/18-/24-pulse |
Type of cooling | Air-cooled and liquid-cooled |
Machine type | Induction motor, synchronous motor |
Дальнейшая информация
Quality management to DIN EN ISO 9001
SINAMICS G180 converters conform to the most exacting quality requirements. Comprehensive quality assurance measures in all development and production processes ensure a consistently high level of quality.
Of course, our quality management system is certified by an independent authority in accordance with DIN EN ISO 9001.